Fundamentals of Piezoelectric Motors
Operating Principles of Piezoelectric Motors
Using the piezoelectric effect, which is a phenomenon in which certain materials generate an electric charge in response to the application of mechanical stress, piezoelectric motors are able to function appropriately. Conversely, the application of an electric field enables certain materials to alter their shape or size. Piezoelectric motors utilize this dynamic ability to generate motion. In contrast to traditional electromagnetic motors, which generate motion through the application of magnetic fields, piezoelectric motors generate motion through the physical deformation of piezoelectric materials. Due to their one-of-a-kind operation, piezoelectric motors are optimal for applications that require precise positional control since they are able to produce motion that is both very precise and controllable at a smaller scale.
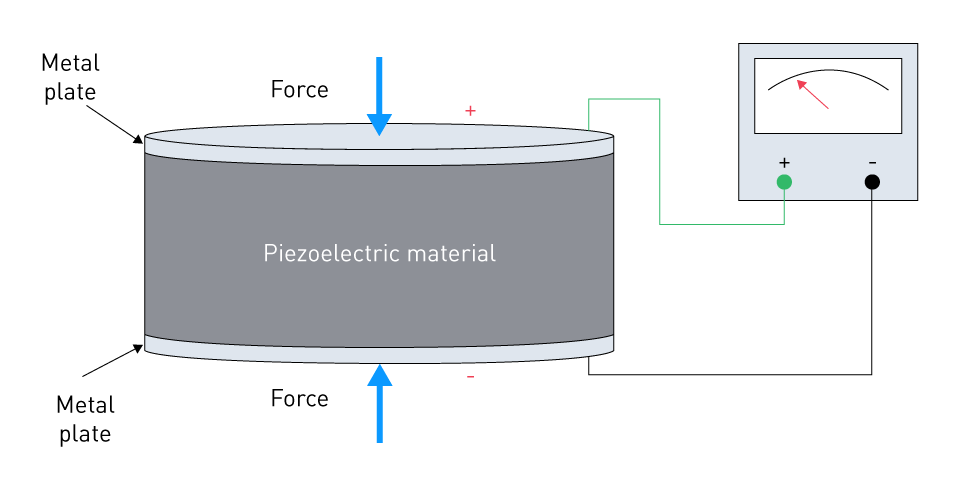
Figure 1: Principle of The Piezoelectric Effect
Composition and Design of Piezoelectric Elements
Materials such as quartz, Rochelle salt, and synthetic crystals such as lead zirconate titanate (PZT) are used to manufacture piezoelectric elements, which are the fundamental components of piezoelectric motors. These materials exhibit high piezoelectric effects. These elements, when exposed to an electric voltage, undergo controlled deformation, enabling them to convert electrical energy directly into mechanical energy. Depending on their intended purpose and the desired motion (either linear or rotational), designers can design piezoelectric elements in a variety of ways. Typically, manufacturers manufacture these elements in thin layers or stacks to maximize their deformation and, consequently, the force or displacement they can produce. To accomplish the intended performance, which includes speed, force, and positional precision, the precise engineering of these elements entails optimizing their geometry, material composition, and electrical properties. This makes it possible to achieve the desired performance.
The application of voltage causes the piezoelectric element's dimensions to change. This change might be linear or angular, depending on the orientation of the element and the pattern of the electrical input. A mechanical interface harnesses this change to generate motion in the motor's output shaft or stage. Controlling the voltage quickly and accurately enables one to control the motor's motion with the same level of precision, including its speed, direction, and position.
Piezoelectric motors stand out for their ability to maintain their position even in the absence of power, only using energy when necessary for movement. Because of this characteristic, in addition to the inherent precision of the piezoelectric effect, these motors are exceptionally efficient and are well-suited for activities in which precise and regulated motion is of the utmost importance. There are a number of key parameters that impact the performance characteristics of piezoelectric motors. These factors include the design and composition of piezoelectric elements, which in turn influence the efficiency, reliability, and application scope of piezoelectric motors in a variety of disciplines.
Types and Mechanisms
Various Designs of Piezoelectric Motors
Piezoelectric motors are available in a variety of designs, each of which is suited to specific applications and the requirements of various operations. Included among the most prevalent varieties are:
Ultrasonic Motors: Inducing ultrasonic vibrations in the piezoelectric element is the method by which ultrasonic motors function. These vibrations cause a rotor or slider to move as a result of frictional forces caused by the element. Ultrasonic motors are well-known for their high speed and compact size, which makes them excellent for applications that require quick motion yet have limited space available.
