Role of Thermal Management in Power Electronics
An essential aspect of power electronics design, thermal management has a direct impact on the efficiency, reliability, and lifespan of power conversion circuits. Power electronic devices generate heat as a result of inefficiencies in semiconductor materials and circuit components. This heat can build up without proper thermal management, resulting in high temperatures that degrade component performance, lower lifespan, and increase failure risk. In order to preserve ideal working conditions and guarantee the long lifespan of power conversion systems, this section examines the basic function of thermal management in power electronics.
Heat Generation in Power Electronics
Sources of Heat in Power Conversion Circuits: Conduction and switching losses in semiconductor devices such as transistors (e.g., MOSFETs, IGBTs) and diodes are the main sources of heat in power electronics. Switching losses occur during the change from the on to the off state, whereas conduction losses happen as current passes through the semiconductor material. Additionally, resistive losses and core losses (in magnetic components) are two more ways that passive components like resistors, transformers, and inductors can contribute to heat generation.
Impact of Heat on Component Performance: Power electronic components' electrical characteristics can alter as their temperature rises, frequently resulting in decreased efficiency and higher power loss. For instance, MOSFETs' on-resistance usually rises with temperature, increasing conduction losses. Additionally, high temperatures can result in thermal runaway, a process whereby rising temperatures induce greater losses and possibly component failure or, in extreme situations, fire.
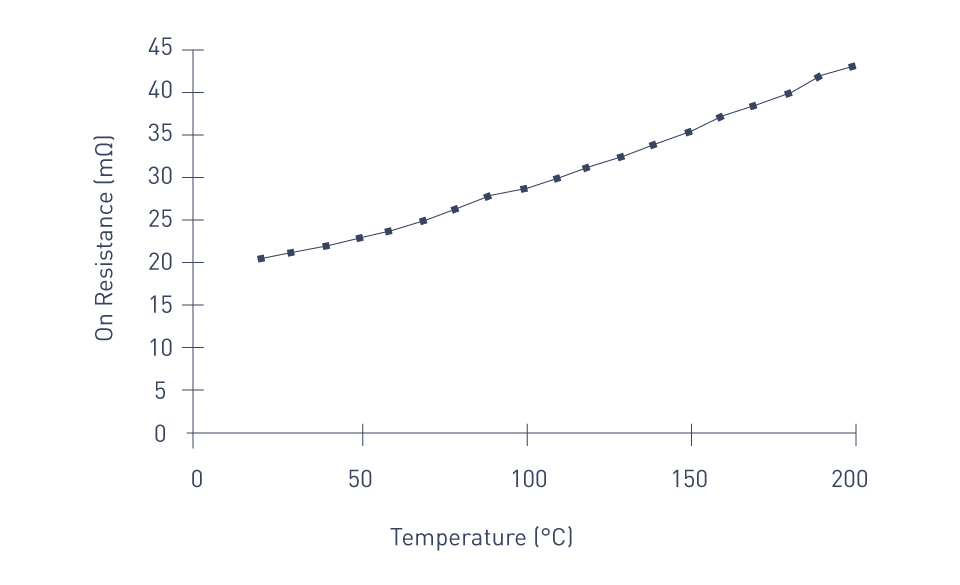
Figure 11: MOSFET on resistance vs temperature
Importance of Thermal Management
Maintaining Safe Operating Temperatures: Effective thermal management is required to keep components within their safe operating temperature range. Overheating these temperature thresholds may cause immediate damage or long-term deterioration, which would lower the power conversion circuit's reliability. Thermal management keeps components cool so they may function effectively and within their designated ratings, preventing catastrophic failures and performance deterioration.
Enhancing Reliability and Lifespan: One of the main factors of electronic component aging is thermal stress. High temperatures accelerate the breakdown of dielectric materials, electromigration in interconnects, and mechanical wear brought on by thermal cycling, among other failure mechanisms. Effective thermal management lowers these stresses, prolonging the life of power electronic components and enhancing system reliability in general.
