Thermocouples
Engineering applications rely heavily on temperature measurements, and among the many temperature sensors available, thermocouples have drawn a lot of interest because of their adaptability, wide temperature range, and straightforward design.
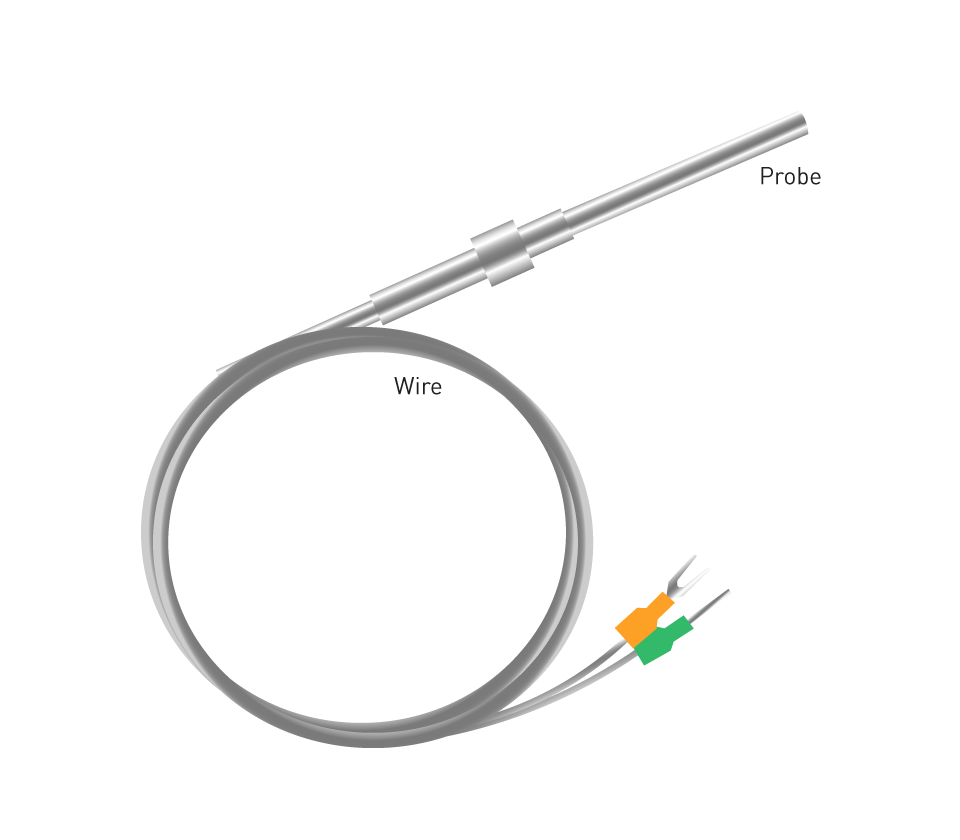
Figure 1: Thermocouple
Working Principle: Seebeck Effect
The Seebeck effect is the fundamental mechanism of a thermocouple. It is a term used to describe a phenomena that Thomas Seebeck discovered in the early 1800s, which is the generation of a voltage differential (also known as an electromotive force, or EMF) between two dissimilar metal conductors at different temperatures. A thermocouple is made up of two distinct metals, A and B, that are connected at one end. A voltage is generated when one of the junctions, referred to as the measuring junction, is at a temperature different from the reference junction. The temperature differential between the two junctions can be determined by measuring and correlating this voltage.

Figure 2: Seebeck Effect in Thermocouples
Types and Their Material Composition
A letter designation is used to distinguish between the many types of thermocouples. Every variety is composed of distinct materials and has distinct voltage versus temperature properties. Among the prevalent kinds are the following:
Type J (Iron-Constantan): It is utilized in environments that are inert, oxidizing, reducing, and vacuum. From -40°C to +760°C is its range.
