Photodiodes
One essential element in the range of optical sensors are photodiodes, which function as transducers to transform light into electrical current. Their great sensitivity and quick response are well known, and these are crucial characteristics that help with applications like Light Detection and Ranging (LIDAR).
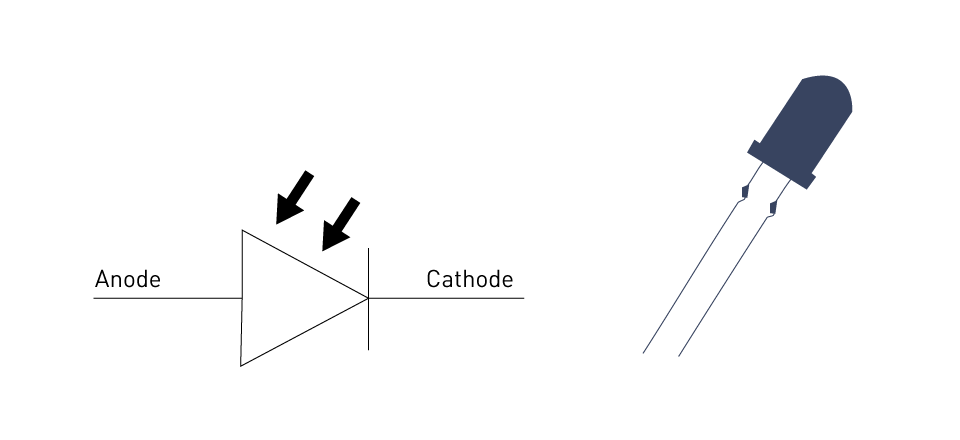
Figure 1: A Photodiode
Working Principle
The basis of photodiodes' operation is photon absorption, which creates electron-hole pairs in semiconductor materials. When photons, which are the building blocks of light, hit the photodiode, they provide electrons enough energy to break free from their atomic orbits and produce matching holes. Quantification of light levels is made possible by the passage of these electron-hole pairs, which form an electric current that is directly proportional to the intensity of the incident light.
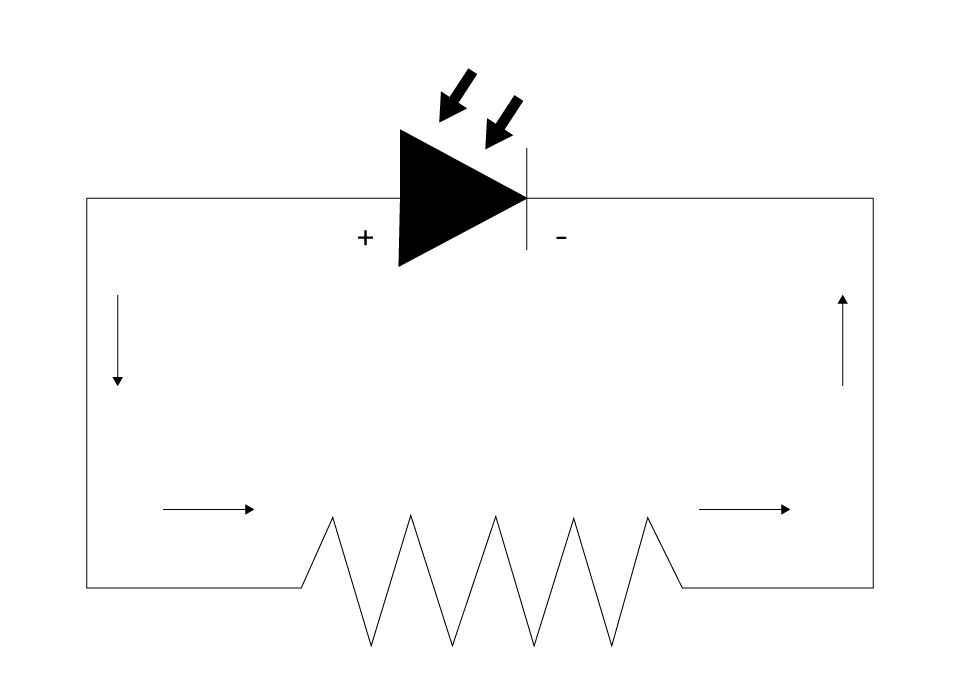
Figure 2: Working of a Photodiode
Types of Photodiodes
PN Photodiodes: Due to the modest sensitivity and speed, PN photodiodes—which are formed by the junction of p-type and n-type semiconductors—are usually used in low-light situations.
PIN Photodiodes: High-frequency applications can benefit from these photodiodes because they have an inherent semiconductor layer positioned between the p-type and n-type layers, which lowers capacitance and speeds up response.
Avalanche Photodiodes: Avalanche photodiodes are more sensitive because they produce an avalanche multiplication effect when they operate at high reverse bias voltages. This effect increases the produced current, which is crucial in high-precision applications since it enables the detection of incredibly low light levels because of the bigger gain.
