Hall-Effect Sensors
Since Hall-effect sensors are sensitive to magnetic fields, they have a special place in the world of magnetic sensors and can be used for a wide range of purposes.
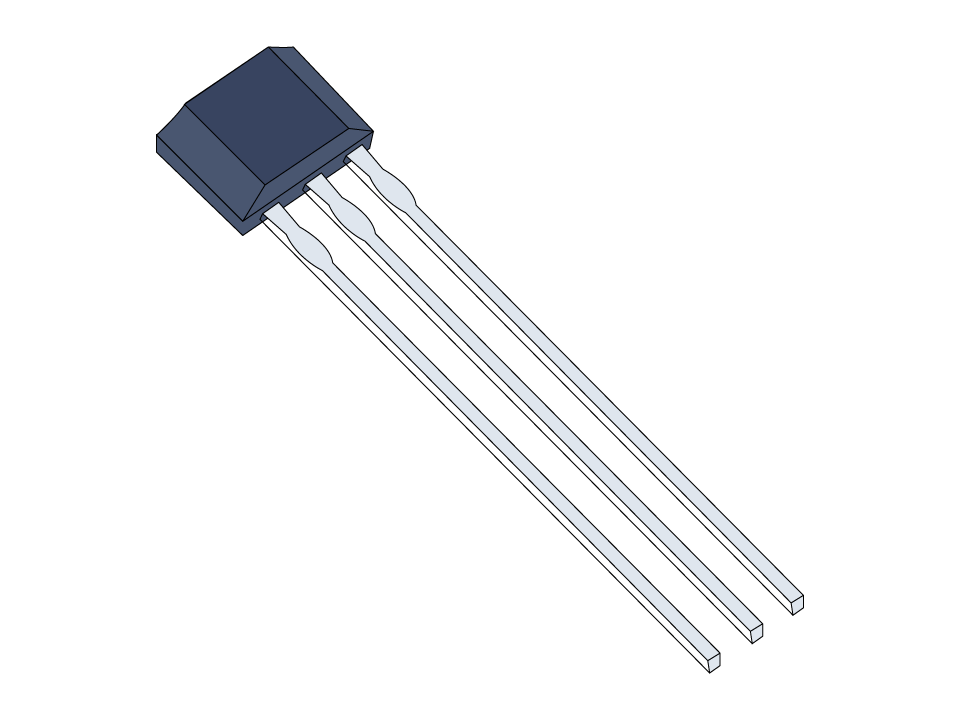
Figure 1: Hall-Effect Sensor
Working Principle
Edwin Hall established the Hall-effect concept in 1879, which serves as the foundation for Hall-effect Sensors. A voltage across a current-carrying conductor positioned perpendicular to a magnetic field is produced, which is perpendicular to both the magnetic field and the current flow. We call this phenomenon- the Hall effect.
A thin conductive substance is exposed to a current flow in a Hall Effect sensor. This material generates an induced Hall voltage when it comes into contact with a magnetic field that is perpendicular to the current flow. The product of the magnetic field strength and the current is directly proportional to the Hall voltage. By converting the Hall voltage into an equivalent electrical output, the sensor is able to determine the existence and strength of the magnetic field. In order to infer details about the magnetic field or its source, this output can then be monitored, conditioned, and examined.