Type K (Chromel-Alumel): Usually used in oxidizing atmospheres, the general-purpose thermocouple has a temperature range of -200°C to +1250°C.
Type T (Copper-Constantan): In cryogenics and other ultra-low temperature applications, this type finds frequent use since it remains stable within its range of -200°C to +350°C.
Advantages and Limitations
Advantages
- Wide Temperature Range: Certain thermocouples are useful in a variety of industries because they can measure extremely high or low temperatures.
- Fast Response: Their small size and direct contact allow them to sense and react to temperature changes swiftly.
- Simple and Cost-Effective: They are reasonably priced and offer an easy-to-use design.
Limitations
- Accuracy: Although they have a large temperature range, they may not be as accurate as other temperature sensors like RTDs.
- Stability: The accuracy of thermocouples may be impacted over time by drift, particularly at higher temperatures.
- Reference Required: Accurate measurement requires a reference temperature, which is typically the cold junction. There are instances when this calls for the inclusion of circuitry or compensating methods.
Applications
Thermocouples are used in a wide range of industries for a variety of purposes, such as HVAC system temperature management and industrial process monitoring in manufacturing and chemical production. Additionally essential to scientific research, vehicle exhaust systems, and environmental monitoring are thermocouples. They aid with energy generation optimization in power plants and set off warnings in safety systems when temperature abnormalities occur.
In conclusion, despite significant drawbacks, thermocouples are a common option in many industrial and laboratory settings due to their responsiveness, wide temperature range, and affordability.
RTDs
Precision temperature sensors known for their accuracy, stability, and repeatability are called resistance temperature detectors, or RTDs. RTDs work on the theory that changes in material resistance as a result of temperature fluctuations, in contrast to thermocouples, which are based on voltage generation.
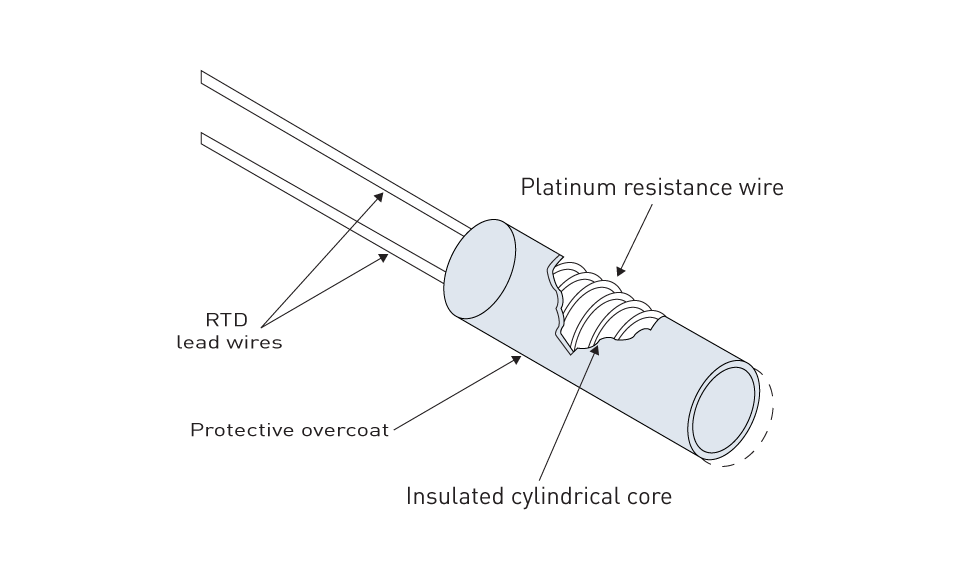
Figure 3: RTD
Working Principle: Resistive Change Due to Temperature
The main principle underlying the operation of an RTD is the distinctive resistance change that specific materials experience in response to temperature changes. In particular, throughout a broad temperature range, the resistance value of the RTD material grows in tandem with temperature increases, and this change is nearly linear. The temperature can be determined by measuring the resistance.