Light Detection and Ranging (LIDAR) Applications
In LIDAR technology, which uses light pulses to detect distances, photodiodes are essential components. By measuring the reflected light pulses from objects, photodiodes in LIDAR systems are able to determine their distance using the speed of light and the interval between the transmitted and received pulses. For precise distance measurements, LIDAR is essential in many applications, including atmospheric research, autonomous vehicles, and topographical mapping.
Optical sensing applications rely heavily on photodiodes because of their remarkable capacity to convert light into quantifiable electric current. Photodiodes' accuracy and versatility highlight their significance in modern optical technology, whether they are used for measuring ambient light levels or advanced distance measurement systems such as LIDAR.
Phototransistors
In optical sensing technology, phototransistors are essential components that perform as both photodiodes and bipolar junction transistors (BJTs). Signal processing and communication are just two of the advanced applications that phototransistors can be used for. They stand out for their increased sensitivity and magnified reaction to light.
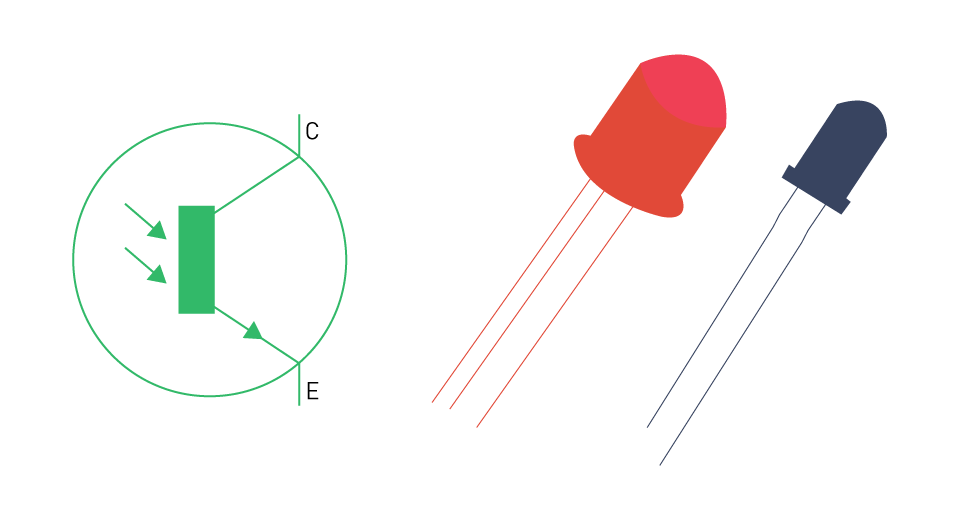
Figure 3: A Phototransistor
Amplified Response Compared to Photodiodes
While phototransistors and photodiodes function according to comparable principles, their reactions to incident light differ considerably. Whereas phototransistors amplify this current to provide a greater output signal, photodiodes directly convert light into current. Compared to conventional photodiodes, this amplification is made possible by the intrinsic gain of the transistor, which allows for the detection of lower light levels. Because of their built-in amplification, phototransistors can operate efficiently in low-light situations, which increases their dependability and expands their potential applications.
Configurations
Common Base Configuration: The base terminal in this configuration acts as a common terminal for the input and output. Base current is induced by light incident on the base-collector junction, and this in turn modifies the collector current. This setup has a broad bandwidth by design and is appropriate for high-frequency applications because of its low input impedance and high output impedance.
Common Emitter Configuration: The most widely used arrangement for phototransistors is the common emitter configuration, which stands out for having a high gain. The base current is modulated by the incident light and amplified to provide the collector current. With its high output impedance and moderate input impedance, this design is perfect for high power gain applications.
Common Collector Configuration: The strong current gain of the common collector setup sets it apart from other configurations without a noticeable voltage gain. The base current is modulated by the incident light and amplified to provide the collector current. Due to the low output impedance and high input impedance, this design is perfect for applications that need a lot of signal processing and amplification.
Applications and Importance
Phototransistors have several applications because of their higher sensitivity and amplified response as compared to photodiodes. They play a crucial role in systems where light detection and amplification are necessary, like optical communication systems, remote controls, and other light detection applications. They are also necessary for detecting low light levels.
To sum up, phototransistors are essential to the development of optical sensors since they can respond with greater amplitude and function in many configurations. They are essential in a wide range of applications where accurate light detection and amplification are critical due to their versatility and increased sensitivity.
Fiber Optic Sensors
Fiber optic sensors are the pinnacle of adaptable, cutting-edge sensing devices that use the characteristics of light to measure a variety of parameters like strain, pressure, and temperature. These sensors are ideal in many difficult applications because of their high sensitivity, small design, and resilience to electromagnetic interference when combined with optical fibers.