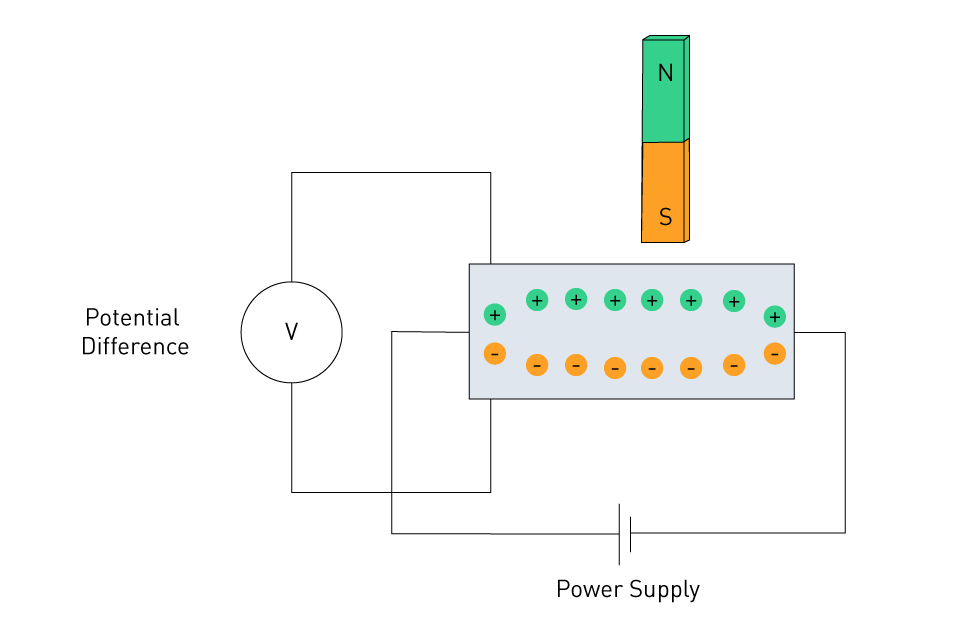
Figure 2: Working of a Hall-Effect Sensor
An important consideration for Hall sensors is the angle of approach, the angle at which the current carrying conductor or trace and its associate magnetic field interact with the sensor. Each sensor has an acceptable range for angle of approach. The sensor will not give an accurate measurement if the angle of approach is outside this acceptable range.
Applications
Position Sensing: By sensing the magnetic field surrounding an object, Hall-effect sensors play a crucial role in determining its location. This is especially important for automotive systems since these sensors let you know where the throttle and crankshaft are, among other parts, and allow you to precisely manage how the car runs.
Speed Detection: Particularly in applications such as anti-lock braking systems (ABS), these sensors are widely utilized for speed detection. Accurate speed readings are vital for systems that need precise speed control and monitoring, and they can be obtained by sensing the magnetic fields generated by spinning gears or other magnetic encoders.
Hall-effect sensors are widely used in many different sectors, including position sensing, speed detection, fluid level measurement, and current sensing. This highlights the sensors' versatility and significance.
With their distinct mode of operation, Hall-effect sensors have made major contributions to the fields of sensing and measurement as well as to the development of numerous applications across sectors, hence boosting technological developments.
Magneto-Resistive Sensors
The mechanism of operation of magneto-resistive sensors relies on the magneto-resistive effect, specifically the Anisotropic Magneto-resistive (AMR) effect. For the detection of magnetic fields and comprehension of their consequences in a variety of applications, ranging from industrial sensing to navigation, these sensors are crucial.
Anisotropic Magneto-Resistive (AMR) Effect
The phenomenon where a ferromagnetic material's electrical resistance shifts in response to an external magnetic field supplied in a favored direction is known as the anisotropic magneto-resistive effect. Because of the intrinsic anisotropy of the AMR effect, the resistance change is contingent upon the angle formed by the direction of the magnetic field in the material and the current flow. AMR sensors are very flexible and efficient in detecting magnetic fields because of this feature, which allows the sensor to identify not only the magnetic field's presence and strength but also its direction.