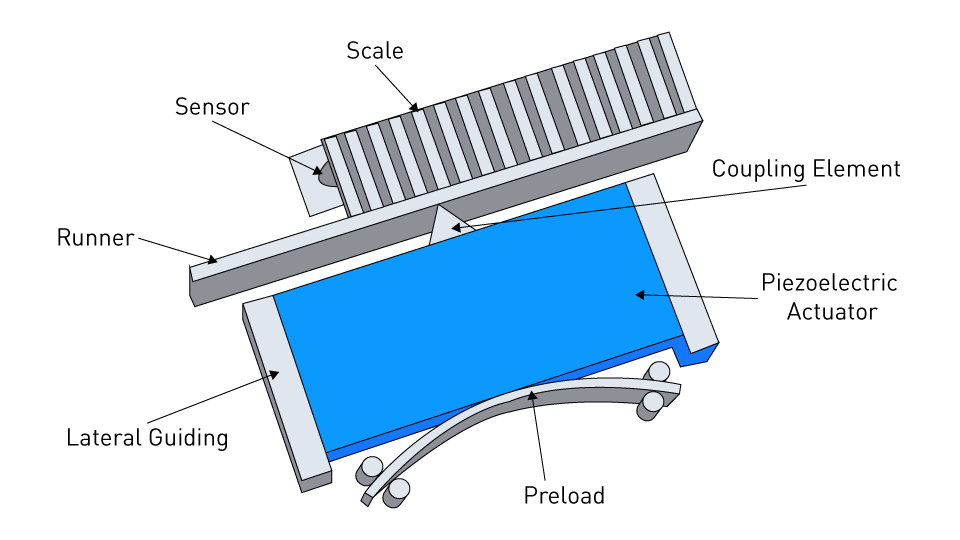
Figure 2: Ultrasonic Piezomotor from PILine
Stepping Motors: Piezoelectric stepping motors are able to generate motion by means of a sequence of discrete steps. The piezoelectric element expands and contracts in order to "walk" along a surface. The architecture of this device enables precise control of motion, the capacity to maintain positions without the need for power, and the ability to function effectively in applications that are downsized.
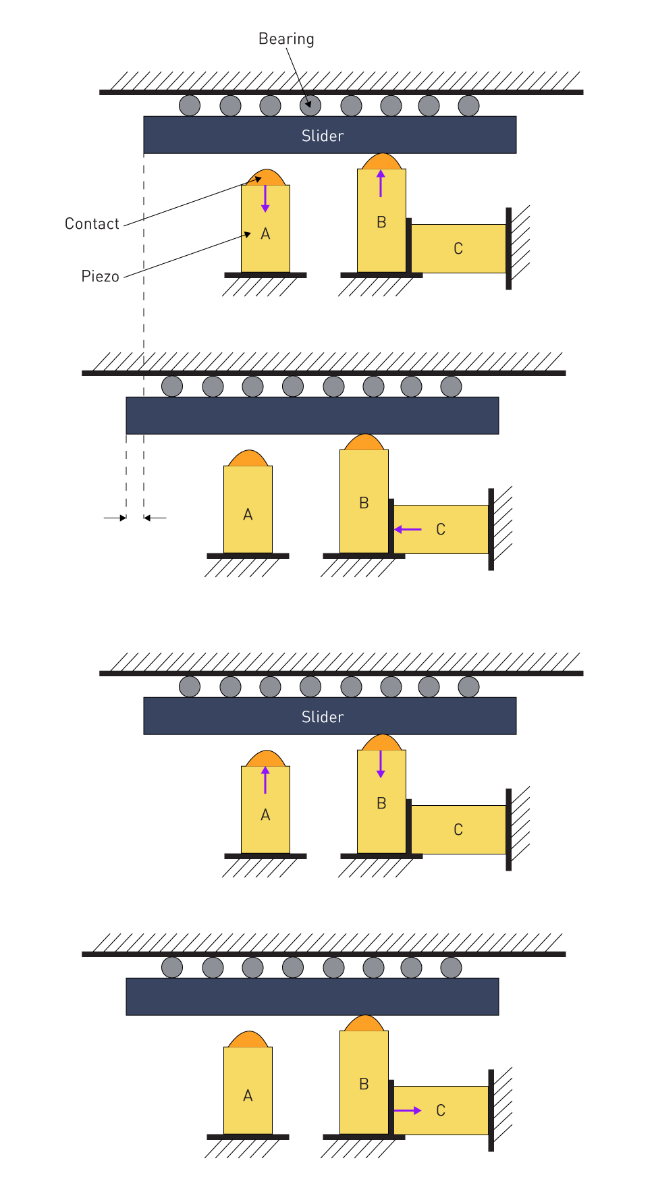
Figure 3: Working Principle of a Stepping Piezo Motor
Inchworm Motors: The term "inchworm motors" refers to motors that combine linear and clamping piezoelectric elements in order to generate controlled linear motion. These motors were given their name because of their resemblance to the movement of an inchworm. When it comes to applications that require precise, incremental movements over small distances, inchworm motors perform exceptionally well.
