Piezoresistive
Considering the high sensitivity and straightforward design, piezoresistive pressure sensors—which convert mechanical force into an electrical signal—are among the most widely used varieties of pressure sensors. The essential operating premise is that stress causes a material's resistance to change.
Stress-Induced Resistive Change
The basic idea underlying these sensors is the piezoresistive effect, in which pressure is applied to cause stress and subsequent deformation in a metal or semiconductor strain gauge, changing the resistivity of the material. The exact detection of pressure fluctuations is made possible by the quantification and conversion of this resistivity shift into an electrical signal proportional to the applied pressure.
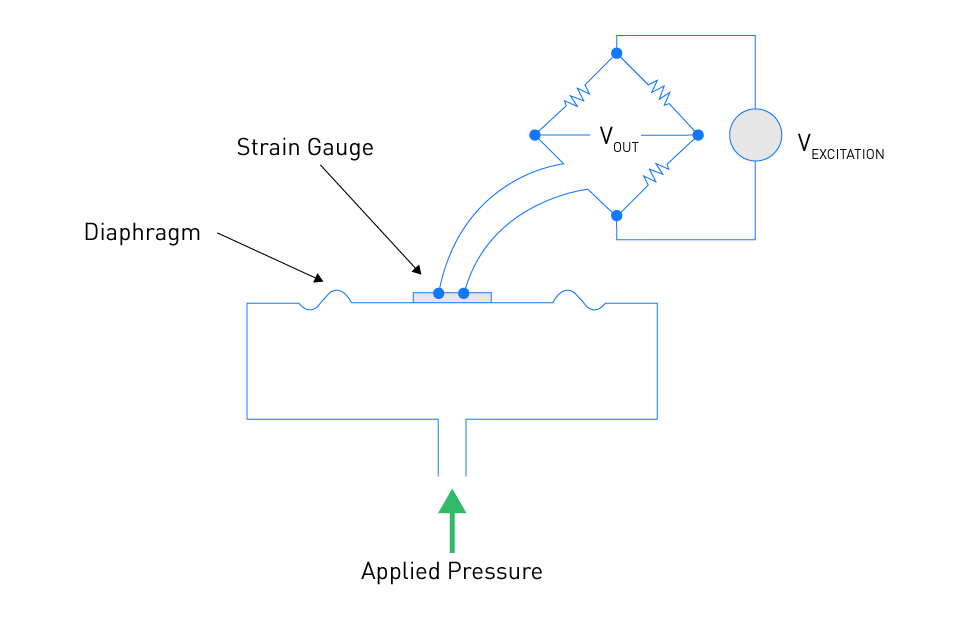
Figure 1: Working of a Piezoresistive pressure Transducer
MEMS Structures and Diaphragms
MEMS Structures: Miniaturized piezoresistive pressure sensors are made possible by Micro-Electro-Mechanical Systems (MEMS) technology, which also makes it possible to integrate these sensors with electronic systems. Because of its well-known high sensitivity, low power consumption, and compatibility with integrated circuit technology, MEMS piezoresistive sensors are widely used in a wide range of applications.
Diaphragms: Piezoresistive pressure sensors rely on the diaphragm, which serves as the pressure-sensing element. Pressure causes the diaphragm to distort, which stresses the piezoresistors that are placed on top of it. Precise pressure measurements are possible because the amount of deformation and the applied pressure are correlated and translate into a change in resistance.
Applications
Due to their capacity to produce precise and dependable pressure readings, piezoresistive pressure sensors are widely used in a variety of industrial applications for process control and monitoring, as well as in medical equipment for blood pressure and tire pressure monitoring.
A major breakthrough in the creation of small, effective, and adaptable pressure sensing devices is the combination of MEMS technology and piezoresistive principles.
Capacitive
The idea of capacitive sensing, which states that fluctuations in pressure translate into changes in capacitance, underlies the operation of capacitive pressure sensors. These kinds of sensors are well known for their capacity to monitor both static and dynamic pressures, as well as their sensitivity and long-term stability.