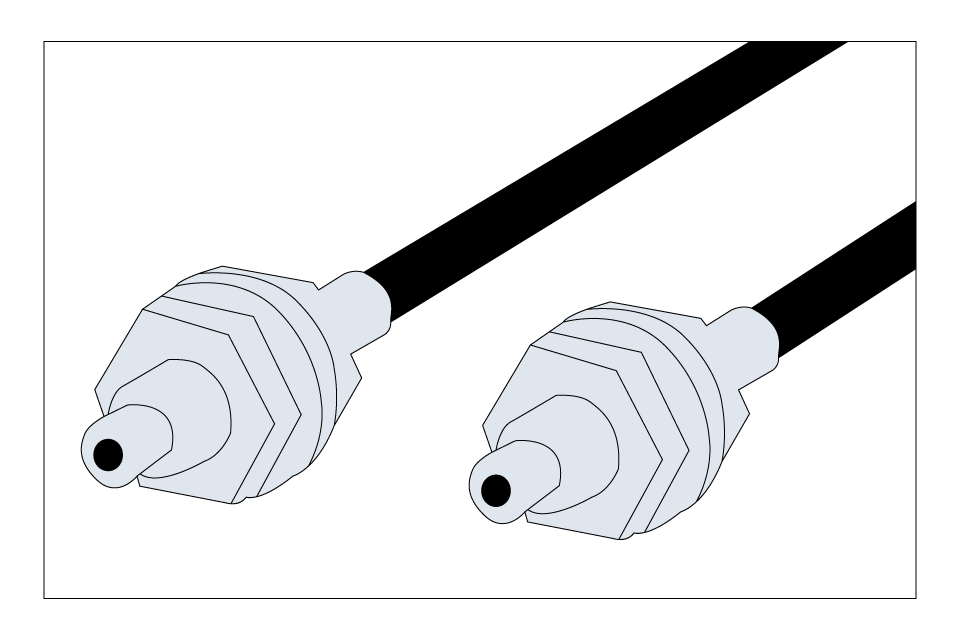
Figure 4: Fiber Optic Sensors
Types of Fiber Optic Sensors
Intensity Modulated Fiber Optic Sensors: Based on the modulation of light intensity in the optical fiber, these sensors operate. The light is detected by a photodetector once its intensity is changed by variations in the surrounding parameters. Variations in the reflecting qualities of surfaces interacting with the fiber or light loss resulting from bending, microbending, or macrobending of the fiber may be the cause of this modulation.
Phase Modulated Fiber Optic Sensors: Phase modulated fiber optic sensors function differently from intensity modulated ones in that they identify variations in the phase of light waves as they pass through the fiber. They are highly accurate and sensitive, and are particularly helpful in identifying even the smallest changes. The refractive index of the fiber is impacted by changes in temperature, pressure, or strain, which alters the phase of the light that is propagated.
Applications
Temperature Sensing: For applications where accurate temperature readings are necessary, fiber optic sensors are essential. They are perfect for usage in high electromagnetic field situations, including power plants or MRI machines, where traditional electronic sensors fail due to their resilience to electromagnetic interference.
Pressure Sensing: Fiber optic sensors are invaluable in a wide range of industrial and biomedical applications due to their exceptional ability to detect minute pressure differences. They are extensively employed in intracranial pressure monitoring in medical contexts as well as hydraulic systems to monitor fluid pressure.
Strain Sensing: Since fiber optic sensors can identify even the smallest structural deformations, they are essential for tracking the structural health of buildings, bridges, and airplanes. This allows for the early detection of probable breakdowns.
With its wide variety of applications and varied modulation principles, fiber optic sensors are essential parts of contemporary sensing technology. Because of their exceptional sensitivity, precision, and immunity to electromagnetic interference, they are widely used in a wide range of applications, such as industrial, medical, and structural ones, confirming their status as complex, multipurpose sensing components.
Angular Position Sensors (Optical Encoder Type)
Determining exact rotational positions of objects requires the use of angular position sensors equipped with optical encoder types. They greatly advance the domains of robotics, industrial automation, and motor control by using the transduction of light signals to decode the angular location, speed, and direction of a shaft or axle to which they are coupled.