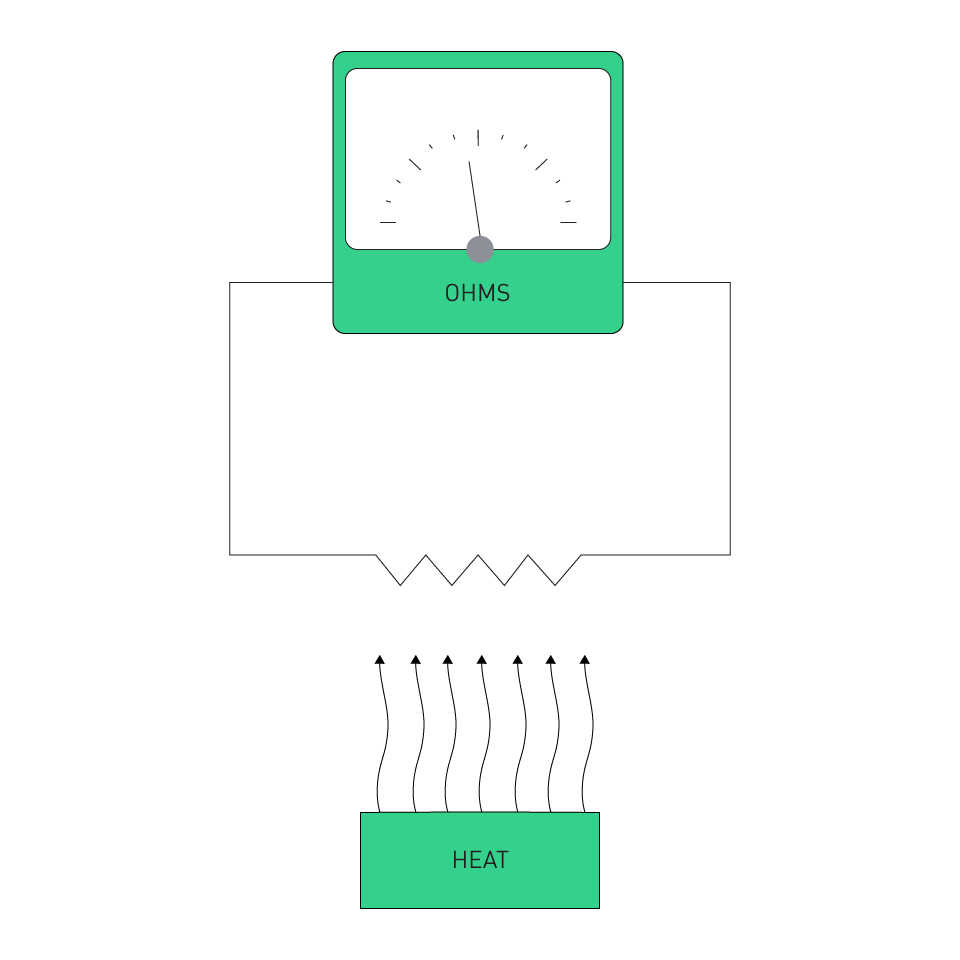
Figure 4: RTD working Principle
Materials: Pure Platinum
Pure platinum is the preferred material for the majority of premium RTDs. Because of its wide temperature range, consistent resistance-temperature connection, and chemical inertness (which results in great long-term stability), platinum is preferred. The term Pt100 refers to the conventional platinum resistance thermocouple, which has a resistance of 100 ohms at 0°C and a positive temperature coefficient.
Wheatstone Bridge Configuration
In order to determine the temperature, RTDs are frequently incorporated into Wheatstone bridge circuits to monitor the resistance change in them. Through the use of known resistors to compare the resistance of the RTD, the Wheatstone bridge, a four-resistor setup, provides accurate resistance measurements. The ratio of two resistors equals the ratio of the RTD to another known resistor when the bridge is balanced. Any variation in the RTD's resistance due to temperature throws off the bridge's equilibrium and results in a detectable voltage differential that is proportionate to the temperature.