Variation of Capacitance with Pressure
The pressure to be measured in capacitive pressure sensors typically acts on a diaphragm, which is a component of a capacitor. The diaphragm changes shape in response to pressure, changing the spacing between the capacitor plates and, consequently, the capacitance. Following measurement, the resultant capacitance change is transformed into an output signal that is proportionate to the applied pressure.
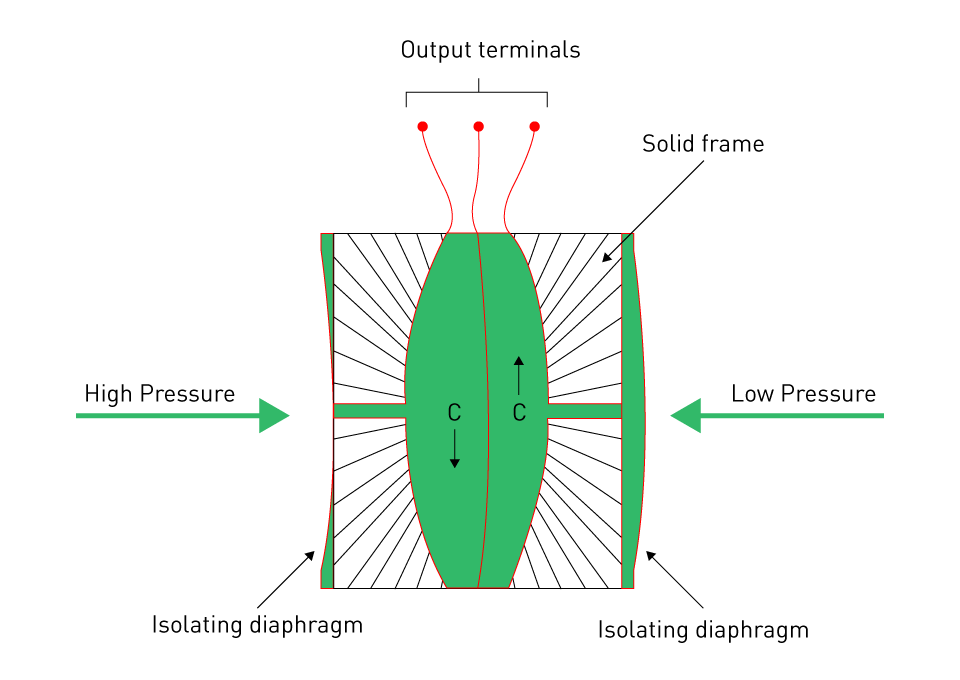
Figure 2: Working of a Capacitive Pressure Sensor
Mathematically, the capacitance (C) of a parallel plate capacitor is given by the equation:
$$ C=\frac{Ɛ_0\timesƐ_r\times A}{d}$$Where:
- C = Capacitance
- Ɛ0 = Permittivity of free space
- Ɛr = Relative permittivity of the dielectric material
- A = Area of the capacitor platesE
- d = Separation between the capacitor plates
As pressure induces deformation in the diaphragm, it modifies the separation (d), leading to a change in capacitance which is then quantified to determine the applied pressure.
Materials and Design Considerations
Materials: The sensitivity and stability of the sensor are affected by the materials used for the diaphragm and the dielectric, therefore selection is important. Stainless steel and silicon are common examples of materials with low hysteresis and high elastic modulus that are used for diaphragms. Typically, the dielectric material must be an insulator with a high dielectric constant; silicon dioxide and ceramic materials are popular options.
Design Considerations: Capacitive pressure sensors are defined by their overall configuration, kind of dielectric material, thickness and diameter, and other design variables that affect their performance, dependability, and applicability for certain applications. Apart from this, temperature compensation, linearity, and hysteresis must also be taken into account in order to provide reliable pressure readings under a range of environmental circumstances.