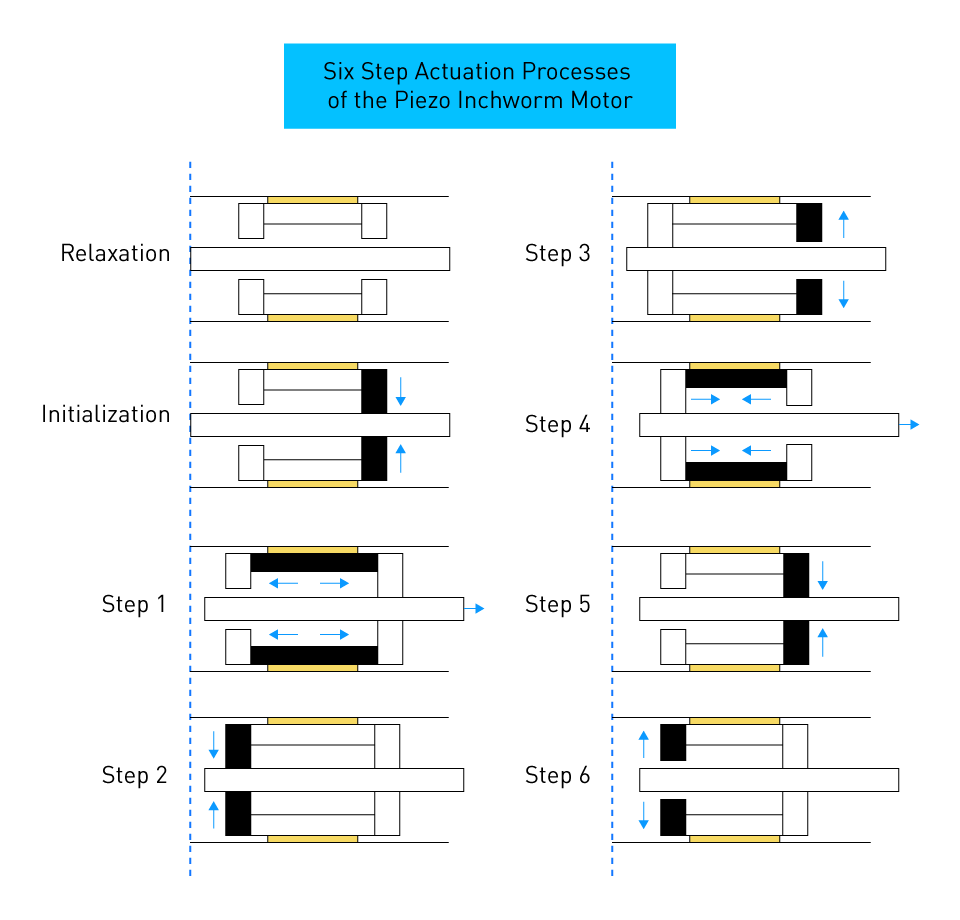
Figure 4: Six Step Actuation Process of The Piezo Inchworm Motor
Mechanisms of Motion Generation in Piezoelectric Motors
The fundamental process that forms motion in piezoelectric motors is the piezoelectric effect, but the ways in which different motor designs generate motion vary significantly.
Ultrasonic Motors: These motors allow the piezoelectric element to be excited at ultrasonic frequencies, which results in the creation of vibrations that cause a continuous rotation or linear motion through frictional contact with the moving section of the motor. The frequency and phase of the vibration can be altered to regulate the speed of the movement as well as the direction it is moving in.
Stepping Motors: Motion is generated in stepping motors by sequentially activating different sections of the piezoelectric element or array, which causes it to expand and contract in a controlled manner. Stepping motors are also known as stepper motors. This consecutive activation "steps" the motor along its path, which enables accurate placement to be achieved.
Inchworm Motors: These motors generate motion by alternatingly expanding and retracting piezoelectric elements, which are paired with clamping devices that grip a track or rod. Inchworm motors are sometimes referred to as "worm motors." In order to simulate the crawling motion of an inchworm, the extend-retract-grip sequence is used to produce a motion that is smooth and continuous.