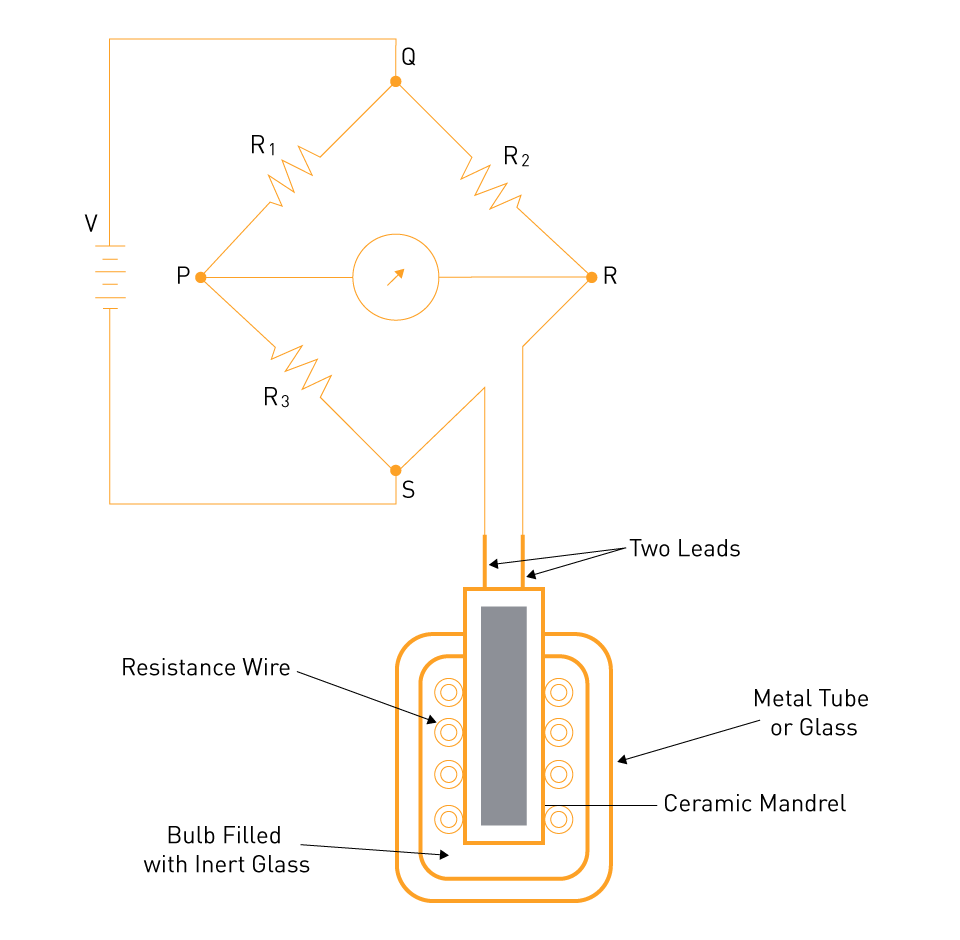
Figure 5: Measurement from RTD using Bridge
Accuracy and Linearity
The precision and linearity of RTDs are two of their best qualities. Compared to alternative temperature sensors:
Accuracy: RTDs have a high degree of precision throughout their operating range, frequently within ±0.1°C or better.
Linearity: Particularly in contrast to devices such as thermistors, the resistance-temperature connection for platinum RTDs is well-characterized and almost linear. Because of its linearity, less complicated compensating circuitry is required for the conversion of resistance to temperature.
Applications
A wide range of industries, including the chemical, automotive, aerospace, pharmaceutical, and food and beverage sectors, employ RTDs for temperature measurement and control. RTDs have a variety of specific uses, such as temperature measurement in industrial processes and control systems, temperature monitoring in HVAC (Heating, Ventilation, and Air Conditioning) systems, engine temperature sensing in the automotive industry, temperature control in production processes in the food and beverage industry, and more. For temperature readings, RTDs provide the best possible balance of precision, stability, and repeatability, particularly in industrial and laboratory environments where accuracy is crucial.