Applications
Capacitive pressure sensors are essential for a wide range of applications, such as medical equipment, industrial process control, and atmospheric pressure monitoring, due to their great sensitivity and stability.
Leveraging the full potential of capacitive sensing technologies, which accommodate a range of applications with different needs, requires careful material selection and critical design considerations.
Resonant
Sensitive sensors known as resonant pressure sensors use variations in a mechanical system's resonant frequency to detect pressure. These are known for having very high precision, and they are usually used in situations where having very high accuracy is a must.
Frequency Change due to Pressure Variation
Resonant pressure sensors rely on a mechanical resonator, often composed of silicon, which is engineered to possess an inherent resonant frequency that is responsive to variations in external pressure. The resonator's inherent frequency shifts as a result of changes in stress and strain caused by applied pressure. High accuracy measurement of this frequency shift, which is proportional to the applied pressure, is frequently possible through the use of piezoelectric or capacitive sensing methods.
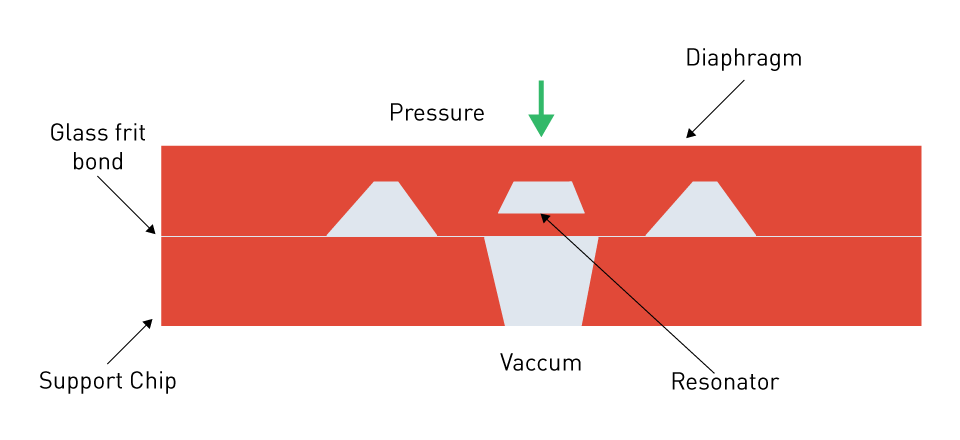
Figure 3: Working of a Resonant Pressure Sensor
Mathematically, the resonant frequency (f) can be modeled as:
$$f=\frac{1}{2\pi}\sqrt{\frac{k}{m}}$$Where:
- f = Resonant frequency
- k = Spring constant of the resonator
- m = Effective mass of the resonator
The connection shows that the applied pressure affects the mechanical characteristics of the resonator, which in turn affects the frequency, making accurate pressure measurements possible.
Applications in High-Accuracy Requirements
Precision Measurement: Resonant pressure sensors are essential to precision measurement applications like barometric pressure measurements, where even small errors can cause substantial differences in altitude readings. This is because of their unmatched stability and accuracy.
Aerospace and Aviation: In the aerospace and aviation industries, high-accuracy pressure sensors are essential for monitoring fuel systems, hydraulic systems, and cabin pressure, where even the tiniest mistake can have dire repercussions.
Industrial Processes: Resonant pressure sensors are used in industrial processes, particularly in the chemical and pharmaceutical sectors, to monitor and control operations where safety and product quality depend on maintaining particular pressure levels.
Research and Development: Since resonant pressure sensors have a high resolution and are highly reliable, they are also often utilized in research and development labs for studies and experiments that call for careful pressure monitoring and control.
In situations where accuracy is crucial, resonant pressure sensors are invaluable because of their exceptional precision and dependability. The sensors' capacity to identify even the slightest variation in pressure renders them appropriate for a variety of uses, ranging from industrial process management to aviation. By guaranteeing secure and ideal operating conditions, these sensors considerably promote progress in various domains.
直接登录
创建新帐号