高度集成的电池充电器 IC 用例:扫地机器人

每月为您发送最具参考价值的行业文章
我们会保障您的隐私
本用例将介绍MPS全集成开关充电 IC 在扫地机器人中的应用。
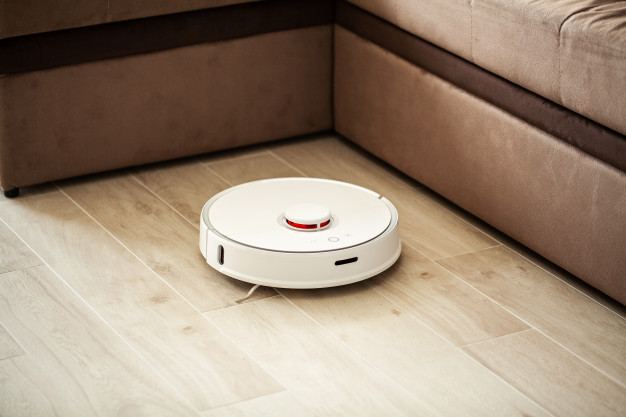
扫地机器人需要多电池充电IC来供电。由于市场对成本极为敏感,有些设计采用 MCU 和外部组件来构建自己的分立式解决方案,而不是采用专用充电 IC。
MP2759是一款高度集成的开关充电IC,专为采用 1 至 6 节串联锂离子、锂聚合物和磷酸铁锂电池组的充电应用而设计。该 IC 将三个功率 MOSFET 以及模拟控制电路集成到一个 3mmx3mm 的封装中,只需很少外部元器件即可安全、可靠地运行。
传统分立式解决方案至少需要两个功率 MOSFET 用于充电IC的 DC/DC 变换器:一个功率 MOSFET 用于防止电池电量回流到输入端;另一个 MOSFET 则用于电池的电源路径管理功能(如果需要)。而且,包含采样电路、补偿电路、PWM 发生器和驱动器的控制回路也必不可少。另外,系统还需要适当电路来提供保护功能、输入源指示或操作条件的变化指示,以及其他功能。
这些分立的元件使设计过程变得复杂,它不仅不具备充电可编程性,而且充电精度低、电路板尺寸大。
采用MP2759充电解决方案则具有以下优势:
- 不涉及软件:这是一种自主充电解决方案,它不需要MCU 代码,构建和验证的时间更短。
- 更小的电感:低开关频率需要大电感。MP2759 具有较高开关频率(高达 700kHz),因此所需电感尺寸较小。而集成 FET又进一步减小了解决方案尺寸。
- 充电速度更快:现有MCU 解决方案需要较长时间来充电,因为低效率需要电流更低。MP2759则集成了低 RDS(ON) MOSFET,可以支持更大的充电电流,散热性能也更加出色。
- 精度更高:分立式MCU 充电解决方案的电流和电压调节精度较差。将电池充电至满电压(例如每节电池 4.2V)对于最大化电池容量非常重要,但却不能超过满电压以避免造成安全问题。MP2759 的高精度电流和 0.5% 的电压调节精度意味着电池可以更快、更安全地充至更高容量;扫地机器人将能够在每次充电后更快地返回清洁并运行更长时间。
其他功能:
- 可调输入限流调节
- 可调电池充电温度范围
- 采用 JEITA 配置的电池温度监测和保护
- 高达 36V 的工作输入电压和 40V 保护
- 高达 3A 的可调充电电流
- 支持多达 6 节电池串联,每节电池都具有 3.6V/4.0V/4.1V/4.15V/4.2V/4.35V/4.4V 电池调节电压
- MPPT 的最小输入电压调节
- 支持“或”选择电源路径管理,以实现在电池电量不足时即时启动
- 0.5% 的电池调节电压精度
- 450kHz 或 700kHz 开关频率
- 集成反向阻断 FET 和降压开关 FET
- 内部环路补偿
- 充电操作指示
- 输入状态指示
- 电池过压保护
- 充电安全定时器
- 芯片过温保护
相关内容
-
文章
用于多锂离子/锂聚合物电池充电器的集成解决方案
与传统解决方案相比,全集成解决方案具有极高的效率、丰富的安全功能、低BOM成本和更短的设计周期。本文介绍的MPS MP2759,展示了集成解决方案的优势。该方案包括三个低导通电阻功率MOSFET、模拟控制环路以及保护和指示等辅助功能,它可以帮助设计人员通过简单的外部电路实现电源路径管理和实时充电电流调节。
-
应用
机器人技术
MPS提供高效、可靠、创新且应用广泛的解决方案,可简化机器人设计周期并缩短上市时间。我们帮助设计师提高速度、传感和控制,以优化生产,从而配备新的机器人技术以满足今天的需求,同时解决未来可能的问题。
-
用例
高集成度电池充电器 IC 用例:备用电池系统
在本用例中,我们将全集成开关充电器 IC用于备用电池系统。
-
参考设计
利用数字 PWM 信号调节 ICC 的实现方法
本参考设计展示了一种利用 MCU 发出的 PWM 信号实时调整充电电流的方法。
直接登录
创建新帐号