RTDs are reliable and stable, but it's important to remember that their response times are usually slower than those of thermocouples or thermistors, which makes them less useful for applications that need fast temperature measurements.
Thermistors
The resistance of thermocouples, which are temperature-sensitive resistors, changes dramatically with temperature—much more than that of ordinary resistors. "Thermal" and "resistor" are combined to get the phrase "thermistor". A thermistor's main job is to show a noticeable, dependable shift in resistance in response to changes in body temperature, which can be either positive or negative.
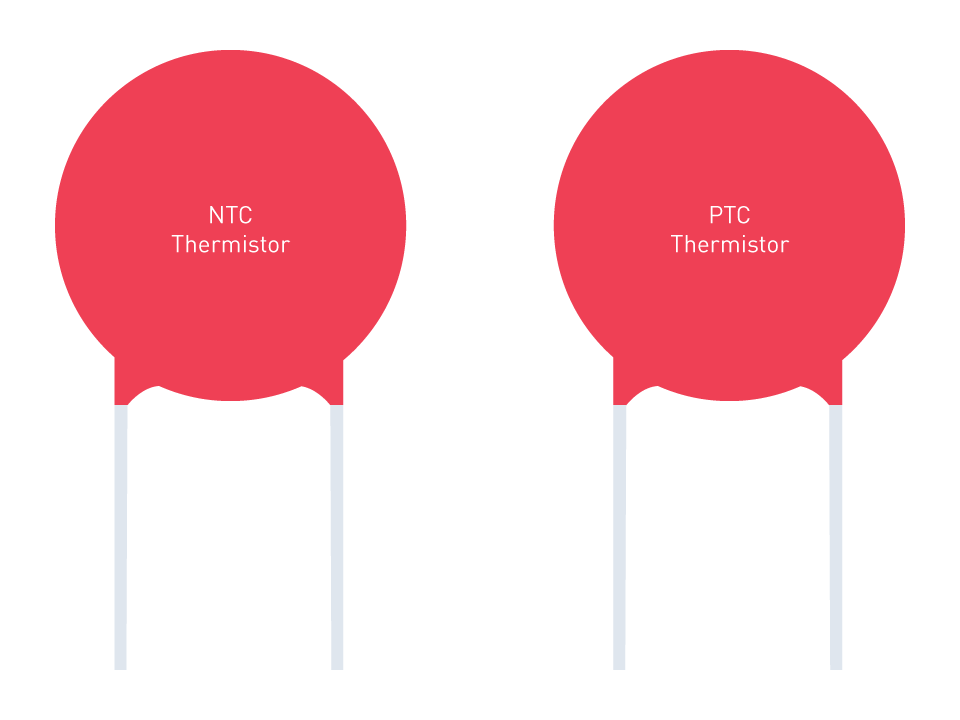
Figure 6: Thermistors (NTC and PTC)
Positive/Negative Temperature Coefficient (PTC/NTC)
The resistance-temperature connection of thermocouples can be broadly categorized into two categories:
Negative Temperature Coefficient (NTC): When the temperature rises, these thermistors show a decrease in resistance. The most popular kind of thermistors, NTCs are mostly used for controlling and measuring temperature. They are very sensitive due to their near-exponential resistance change with temperature, but this also results in a very non-linear response.
Positive Temperature Coefficient (PTC): PTC thermistors, in contrast to NTC, become more resistant as the temperature rises. Since their resistance increases significantly above a particular threshold, restricting the current flow, they are frequently employed in self-regulating heating components and over-current protection.