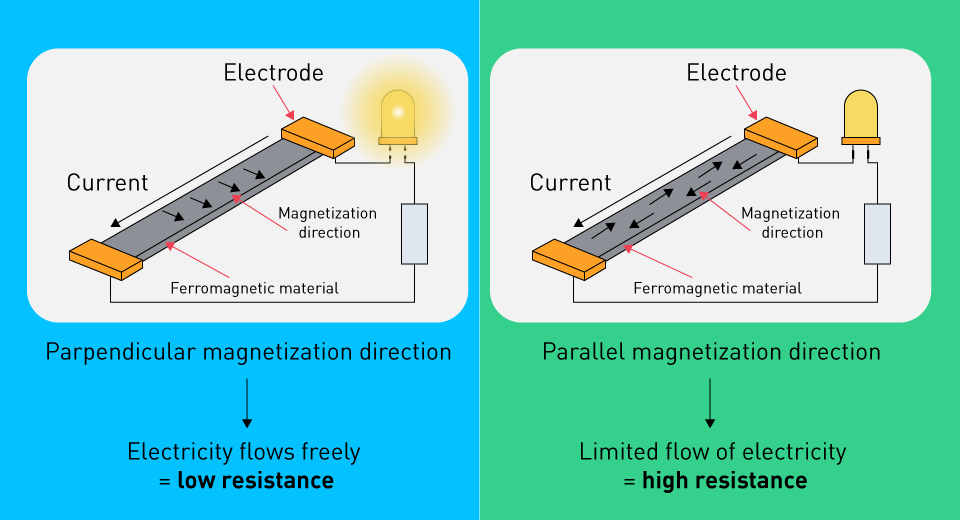
Figure 3: Working of an AMR Sensor
The ferromagnetic material's resistive properties are changed when an external magnetic field is applied because it realigns the magnetic domains within the material. Following measurement, the induced resistance change is transformed into an electrical signal proportional to the strength of the magnetic field. This signal can then be processed and interpreted for a variety of uses.
Applications
Magnetic Field Mapping: The creation of magnetic field maps relies heavily on magneto-resistive sensors, which offer vital information about the characteristics and distribution of the magnetic field in a particular space or system. Understanding magnetic surroundings is essential for scientific study, geophysical studies, and industrial applications.
Electronic Compasses: Electronic compasses used in navigation systems are one of the most common uses for AMR sensors. AMR sensors are able to precisely identify a device's orientation with respect to magnetic north by detecting the Earth's magnetic field. This capability makes them useful for navigation and positioning in a variety of devices, including cars, smartphones, and marine instruments.
In addition to this, magneto-resistive sensors are used in consumer electronics for magnetic switch functions, automotive systems for wheel speed and crankshaft position sensing, and industrial automation for proximity and position sensing.
In conclusion, magneto-resistive sensors have become essential in current technology, enhancing the capabilities of diverse systems across numerous domains, thanks to their sensitivity to the direction and magnitude of magnetic fields through the AMR effect.
Current Sensors
Electric current (amperes) flowing through a wire is measured by current sensors, which are essential components of electrical systems. They have a big impact on a lot of different applications, like overload protection, feedback control, and power monitoring. The types, uses, and working principles of modern sensors are covered in detail in this section.
There are several scenarios for a current sensor’s behavior to a high-current glitch (beyond current limit setting). Many sensors have a maximum current or magnetic field strength they can accurately measure. When the primary current surpasses this limit, the sensor saturates: the sensor outputs a constant value even if the primary current continues to increase. In some cases, rather than saturating, the sensor output may clip at its maximum or minimum value. This means that the sensor's output signal is limited to a specific range, and any input beyond this range is truncated or clipped. If the primary current exceeds the sensor's maximum rating or operating limits, it can also damage the sensor.
Current sensors, like any other component with a physical contact to a power source or path, produce heat. Depending on the sensor design and specifications, designers must take appropriate measures for current sensing thermal management.
Principles of Operation
Magnetic Field Sensing: A magnetic field is produced in proportion to the amount of electric current flowing through a conductor. This field is detected by current sensors that sense magnetic fields in order to measure the accompanying current. Hall-effect and magnetic core-based sensors are mostly based on this idea.
