采用副边同步整流解决方案降低开关电源过热(一)

每月为您发送最具参考价值的行业文章
我们会保障您的隐私
介绍
当今世界,手机,笔记本电脑等移动设备正在改变着人们的生活。对于这些设备的适配器,人们总是希望能做到小巧轻便,充电快速。为此,各大厂商近期争相推出超小体积快充。
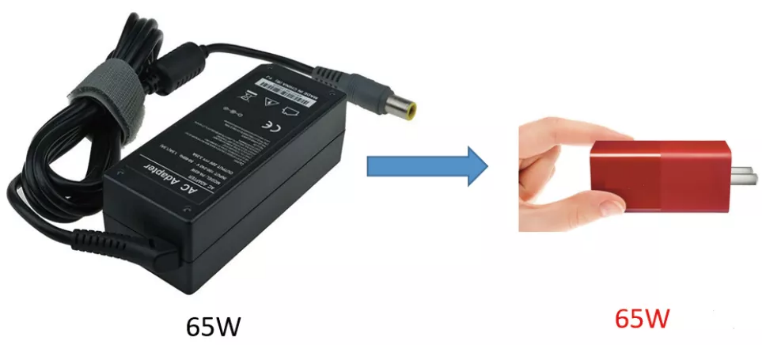
图1:适配器的发展历程
本文为如何为超小体积快充适配器设计副边同步整流器系列文章的第一篇。 第一篇将介绍副边同步整流的基本拓扑结构,以及对其供电的要求。 第二部分将介绍副边同步整流器的开通和关断过程以及快速关断技术。
同步整流拓扑
充电速度快意味着更大的输出电流和更多的发热。而体积小巧则意味着更小的散热面积。在这二者双重作用下,热的问题变得棘手。
图2为常用的反激拓扑,假定系统输出规格为5V 4A,那么流过副边二极管的平均电流是4A。假设二极管的导通压降是0.7V,在二极管上形成的导通损耗是2.8W,发热严重。系统在这种情况下长期工作,会严重影响可靠性和用户使用体验。
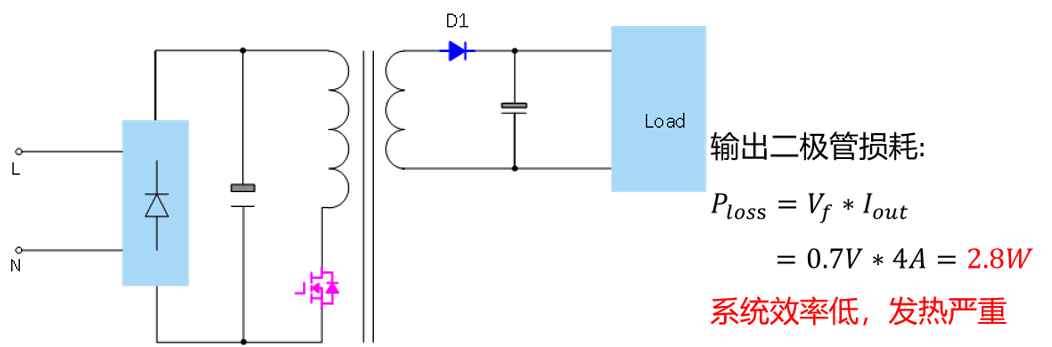
图2: 常用反激拓扑,发热严重
遇到这种问题,如果用MOS管代替副边输出二极管,当副边续流的时候把副边MOS管打开,使其工作在同步整流模式。由于MOS的导通阻抗很小,续流过程中发热量就很小。以导通阻抗10mΩ的MOS为例,当输出电流4A时,MOS导通损耗仅为0.16W。发热量被大大降低。
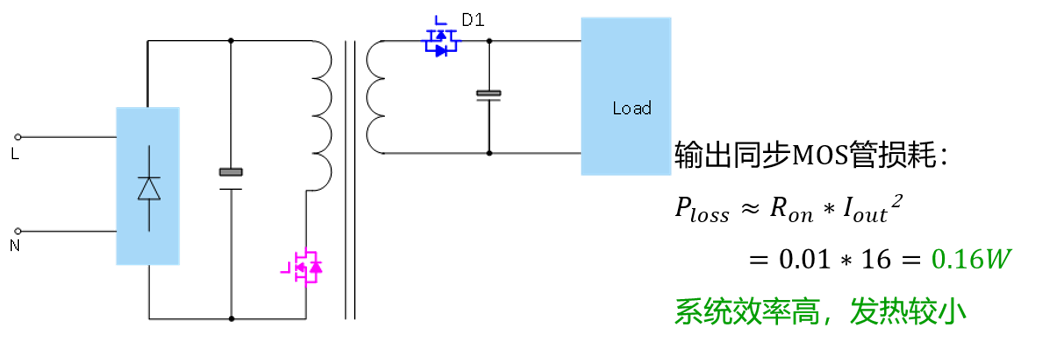
图3: 用MOS管替代,显著降低发热
同步整流如何实现供电
我们都知道,对于NMOS,如果要在续流的过程中将MOS管打开就需要在G上提供高于S的电压。而在续流的过程中,副边的最高电压就是S点的电压。
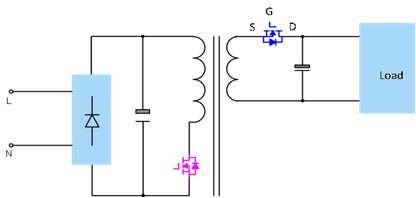
图4:续流过程中打开MOS管,G点上电压需高于S点
我们可以想到用辅助绕组,如图5采用额外的绕组给副边MOS的驱动供电。但这种方式需要增加一个变压器绕组和驱动电路,增加的系统的复杂度和成本。