Materials: Metal Oxides
Metal oxides make up most thermistors; these oxides are sintered to create a material similar to ceramic. Oxides of manganese, nickel, cobalt, and copper are common materials. The unique temperature-resistance properties of thermistors are attributed to these materials. The resistance-temperature curve of the thermistor is determined by the particular combination of metal oxides and the manufacturing process.
Applications: Consumer Electronics, Medical Devices
Consumer Electronics: NTC thermistors are widely used for temperature monitoring, regulation, and compensation in electronics and home appliances because of their high sensitivity and quick response time. They are used, for example, to monitor operating temperatures in battery chargers, microwaves, and 3D printers.
Medical Devices: Thermistors are very useful in medical applications because of their accuracy and quick response. Thermistors are essential for maintaining patient safety and equipment effectiveness in a variety of applications, including body temperature monitoring systems (where body temperature measurements are crucial) and catheters that need real-time thermal feedback.
Finally, it should be noted that thermistors have a substantial niche in the temperature sensing industry due to their sensitive temperature-resistance relationship and wide application range. Although RTDs or thermocouples may be a better option in situations needing rapid and accurate temperature change detection, they perform very well in those that don't necessarily require linear responses over large temperature ranges.
Infrared Sensors
Infrared (IR) sensors are a special kind of temperature sensors that can identify infrared radiation, which is electromagnetic radiation with a frequency lower than visible light. These sensors have clear benefits from being able to measure temperature without physical contact, particularly in situations where traditional sensors might not be practicable.
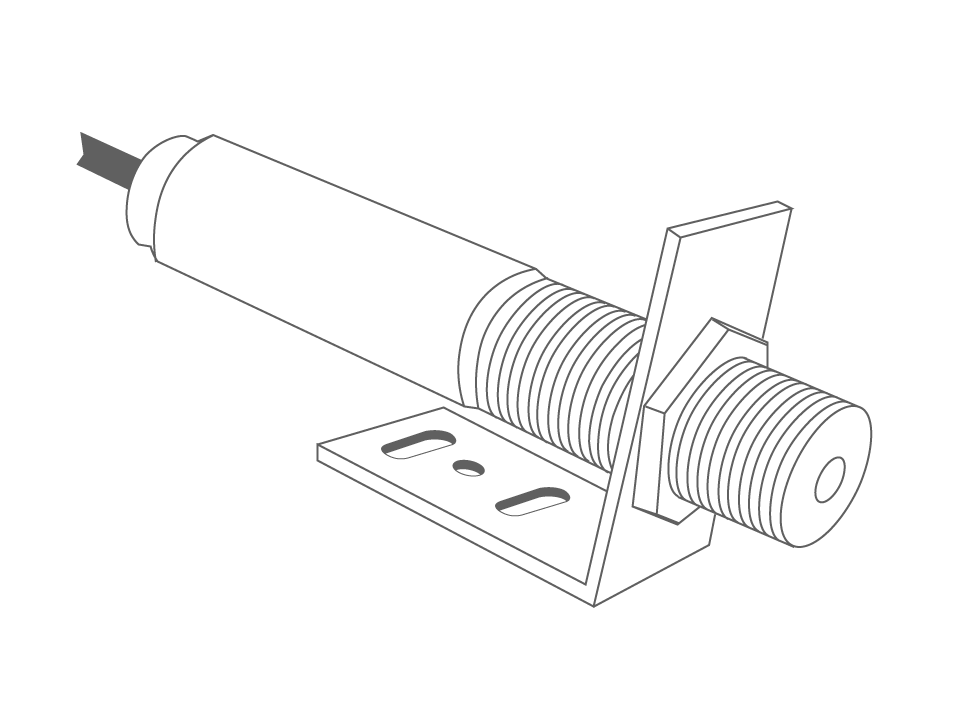
Figure 7: An IR Pyrometer
Principle of Infrared Radiation Detection
Infrared radiation is emitted by everything that has a temperature higher than zero. This radiation's strength is proportionate to the object's temperature. In order to function, infrared sensors—also known as pyrometers or infrared thermometers—capture this radiation and transform it into an electrical signal. This electrical signal is produced within the sensor by a detection element composed of materials like thermopiles or pyroelectric crystals. After that, a temperature reading is obtained by conditioning and translating this signal.
