汽车电子中的电磁干扰生成、传播与抑制(上)

每月为您发送最具参考价值的行业文章
我们会保障您的隐私
基于安全性的考虑,汽车行业对电磁干扰 (EMI)有严格的要求,这给工程师带来了很大的设计挑战(见图 1)。降低 EMI需要对各种 EMI 问题进行建模与分析。本文提供的建模和抑制方法用来降低非隔离式变换器(例如降压、升压和升降压换器)中的 EMI。
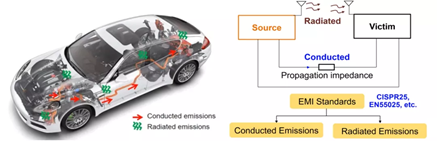
图 1:汽车电子中的传导和辐射EMI
电力电子系统中的许多组件(例如 MOSFET 和二极管)在高频开关期间会产生高 dv/dt 节点和高 dI/dt 环路。这些高 dv/dt 和 dI/dt 值就是EMI产生的根本原因。EMI分为传导EMI 噪声和辐射EMI噪声。传导 EMI是由导体之间的物理接触引起的,而辐射EMI则由感应引起,即使导体不接触也会产生。由于两种EMI 传播路径差别很大,所以我们分别讨论两种EMI噪声。本文将侧重传导 EMI,而下一篇文章将讨论辐射EMI。
传导EMI
传导 EMI 分为差模 (DM) 噪声和共模 (CM)噪声。相应地,对DM噪声和CM噪声应分别建模,以说明它们不同的传播路径和抑制机制。我们采用噪声分离器来获取测量结果,同时区分是DM还是CM导致了大部分的EMI噪声。
DM噪声主要在两线之间流动,而CM电流则以位移电流的形式流向大地。该位移电流经过设备与地之间的电容器,然后流回电网(见图 2)。
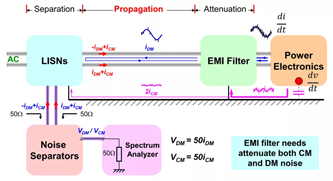
图2: 传导EMI中的CM噪声和DM噪声
EMI建模的第一步是将开关用作等效的电流或电压源,之后电流和电压在整个电路中保持恒定。然后,使用叠加定理来详细分析每个源的影响。图 3 显示了如何简化降压变换器的 DM模型。当然,也可能有其他非隔离式变换器的模型。
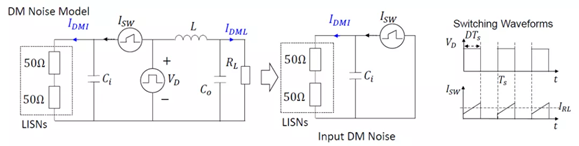
图 3:降压变换器的DM噪声模型和典型开关波形
图 4 显示了如何简化降压变换器的CM模型。
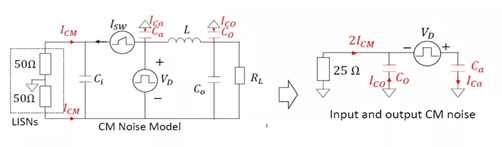
图 4:降压变换器的CM噪声模型和典型开关波形
谨慎选择输入电容器和输入滤波器可以降低降压变换器中的DM噪声;而利用滤波器最小化开关节点的面积可以降低CM噪声。
图 5 显示了分离并测量降压变换器DM噪声和CM噪声的结果。在本例中,DM噪声是EMI的主要成因。
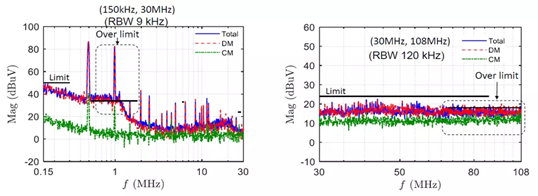
图 5:降压变换器的整体DM和CM噪声测量
增加DM 滤波器可以降低 EMI,图6所示的噪声测量结果展现了良好的EMI 优化成果。该原理也可扩展至其他DM噪声过多的变换器。
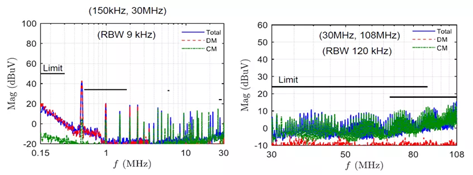
图6: 降压变换器的噪声消减
EMI性能优化的汽车降压变换器
MPS的MPQ4423C-AEC1是一款优化了传导EMI性能的同步整流降压开关模式变换器。它采用侧面镀锡封装,集成功率 MOSFET 并采用同步模式操作,以提高输出电流的效率。
在强制脉宽调制 (PWM) 模式下工作时,MPQ4423C-AEC1能够保持较低的传导EMI辐射(见图 7)。
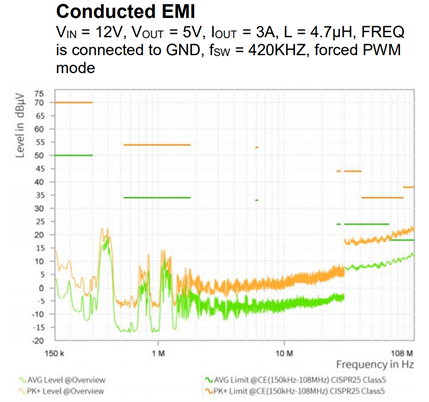
图7: MPQ4423C-AEC1的传导EMI性能
MPQ8873-AEC1是另一款非常适合汽车应用的4开关降压-升压变换器。MPQ8873-AEC1 具有可配置的参数,包括可调频率展频(FSS),它周期性地抖动开关频率 (fSW) 以提升EMI性能。MPQ8873-AEC1还采用专用寄存器来启用FSS、调整FSS调制范围并设置 FSS 调制频率。图 8显示了平均传导 EMI测量结果。
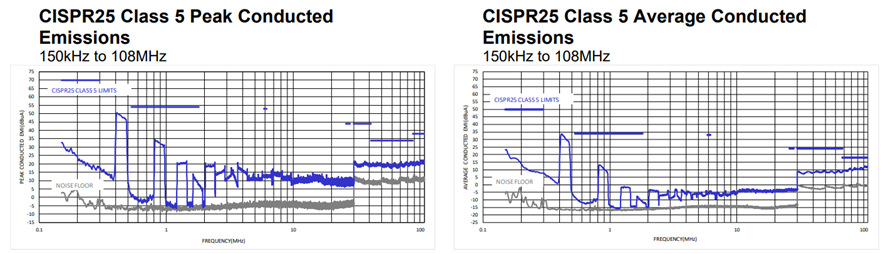
图 8:MPQ8873-AEC1 的传导 EMI性能
结论
本文回顾了控制传导 EMI 噪声以满足标准要求的方法,具体包括如何对DM噪声和CM噪声分别建模,并针对不同的应用来降低EMI,同时强调了针对汽车设备如何控制传导EMI以实现峰值效率。
下一篇文章 将利用戴维南定理深入探讨辐射EMI问题的更多细节,戴维南定理可以实现变换器和天线的建模以控制EMI噪声。
_______________________
您感兴趣吗? 点击这里,可直接联系我们获取最具价值的资源 - 每月为您推送!
技术论坛
Latest activity 8 months ago
10 回复
Latest activity 9 months ago
4 回复
Latest activity 6 months ago
10 回复
直接登录
创建新帐号