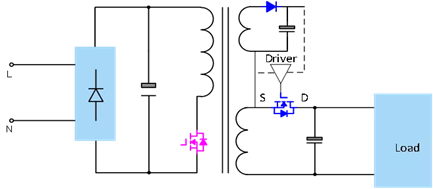
图5: 辅助绕组可提供高于S点的电压
那么,有没有不需要辅助绕组的方案呢?如上图,如果我们把MOS管放到副边输出的低端,可以借助输出电压给MOS管供电。这种方式看似完美,但实际上MOS放在低端往往会造成系统的EMI表现更差。同时如果输出电压较低,就不足以为MOS的驱动提供足够的电压,因此无法在低压输出场合应用。
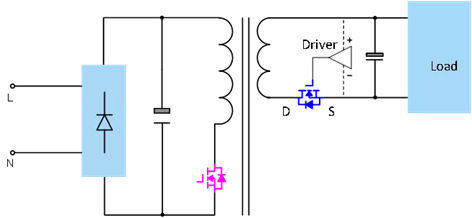
图6: MOS管放到副边输出的低端
其方案的设计要点是既不需要辅助绕组,又能适应不同输出电压应用,同时也要保证系统EMI表现较好。MP9989, 集成了CCM(连续导通)和DCM(断续导通)模式的反激二极管,可以实现这样的设计(图7)。
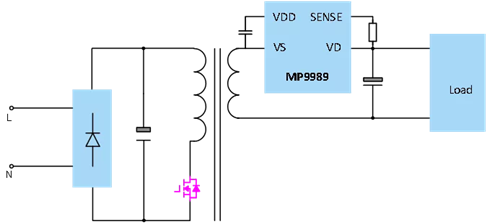
图7: MP9989 提供了系统EMI 性能
MP9989,它可以直接放在输出的高端,可支持低压输出,并且外围电路非常简单,我们称之为理想二极管,MP9989关键优势就是它里面的自供电电路。
当原边MOS打开时,MP9989的MOS管反向截止(图8),此时(VDS)出现正压,MP9989内部的自供电电路会给VDD电容充电。当原边MOS关断时,由于VDD电容已经被储能,此时VDD可以为驱动电路供电,保证副边MOS的顺利打开。
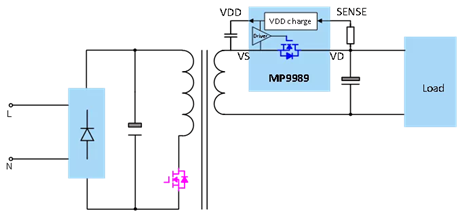
图8: 内部自供电电路给 VDD 电容充电
随着USB PD越来越普及,输出的电压范围越来越宽。较高的输出电压会给芯片的耐压带来挑战。而MP9989内置100V的MOS,为宽范围设计提供足够裕量。
结论
在本文中,我们使用MP9989提供了一款副边同步整流设计方案,可以成功导通MOS管同时还能减少发热。第二篇我们将解释同步整流器的开通和关断的过程,同时探讨快速关断技术的优势。
_______________________
您感兴趣吗?点击这里,可直接联系我们获取最具价值的资源 - 每月为您推送!
直接登录
创建新帐号