Ensuring Consistent Performance: Temperature differences can cause performance deviations in power conversion circuits. For instance, at higher temperatures, semiconductors' switching speeds may slightly increase, which could impact the circuit's efficiency and dynamic response. Maintaining stable operating conditions through consistent thermal management helps guarantee that the power converter operates reliably under a variety of operating conditions.
Thermal Management as Part of the Design Process
Integrated Approach to Thermal Design: Instead of being an afterthought, thermal management ought to be incorporated into the design process from the beginning. Thermal effects must be considered while selecting components, laying out PCBs, and designing systems. Designers, for example, must consider thermal resistance, calculate power dissipation, and choose components with acceptable thermal ratings. In order to improve heat dissipation, the layout should also be improved. For example, heat-generating components should be attached to heat sinks or placed in locations with higher airflow.
Regulatory Compliance and Standards: Thermal management is also critical for achieving regulatory requirements for safety and reliability. Specific thermal performance requirements, such as maximum allowable temperatures, cooling efficiency, and thermal protection measures, are present in many industries. Product certification and market acceptance require adherence to these requirements.
Impact on System Efficiency and Cost: While proper thermal management is essential for reliability, it also affects system efficiency and cost. For instance, adding fans, heat sinks, or liquid cooling systems might enhance thermal performance, but doing so may make the system larger, more complicated, and more expensive. As a result, designers must strike a compromise between thermal management requirements and the system's overall efficiency and economic considerations.
Techniques for Effective Heat Dissipation
Effective heat dissipation is critical in power conversion circuits to prevent overheating, preserve performance, and increase the lifespan of electronic components. As power electronics function, they inevitably generate heat, which must be regulated to avoid thermal stress and potential failure. To effectively dissipate heat and guarantee that power conversion systems function within their thermal limits, a variety of techniques are used. Conduction, convection, radiation, and advanced cooling techniques are some of the important techniques for effective heat dissipation that are explored in this section.
Conduction: The Foundation of Heat Dissipation
Thermal Conduction: The principal heat transmission mechanism in power electronics is conduction, in which heat produced by components is transferred to cooler regions via solid materials such as the semiconductor package, PCB, or heat sink. The thermal conductivity of the materials used determines the conduction efficiency. Metals with high thermal conductivity, such as copper and aluminum, which are often used in PCBs and heat sinks, are good heat dissipators.
PCB Design for Enhanced Conduction: In power electronics, the PCB is crucial in transferring heat away from components. Techniques for improving conduction across the PCB include:
- Thicker Copper Layers: Increasing the thickness of the PCB's copper layers enhances heat conduction, allowing for more efficient heat transmission from the components to the board.
- Thermal Vias: Placing thermal vias beneath heat-generating components allows heat to be transferred from the PCB's top layer to the interior layers or the opposite side, so distributing the heat more effectively and reducing localized hot spots.
- Heat Spreading Planes: Using specialized thermal planes within the PCB, frequently connected to ground or power layers, helps disperse heat evenly and decreases the thermal resistance from the components to the ambient environment.
Convection: Moving Heat Away from Components
Natural Convection: Convection is the transfer of heat via a fluid, usually air, that moves heat away from heated surfaces. Natural convection occurs when warm air rises due to its lower density, allowing cooler air to enter and replace it. This is a passive technique that dissipates heat through the natural movement of air. Components should be oriented and spaced to allow for free passage of air, which maximizes cooling effect.
