Introduction to Linear Motors
Basic Principles and Differences from Rotary Motors
Conventional rotary motors generate rotational motion, but linear motors produce motion in a straight line. Linear motors are a kind of electric motor that produces motion in a straight line. The same laws of electromagnetism that regulate rotary motors are responsible for this direct linear motion; nevertheless, the layout and operation of the two types of motors are fundamentally different. A linear motor generates force linearly down its length through the interaction of the magnetic field and electrical current, unlike a rotational axis. The application of this design avoids the requirement for extra mechanisms to convert rotary motion to linear motion, such as belts, gears, or screw drives. This design effectively converts electrical energy into mechanical motion.
Historical Development and Technological Evolution
Since the 19th century, researchers have been investigating the possibility of linear motion using electromagnetic principles. However, it was not until the later half of the 20th century that technological developments made it possible to implement linear motors in practical settings. Transportation systems, like maglev trains, were primarily focused on early innovations, utilizing linear motor technology for propulsion without physical contact with the rail. This enabled the trains to travel at high speeds while requiring less maintenance.
Improvements in control systems and power electronics, as well as advancements in materials science, have been the driving forces behind the technological evolution of linear motors. Magnets and conductors have been particularly important parts of this growth. The development of these innovations has made it possible to manufacture linear motors that are more compact, efficient, and powerful, making them suited for a wide variety of industrial applications. Today, a variety of sectors that require accurate linear movement utilize linear motors. These fields include automated assembly lines, medical equipment, and high-speed transportation systems, among others.
The progression of linear motor technology from conceptual investigation to extensive practical use is a reflection of the ongoing innovation in this field. The role that linear motors play in modern automation and motion control systems is expected to expand as control systems become more sophisticated and materials become more advanced. Linear motors are expected to deliver improved performance, precision, and efficiency in situations where direct linear motion is critical.
Design Characteristics of Linear Motors
Linear motors are distinguished from other types of motors by their unique components and operation, which allows them to move in a linear fashion. In order to fully appreciate the versatility and adaptability of linear motors across a wide range of applications, it is critically important to have a solid understanding of these features.
Key Components
The three major components that make up linear motors are as follows:
Primary Part (Mover): Similar to the rotor in a rotary motor, this component houses the motor's windings or magnets. It is the component of the linear motor that is in motion, and it is responsible for producing force and motion along a linear route.
Secondary Part (Stator): In contrast to rotary motors, a linear motor's secondary portion is stationary. It often consists of magnets or a ferromagnetic structure, and it is this combination that interacts with the primary part to generate motion. This component may consist of a single piece or a sequence of pieces aligned along the motion path.
Magnetic Tracks: Some types of linear motors use magnetic tracks to direct and improve the magnetic flux interaction between the primary and secondary components. This makes the system more efficient and better at controlling motion.
Low vs. High Acceleration Linear Motors
Different linear motors can be constructed for applications that require low or high acceleration, depending on the purpose for which they are intended:
- In the realm of precision machining or assembly processes, where accuracy is of utmost importance, low-acceleration linear motors are specifically designed to function optimally for applications that require both steady and controlled motions.
- High Acceleration linear motors are specifically intended for applications that require quick movement, such as in sorting systems or high-speed packing lines. The capacity of these motors to rapidly change speeds is one of their defining characteristics. This ability allows them to offer flexibility and efficiency in dynamic environments.
Types of Linear Motors
There are many different types of linear motors, each tailored for a specific application and offering a unique set of benefits.
- Synchronous linear motors are characterized by the utilization of permanent magnets in the mover, which are controlled by an alternating current in the stator unit. Due to the fact that they are known for their high efficiency and precision, they are perfect for applications that require precise placement and control.
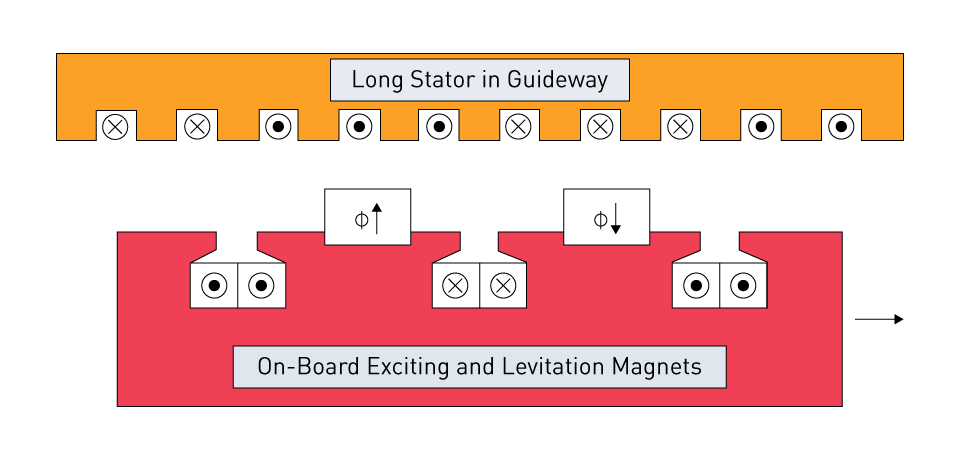
Figure 1: Example Construction of Synchronous Linear Motor
- Induction linear motors function according to the concept of electromagnetic induction, with the secondary component commonly consisting of a conducting plate. These motors are ideal for applications in which durability and simplicity are more important than precise control, because they are well-suited for such applications.
