磁位置传感器在机器人技术中的核心作用

每月为您发送最具参考价值的行业文章
我们会保障您的隐私
简介
机器人是一种动态技术,实时反馈、精度和准确性非常重要。磁位置传感器正是确保机器人实现这些特性的关键元件。本文将通过实际案例探讨磁位置传感器在机器人技术中的应用价值及其多样的应用。
磁位置传感器的重要性
磁位置传感器在机器人领域发挥着关键的作用,它能够精确检测并量化机器人部件的位置、速度和定向,而且坚固耐用,能够适应严苛的工业环境。
磁位置传感器是一种非接触式传感器,无需物理接触被测物体即可确定其位置,因此可减少磨损并延长传感器与机器人部件的使用寿命。它能够测量线性和旋转运动,具有高度适应性,并可提供实时反馈,这些功能对机器人系统的动态控制都至关重要。其紧凑的尺寸也适用于空间有限的机器人构造。而且,通过提供精确的位置数据,这些传感器能有效防止可能导致机器人或其周边环境受损的意外动作。
机器人技术中的磁位置传感器类型
霍尔效应传感器
霍尔效应传感器在机器人技术中常用于电机转速测量、位置检测和接近感测。其工作原理基于以下前提:磁场的存在会导致导体中的电荷发生移动。通过测量沿磁场方向产生的电势差,即可检测电荷位移量。
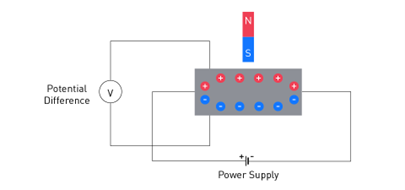
图1:霍尔效应原理
磁阻效应则不同:当存在外部磁场时,磁阻材料的电阻值发生变化。
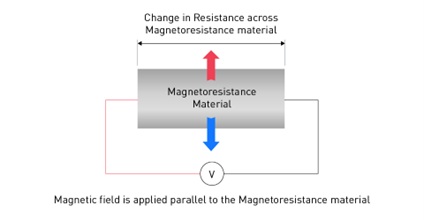
图2:磁阻效应原理
在磁阻效应中,磁通量方向与激励电流平行;霍尔传感中,磁通量方向垂直于激励电流。此外,受外部磁场影响时,霍尔传感器产生电压,而磁阻材料则改变其电阻值。
电感式传感器
电感式传感器可用于检测机器人附近的金属物,该技术也应用于金属探测器、交通信号灯和洗车设备等。
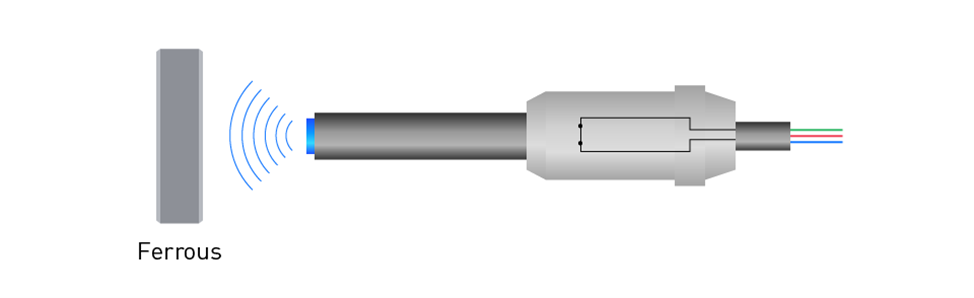
图3:电感式传感原理
当金属物干扰振荡磁场时,基于涡流效应会产生反向磁场,导致激励场衰减,电感式传感器可即时检测到这种变化。
磁位置传感器在机器人技术中的多样化应用
工业机器人
在焊接、装配和物料搬运等作业中,工业机器人高度依赖磁位置传感器实现机械臂的精确移动和定位。这些传感器能够提供机械臂位置和定向的实时反馈,确保作业精度和质量。
自动导引车 (AGVs)
自动导引车(AGV)应用,例如仓储机器人,通过磁位置传感器追踪地面磁条,实现快速精准的移动。库存管理效率可以得到大幅提升,维护成本也大幅降低。
手术机器人
医疗领域的手术机器人利用磁位置传感器精确控制手术器械,使外科医生能以更小创面完成复杂的手术,显著改善患者预后。
无人机和自动驾驶车辆
自动驾驶车辆和无人机通过磁位置传感器来维持稳定性和控制力,让设备能够感知姿态与航向的变化,实现安全、高效地导航。
机器人假肢和外骨骼
磁位置传感器在该应用中可用于辅助追踪运动。传感器的实时数据使各部件能够响应用户的意愿,并以更自然、更直观的方式移动。
服务型机器人
服务型机器人借助磁位置传感器实现环境导航。例如扫地机器人利用磁位置传感器实现避障和高效清洁,成为维护家居及商业场所干净卫生的有效工具。
教学机器人
磁位置传感器还可用于教学机器人。通过演示运动控制与反馈原理,为学生提供理解机器人和自动化基础知识的实践学习平台。
结语
磁位置传感器在机器人技术的众多应用中具有不可替代的作用。它可以提供精确实时的位置和定向数据,是提升机器人系统精度与效率的核心工具。随着机器人技术的发展,磁位置传感器的重要性不断凸显。其精度、稳健性、适应性和实时反馈特性将不断推动其在机器人领域的普及,并影响这一前沿产业的发展轨迹。
_______________________
您感兴趣吗? 点击订阅,我们将每月为您发送最具价值的资讯!
直接登录
创建新帐号