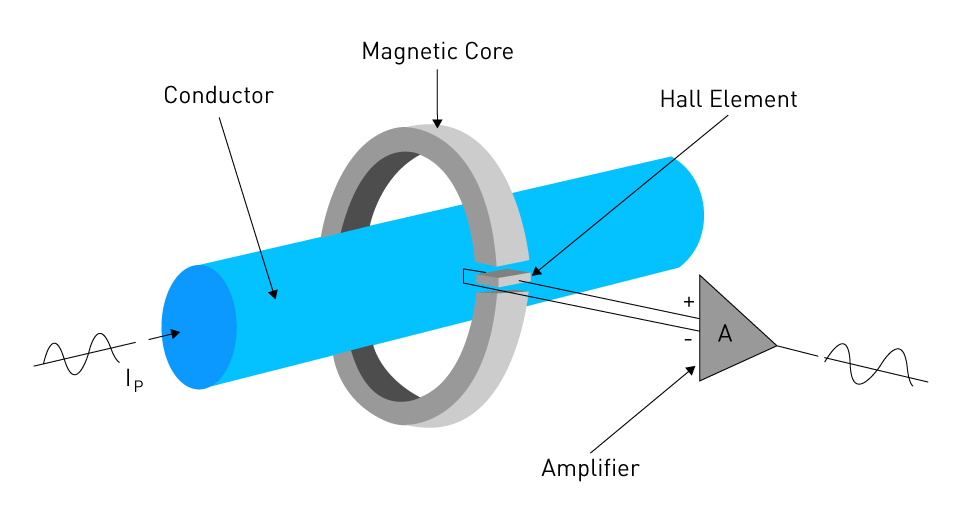
Figure 4: How a Magnetic Current Sensor Works
Shunt Resistors: The voltage drop concept governs how shunt resistors work. The circuit is connected in series with a precisely known resistor, and the voltage drop across the resistor is measured. The voltage is directly proportional to the circuit's current flow.
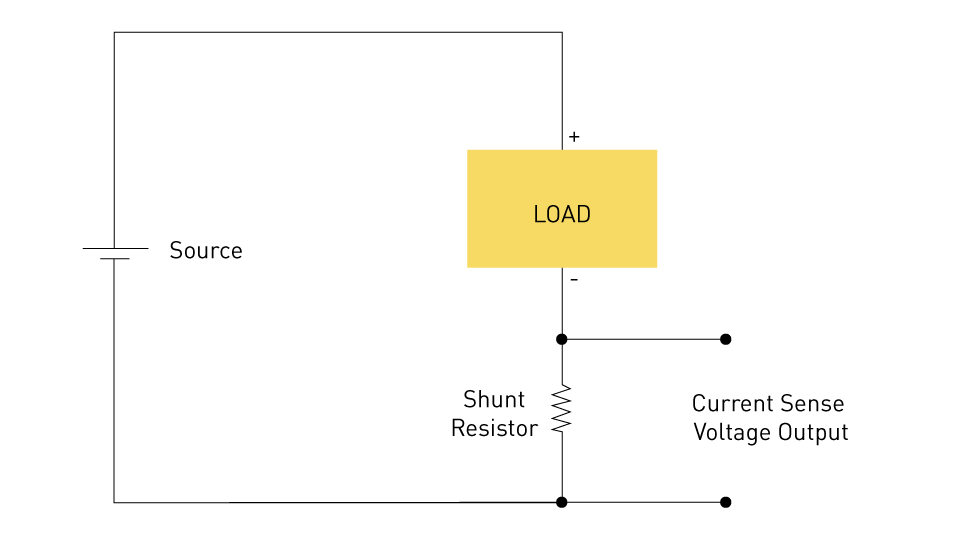
Figure 5: How a Shunt Resistor Works
Transformer Principle: In order to measure the primary current, current sensors also work on the transformer concept, in which the magnetic field created by the primary current causes a secondary current to be induced in a coil coiled around the conductor.