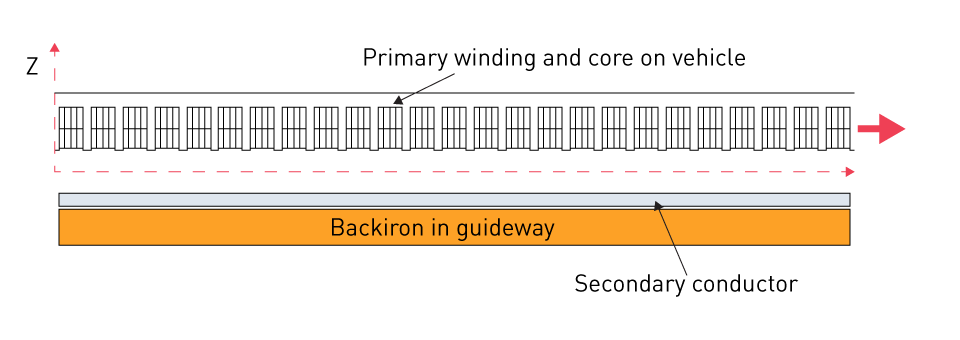
Figure 2: Example Construction of Induction Linear Motor
- Homopolar linear motors are characterized by a single magnetic route and direct current. In comparison to other varieties, they are far less prevalent, but they provide simplicity and dependability for applications that are specialized for a niche market.
- Tubular linear motors are characterized by their cylindrical construction, which encloses the magnetic field within the structure, boosting both efficiency and force density. For applications that require high force in a small footprint, this design is advantageous because of its compact size.
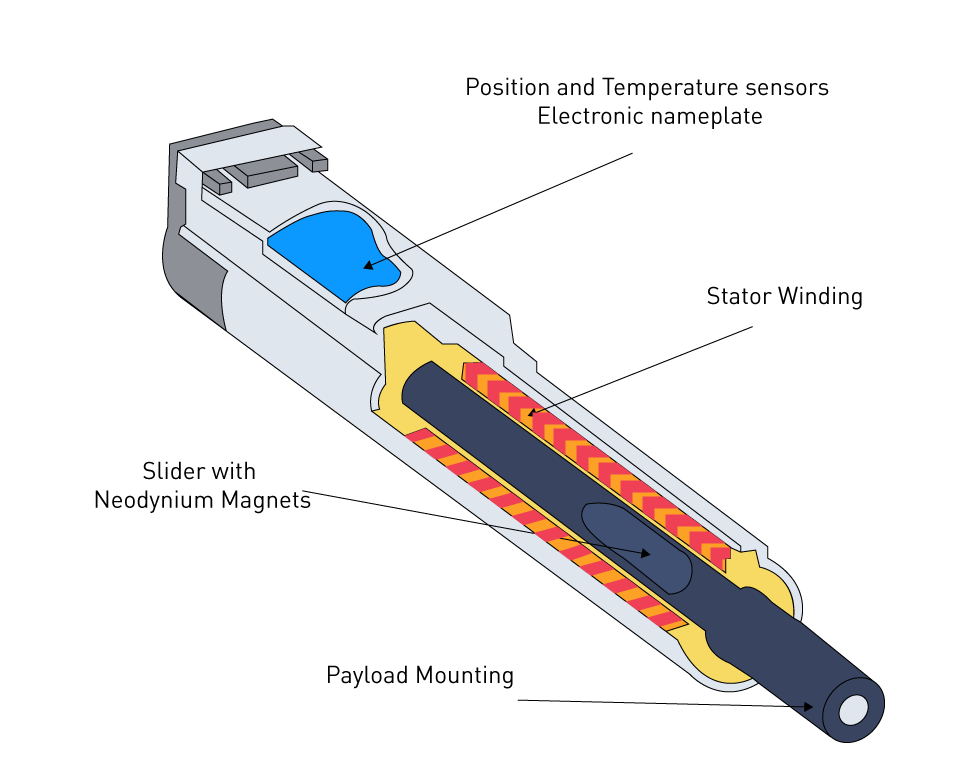
Figure 3: Example Construction of Tubular Linear Motor
- Piezoelectric linear motors employ piezoelectric materials, which change their shape in response to an electric field, thereby generating motion. Applications such as medical devices and optical equipment utilize these motors to perform movements that are exceedingly accurate and limited in scale.