Through the utilization of the one-of-a-kind characteristics of piezoelectric materials, every variety of piezoelectric motor is able to directly transform electrical energy into mechanical motion. This is accomplished without the use of electromagnetic fields or conventional motor components. Because of this direct conversion, it is possible to create motors that are extremely precise, efficient, and small, capable of providing both linear and rotational motion.
Applications of Piezoelectric Motors
Applications
Piezoelectric motors, known for their precise control and tiny size, have found applications in a number of cutting-edge fields that have had a significant impact on the capabilities and efficiency of a variety of technologies.
Semiconductor Manufacturing: In the semiconductor industry, piezoelectric motors are useful for wafer positioning and scanning in lithography procedures due to their high precision and clean operation. This makes them an ideal choice for semiconductor manufacturing. It is essential for them to be able to offer precise and regulated movements without producing electromagnetic interference or particulates in the cleanroom settings that are encountered in semiconductor fabrication facilities.
Optics and Photonics: In the fields of optics and photonics, piezoelectric motors are extensively utilized in the process of adjusting optical components for the purpose of fine-centered placement and focusing. Their outstanding precision is essential in a wide variety of applications, including the alignment of fiber optics and the positioning of lenses and mirrors in optical instruments. This ensures that the light path is aligned efficiently and that focusing accuracy is maintained.
Medical and Biotechnology: The precise and regulated movements of piezoelectric motors are beneficial to the medical industry. These motors are used in applications such as medical imaging equipment, where they are used to modify and position sensors and imaging components. In biotechnology, piezoelectric actuators assist in the manipulation of small biological samples, contributing to breakthroughs in research and diagnostics.
Specific Applications in Micro-Positioning and Delicate Operations
Specifically, the ability of piezoelectric motors to perform motions with nanoscale precision has led to their adoption in specialized applications that need micro-positioning and the handling of fragile materials or components. This is because of the specific properties of piezoelectric motors.
Micro-Manufacturing: In manufacturing processes that involve small components, piezoelectric motors enable the assembly and manipulation of parts with high accuracy. This satisfies the requirements of miniaturization in the electronics industry as well as in other industries.
Robotics: Piezoelectric motors offer the needed precision and smooth control in the field of robotics, particularly in micro-robotics and robots designed for sensitive jobs. This enables the manipulation of objects at a very microscopic scale, which is a significant advancement in the field of robotics.
Aerospace and Defense: The aerospace and defense sectors utilize piezoelectric motors for the precise positioning of sensors and actuators in space-constrained areas, where their tiny size and dependability under various conditions are important.
Prospects and Challenges
Innovations and Potential Improvements
Opportunities for innovation are abundant in the field of piezoelectric motors, which is being pushed by ongoing research and development initiatives that are aimed at boosting the capabilities of these motors and broadening the range of applications for which they may be used. Recent developments have been made with the goal of enhancing the efficiency, force output, and precision of these motors, as well as reducing their size and the expenses associated with their manufacturers. Innovations in materials science, such as the creation of novel piezoelectric materials with higher energy densities, have the potential to make motors that are both more compact and more powerful. In addition, developments in control algorithms and drive electronics are making it possible to control motors with greater precision and responsiveness, which is further expanding the range of uses for piezoelectric motors. The integration of piezoelectric motors with smart technologies and the internet of things is another potential topic. This connection creates the possibility of real-time monitoring and control, which can considerably improve the functionality of piezoelectric motors in complex systems.
Technical and Practical Challenges in Wider Adoption
The widespread adoption of piezoelectric motors faces a number of technical and practical hurdles, despite the fact that they offer a number of advantages that are unique to them. The cost of the materials and manufacturing techniques that are necessary for piezoelectric elements can be more than the cost of typical electromagnetic motors, which is one of the key obstacles that must be overcome. When dealing with applications that are either large-scale or cost-sensitive, this cost issue is frequently a crucial consideration. The restricted range of motion that is supplied by individual piezoelectric motors is another difficulty. In order to attain the requisite range, it may be necessary to use sophisticated mechanisms or arrays of motors, which will add to the complexity and cost of the system. Thermal management is another issue that continues to be a problem. This is because the efficiency of piezoelectric motors can result in the accumulation of heat during high-load or continuous operations, which necessitates the development of creative cooling solutions for small spaces. Furthermore, the requirement for specific drive electronics and control systems in order to fully realize the potential of piezoelectric motors might present integration issues. This is especially true when retrofitting existing systems or when applications have a restricted amount of space.
直接登录
创建新帐号