Table 5: Natural vs. forced convection
Aspect | Natural Convection | Forced Convection |
---|---|---|
Mechanism | Heat transfer occurs due to the natural movement of fluid caused by temperature differences | Fluid movement is induced by an external force, such as a fan or pump |
Flow Type | Flow is driven by buoyancy effects | Flow is actively generated by a mechanical device (e.g., fan, pump) |
Efficiency | Less efficient due to slower fluid movement | More efficient because the external force increases the fluid flow rate |
Applications | Used in passive cooling systems | Used in active cooling systems |
Complexity | Simpler, no external power source required | More complex, requires a power source (fan, pump) |
Control | Harder to control, as it depends on temperature differences | Easier to control by adjusting the flow rate |
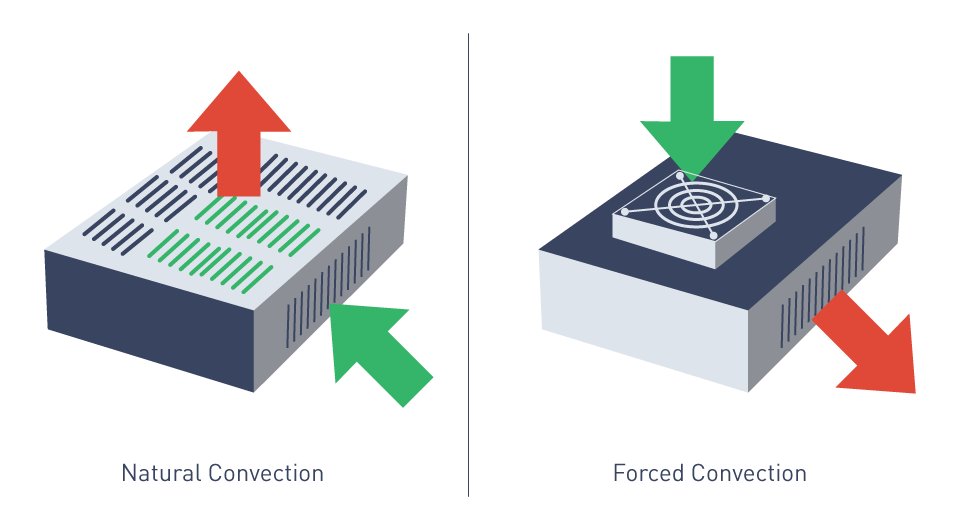
Figure 12: Natural vs. forced convection
Forced Convection: Forced convection, which usually uses fans or blowers to actively move air across the heat-generating components, is employed when natural convection is insufficient. When compared to natural convection, forced convection significantly accelerates heat transfer, which makes it appropriate for high-power applications. Forced convection considerations include:
- Airflow Direction: Cooling efficiency is maximized by designing the system so that airflow bypasses other sections of the circuit and flows directly over the hottest components.
- Fan Placement and Sizing: Large systems may employ multiple fans or ducts to distribute airflow equally, but proper fan placement and sizing are essential to ensuring adequate airflow over all key components.
Radiation: Emitting Heat to the Surroundings
Radiative Heat Transfer: The process by which heat is released from a surface as electromagnetic waves, mostly in the infrared spectrum, is known as radiation. While radiation is less important than conduction or convection in most power electronics applications, it can nonetheless contribute to heat dissipation, particularly in environments with limited airflow.
Surface Treatments to Enhance Radiation: Changing the surface characteristics of components and heat sinks can improve the efficiency of radiative heat transfer. Techniques include:
- Surface Coatings: By adding high-emissivity coatings, including black anodization, to aluminum heat sinks, more heat is dissipated from the surface, enhancing thermal management in overall.
- Increasing Surface Area: Finned heat sinks or other designs that enhance the surface exposed to the environment can be used to maximize the surface area, which improves the effectiveness of radiative heat dissipation.
Advanced Cooling Techniques
Heat Sinks: Heat sinks are one of the most frequent ways to improve heat dissipation in power electronics. They increase the surface area in contact with the air, which facilitates heat transfer via conduction and convection. Types of heat sinks include:
- Extruded Heat Sinks: These heat sinks are typically composed of aluminum and have fins to maximize surface area and convection.
- Bonded or Stamped Fin Heat Sinks: These heat sinks have fins that are glued or stamped onto the base, providing even more surface area and increased cooling efficiency.
- Embedded Heat Pipes: Some heat sinks include heat pipes that transmit heat fast from the base to the fins, boosting overall heat dissipation efficiency.
Thermal Interface Materials (TIMs): By decreasing the thermal resistance between surfaces and filling air gaps between heat-generating components and heat sinks, TIMs improve thermal conduction.