Applications of Linear Motors
Many industries use linear motors to provide direct linear motion, leveraging their unique qualities. The use of linear motor technology in a variety of disciplines exemplifies its versatility and effectiveness in meeting specific industrial applications requirements.
Industrial Applications: Automation, Precision Machining, Transportation
Automation: In the field of factory automation, linear motors drive conveyor systems, robotic arms, and assembly lines. These motors enable high speeds, precise control, and flexibility in movement. Because of their capacity to start, stop, and reverse direction in a short amount of time, automated processes are able to function more efficiently, which in turn contributes to greater production and decreased operational expenses.
Precision Machining: Machining with precision Linear motors are an essential component in the process of precision machining, which includes the use of CNC (Computer Numerical Control) machining centers, laser cutting machines, and EDM (Electrical Discharge Machining) equipment. The creation of parts with tight tolerances and outstanding surface finishes is essential in the manufacturing of aircraft, automotive, and medical device components. Linear motors provide a high level of precision and smooth motion control, enabling the production of these parts.
Transportation: The transportation industry, specifically in maglev (magnetic levitation) trains, utilizes linear motors for propulsion, one of their most notable applications. The elimination of physical contact between the train and the track allows maglev trains to achieve lower friction, which in turn makes rides smoother, quieter, and more comfortable at higher speeds. This demonstrates the potential of linear motor technology to alter mass transportation systems.
Specific Uses in High-Speed and High-Precision Environments
Linear motors are ideal for applications that require rapid and precise sorting, such as those found in postal sorting facilities and distribution centers. High-Speed Sorting Systems: Linear motors are ideal for these applications. They are able to quickly accelerate and decelerate, enabling them to achieve high throughput rates, which are essential for satisfying the requirements of operations in the logistics and e-commerce industries.
Medical and Laboratory Equipment: The medical industry uses linear motors to move diagnostic imaging equipment, like magnetic resonance imaging (MRI) scanners, with the precision and smoothness necessary for capturing high-quality images. Moreover, laboratories utilize them in their automation equipment for the meticulous and accurate handling of samples.
Semiconductor Manufacturing: The manufacturing of semiconductors requires a high level of precision and cleanliness. Linear motors are used to drive the stages of lithography equipment and wafer handling systems. These motors eliminate the impurities that are commonly associated with traditional mechanical systems, allowing them to provide the necessary level of accuracy and purity for these critical procedures.
Advantages and Limitations
Comparison with Traditional Rotary Motors
The primary reason why linear motors offer a different set of advantages over typical rotary motors is their ability to generate motion directly in a straight line without the need for extra mechanical components to transform rotational action into linear motion. The direct action in question results in a number of advantages:
Increased Efficiency: Linear motors eliminate mechanical transmission devices such as gears and belts, resulting in a reduction in energy losses caused by friction and wear. This, in turn, leads to an increase in the overall efficiency of the system.
Enhanced Precision and Control: Enhanced precision and control Linear motors are able to achieve greater precision and control in positioning and speed, which is critical for applications that require extremely precise motion profiles. The absence of mechanical play or backlash, which is inherent in conversion systems, is a significant factor contributing to this greater precision.
Simplified Maintenance: Because linear motors have fewer moving parts and no contact elements, they require less maintenance. This results in less downtime and lower operational expenses. This simplicity also leads to a longer lifespan and improved reliability.
Challenges in Implementation and Operation
In spite of the fact that they have many benefits, linear motors are also subject to a number of obstacles that might impact their implementation and operation.
Cost Considerations: Because linear motors require more complex control systems and components with a higher degree of precision, their initial cost may be higher than that of their rotary counterparts. This is due to the need for high-precision components. One of the potential obstacles to adoption is the cost element, particularly in applications that are sensitive to cost.
Thermal Management: Although linear motors have high efficiency in general, they might present difficulties in terms of thermal management. This is especially true for linear motors that are substantially longer than average. The direct linear motion has the potential to concentrate heat in specific regions, necessitating the implementation of sophisticated cooling systems to avoid overheating and ensure consistent performance.
Integration Complexity: Integrating linear motors into pre-existing systems or designs not originally intended for them can pose integration challenges. It is necessary to give significant thought to the physical and electrical integration of linear motors into machinery and control systems due to the fact that linear motors have a distinctive form factor and manner of functioning.
Space Requirements: Depending on the application, linear motors may demand more space than identical rotary motors, particularly for long travel lengths. Long-distance travel particularly highlights the need for a linear motor. In tight locations, one of the characteristics that can be a hindrance is the requirement to fit the complete length of motion within the motor structure.
直接登录
创建新帐号