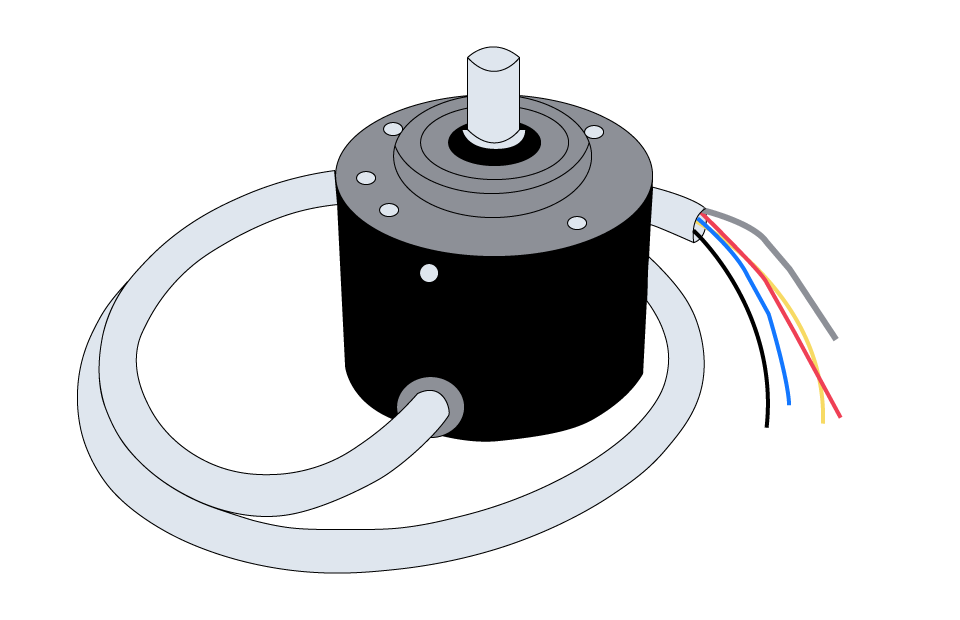
Figure 5: Optical Encoder
Principles of Operation: Optical Detection of Rotary Position
The basis of operation for optical encoders involves adjusting light intensity via an encoder wheel, which is a patterned disk attached to a spinning body. One side of the disc has a light source, often an LED, while the other side has a photodetector. The encoder wheel disrupts the light beam as the item spins, producing a sequence of light pulses that are subsequently picked up and translated into electrical signals. Accurate and real-time monitoring of the rotational parameters is made possible by the direct correlation between the number and frequency of the pulses and the angular position, speed, and direction of rotation.
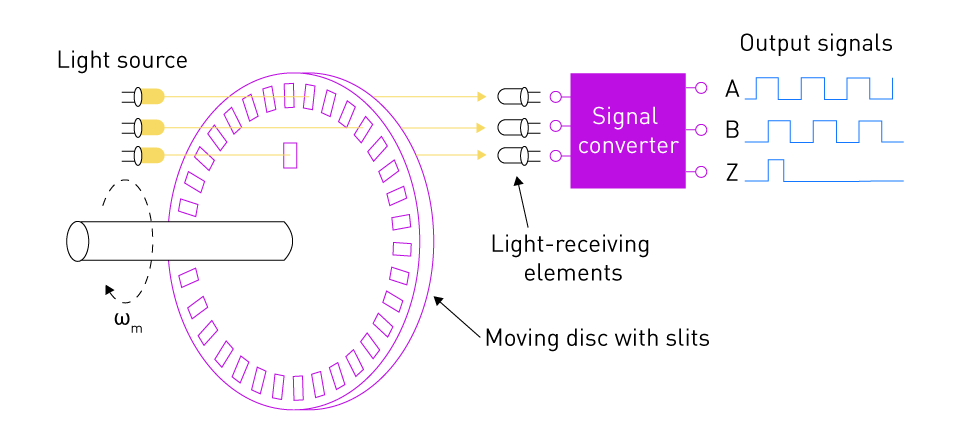
Figure 6: Working of an Optical Encoder
Incremental vs. Absolute Encoders
Incremental Encoders: Pulse streams corresponding to the object's incremental displacement are produced by incremental optical encoders. They need a reference point in order to calculate absolute position because they do not store positional information. Because of their simplicity and cheaper cost, incremental encoders are useful for measuring both speed and direction.
Absolute Encoders: As opposed to this, absolute optical encoders provide each rotational position a distinct output code, making it possible to determine the precise location without the use of a reference point as soon as the device is powered on. Although more expensive and complex than incremental encoders, this is essential in situations where knowing the precise location is critical, including robotics and industrial automation.
Applications
Optical encoders have extensive applicability in situations where mechanical systems need to be controlled, monitored, or both. Surgical robotics, servo and motion control, radiation therapy, diagnostic imaging, microfluidic dispensing, robotic arms, and many more are examples of these uses.
For accurate detection and measurement of rotating locations, speeds, and directions, optical encoder type angular position sensors are essential. Whether an application requires precise positional accuracy from absolute encoders or simplicity and cost-effectiveness from incremental encoders, it will choose which type of encoder to use. Either way, optical encoders are essential in many industrial and technological fields because of their capacity to deliver real-time, high-resolution feedback.
There is a resolution/bandwidth tradeoff in position sensors. Applications that need precise position control may prioritize higher resolution, while those requiring fast dynamic response may favor higher bandwidth.
直接登录
创建新帐号