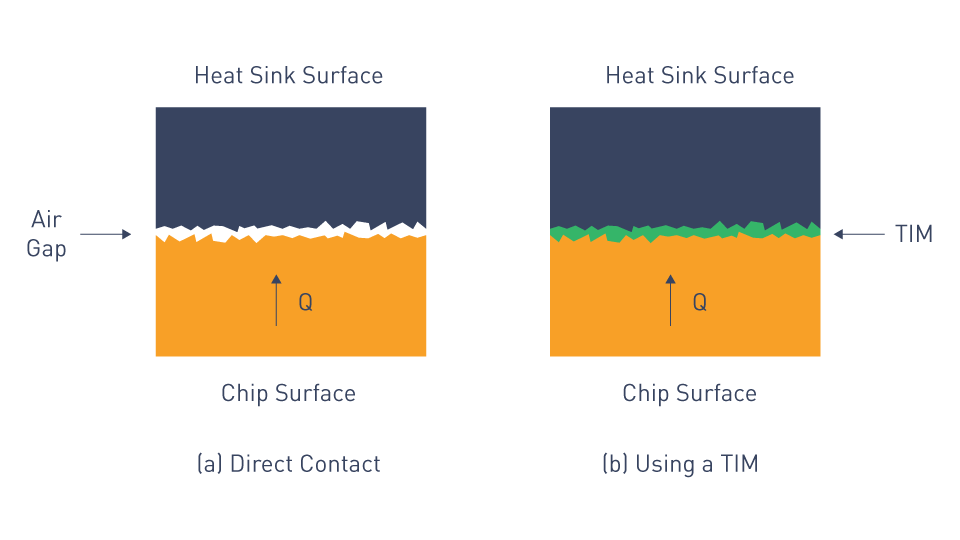
Figure 13: Thermal interface materials
Common TIMs include:
- Thermal Grease: To guarantee enough thermal contact and close microscopic air gaps, a paste is applied between the component and the heat sink.
- Thermal Pads: Pre-formed pads composed of materials such as silicone or graphite are employed where set-up is simple and performance is consistent.
- Phase-Change Materials: These materials change state at specific temperatures to improve thermal conductivity when the device is subjected to high heat loads.
Liquid Cooling: In high-power applications where air cooling is insufficient, liquid cooling can be used. This entails passing a coolant (such as water or a specialized fluid) via channels or pipes in contact with heat-generating components. The coolant absorbs heat and then circulates to a radiator, where it is dispersed into the environment.
- Closed-Loop Systems: To ensure cooling efficiency, these systems circulate coolant in a closed loop through pumps, radiators, and heat exchangers. They are widely employed in high-performance computing, automotive, and industrial power electronics.
- Direct Liquid Cooling: Direct liquid cooling involves the coolant coming into direct contact with the components being cooled, resulting in the highest heat transfer efficiency. This approach necessitates careful designing to ensure electrical isolation and prevent leaks.
Hybrid Cooling Solutions
Combination of Techniques: To achieve the desired thermal performance in many applications, a combination of cooling techniques are used. For instance, a power converter might employ forced convection with fans, radiative cooling with surface treatments, and conduction through the PCB and heat sinks. To maximize efficiency and guarantee that all components stay within safe temperature ranges, hybrid cooling systems can also incorporate both liquid and air cooling to control heat in various system components.
Thermal Analysis and Simulation Tools
Advanced software tools are available for analyzing, modeling, and simulating thermal performance, allowing designers to improve heat dissipation techniques before design finalization. These tools simulate airflow, temperature distribution, and the effects of various materials and cooling systems, allowing to discover potential hot spots and enhance overall thermal efficiency.
Designing for Thermal Efficiency
For electrical components to function within their specified temperature limits, retain reliability, and perform at their best, power conversion circuits must be designed with thermal efficiency in mind. Heat sinks and cooling systems are critical components of this design process, serving as methods for dispersing heat generated by power electronics. This section delves into the concepts of thermal efficiency design, with a focus on how to effectively control heat in power conversion circuits using heat sinks and cooling systems.
Thermal Efficiency in Power Electronics
Thermal efficiency in power electronics refers to a system's ability for effectively dissipate heat produced during operation. A thermally efficient design reduces component temperature rise, which improves reliability and life span. Thermal efficiency is achieved by maximizing the system's heat transmission processes, such as conduction, convection, and radiation, while also reducing thermal resistance.