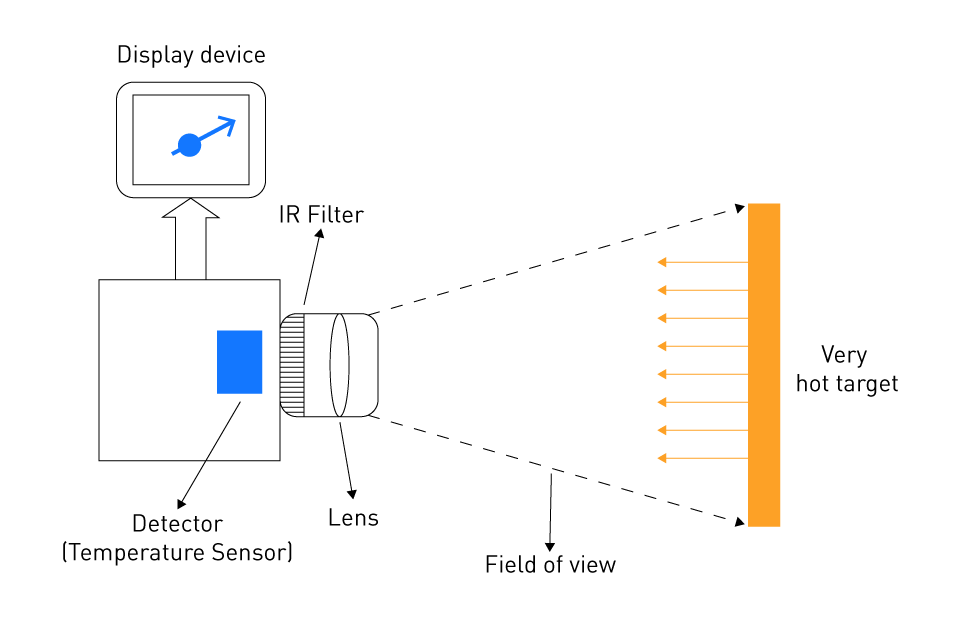
Figure 8: Working of an IR Pyrometer
Non-Contact Temperature Measurements
The ability of infrared sensors to assess temperatures without coming into direct touch with the thing being observed is one of their main advantages. When measuring the temperature of moving objects, potentially dangerous or inaccessible materials, or scenarios where a sensor could introduce contamination, this feature is quite helpful. The size of the region the infrared sensor will measure at a given distance is determined by a parameter called the distance-to-spot ratio. Making ensuring the measured area (spot) is completely inside the object's borders is essential for accurate readings.
Applications: Night Vision, Thermal Imaging
Night Vision: Infrared sensors are essential for night vision equipment because they can identify the infrared radiation that objects and living things release. Through the amplification of infrared radiation, these gadgets enable users to see in complete darkness in the absence of visible light.
Thermal Imaging: IR sensors are used by thermal imaging or thermographic cameras to record changes in an object's infrared emissions. Following that, these variances are converted into color representations, with each hue denoting a distinct temperature. With the use of this technology, personnel may locate "hot spots" in machines before they have a catastrophic failure, which is extremely useful in predictive maintenance applications. Additionally, it can be used in medical imaging to measure inflammation and perform vascular evaluations.
In addition to the above listed uses, infrared sensors are also employed in remote temperature monitoring for industrial operations, flame detection in safety systems, and body temperature screening—the latter of which is particularly important during health pandemics.
To sum up, infrared sensors cover a particular area within the range of temperature detecting technologies. Their value in contemporary engineering and technology contexts is shown by their wide range of applications and their capacity to measure temperature remotely.
直接登录
创建新帐号