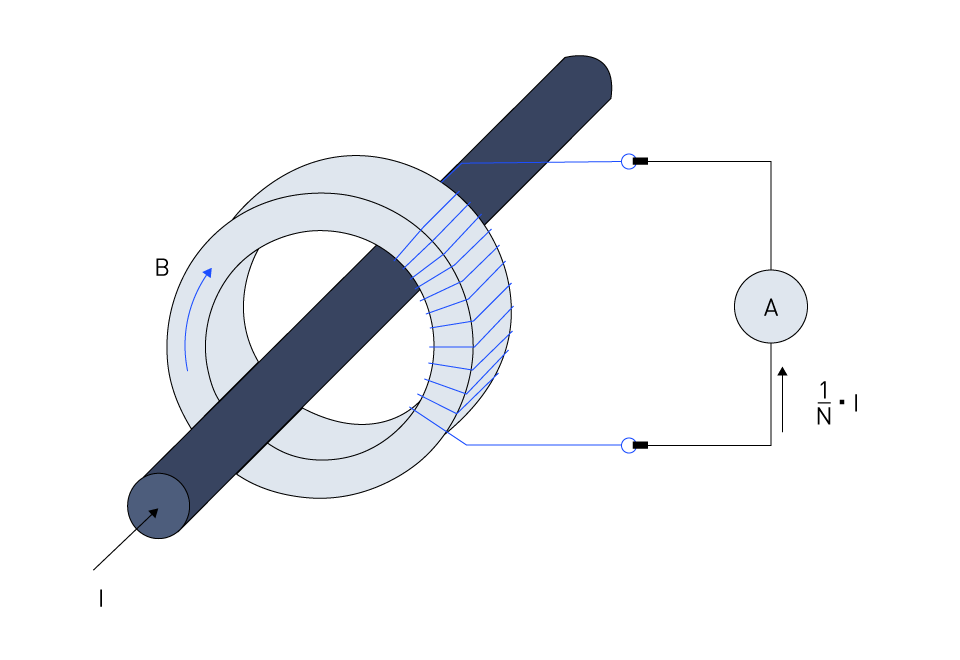
Figure 6: How a Current Transformer Works
Types of Current Sensors
Closed-Loop vs Open-Loop Sensors: Closed-loop sensors are reliable and accurate because they are isolated from the measured circuit and deliver feedback to control the output. Open-loop sensors are less precise since they are directly connected to the measured circuit without any feedback, despite being simpler and less expensive.
Hall-Effect Sensors: The Hall-effect principle, which states that in the presence of a magnetic field, a voltage is induced perpendicular to the current flow, is used by these sensors. As they can offer electrical isolation and detect both DC and AC currents, they are widely employed.
Rogowski Coil: Air-core coils known as Rogowski coils are wrapped around a conductor and work using the magnetic induction principle. They are useful for measuring AC currents and quick transient currents because the induced voltage in the coil is proportional to the rate of change of current in the conductor.
Applications of Current Sensors
Power Monitoring: Power monitoring systems in homes and businesses depend heavily on current sensors to provide effective energy management and lower energy expenses.
Overload Protection: They are essential for preventing potential damage and risks by detecting and terminating excessive current flows, which protects circuits and devices from overcurrent circumstances. For example, protection circuits with current sensors protect the output stages of class D audio amplifiers from excessive current flow.
Thermal Management: By accurately measuring current flow through components and circuits, current sensing provides valuable insights into power consumption and heat generation within systems. This real-time data allows for effective implementation of proactive thermal management strategies, such as dynamic thermal balancing and adaptive cooling.
Inverter Phasing Sensing: Grid-tied solar inverters use current sensors to determine the phase angle of the input AC voltage, which is essential for synchronizing the inverter's output voltage with the utility grid or another AC power source.
Protection: Transformerless solar inverters use AC/DC-sensitive differential current sensors to detect leakage current and protect equipment and personnel.
Feedback Controls: By altering the output based on the measured current, current sensors provide vital feedback for control systems in power supplies, motor drives and various electrical/electronic circuits, assuring steady and effective performance. For example, current sensors are used to monitor and control current consumption of automotive PTC seat heaters with a current measurement feedback loop. Additional examples include high -side current sensing in Power Factor Correction (PFC) control circuits and low -side current sensing in LLC converter control circuits for effective closed-loop control.
Its usefulness improves performance, safety, and dependability in automobile electronics, battery management systems, and renewable energy systems.
Accurate and dependable current measurement and control are necessary for a wide range of applications. Current sensors, with their various forms and operating principles, are essential components of electrical and electronic systems.
直接登录
创建新帐号