Thermal Resistance and Junction Temperature: The ability of a system or component to transfer heat from its source (such as a semiconductor junction) to the environment is measured by its thermal resistance. Lower thermal resistance improves heat dissipation and lowers junction temperatures, both of which are crucial for power electronic device reliability. To achieve optimal thermal performance, designers need to consider both the case-to-ambient thermal resistance (via the heat sink and cooling systems) and the junction-to-case thermal resistance (within the component).
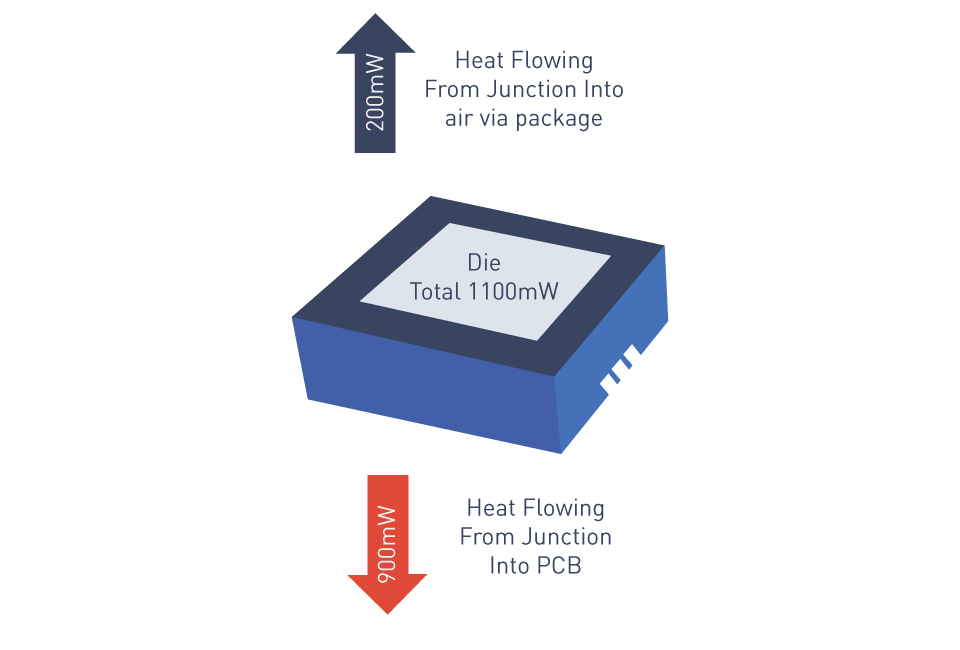
Figure 14: Junction-to-Case Thermal Resistance
Designing Effective Heat Sinks
Heat Sink Selection and Design: Heat sinks are passive devices that absorb and dissipate heat from power components into the surrounding environment. The effectiveness of a heat sink is determined by its material, surface area, and design. Key factors to consider include:
- Material Selection: The most widely utilized materials for heat sinks are copper and aluminum because of their excellent thermal conductivity. Aluminum is a popular choice for many applications because it is lighter and more affordable than copper, despite copper's higher thermal performance. To balance cost and performance, some designs use a blend of both materials.
- Surface Area and Fin Design: The heat sink's ability to dissipate heat is directly related with its surface area. Fins increase the surface area, which facilitates more effective heat transfer to the surrounding air. To maximize airflow and heat dissipation, fin design, including size, shape, spacing, and orientation is essential. For instance, pin fins can be employed to improve performance in natural convection, while straight fins are straightforward and efficient in forced convection environments.
- Optimizing Thermal Interface Materials (TIMs): Thermal performance depends on the interface between the heat-generating component and the heat sink. TIMs, such as thermal grease, pads, or phase-change materials, are used to fill microscopic gaps between the component and the heat sink, lowering thermal resistance. Properly choosing and applying an appropriate TIM guarantees efficient heat transfer and lowers the component's junction temperature.
- Mounting and Mechanical Considerations: To guarantee optimal thermal contact with the component, the heat sink must be mounted properly. To optimize the TIM's performance and reduce heat resistance, the mounting technique should apply consistent pressure over the surface. Common mounting techniques include clamps, screws, and adhesive tapes; each has benefits specific to the application.
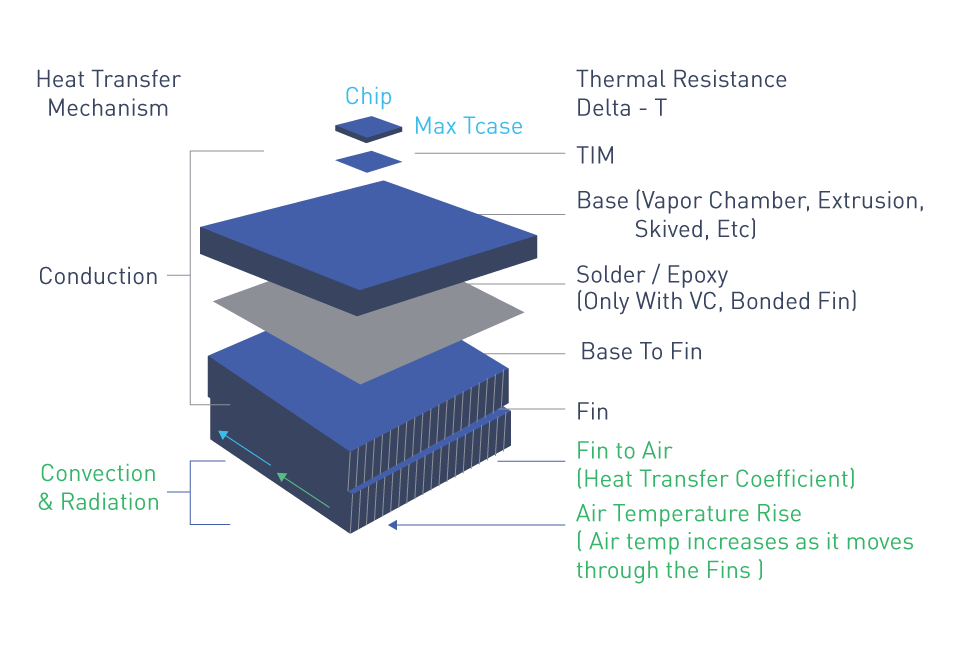
Figure 15: Heat transfer via heat sink
Implementing Cooling Systems
Active Cooling vs. Passive Cooling: Cooling systems in power electronics can be classed into active and passive methods. While active cooling uses fans, blowers, or liquid cooling systems to improve heat dissipation, passive cooling depends on radiation and natural convection.
- Passive Cooling: For low to moderate power applications where natural convection can dissipate heat, passive cooling is frequently sufficient. This approach is preferred due to its ease of use, reliability, and noiseless operation. Optimizing airflow around the heat sink and making sure that heat can efficiently radiate away from the system are the main focus of passive cooling system design.
- Active Cooling: Active cooling systems are used in high-power applications where passive cooling is insufficient. To improve convection and minimize component temperature rise, fans or blowers are frequently employed to boost airflow over heat sinks. Although active cooling systems have the potential to significantly enhance thermal performance, they come with additional complexity, power requirements, and the potential for noise and mechanical wear over time.
Liquid Cooling Systems: Liquid cooling systems offer a practical substitute for air cooling in applications where high power densities or harsh climatic conditions make air cooling inadequate. In liquid cooling, a coolant (such as water or a specialized fluid) is circulated through tubes or channels that are in close proximity to heat-generating components.
- Heat Exchangers and Radiators: Heat exchangers or radiators, which transfer the heat absorbed by the coolant to the surrounding atmosphere, are frequently used in liquid cooling systems. These systems are perfect for high-performance or high-reliability applications because they can dissipate a lot more heat than air cooling.
- Pumps and Fluid Dynamics: The efficiency of a liquid cooling system is determined by the pump's design and the fluid dynamics within it. While the cooling channels' design must minimize pressure drop and guarantee uniform cooling across all heat sources, the pump must have a high enough flow rate to transfer heat away from the components.
- Maintenance Considerations: While liquid cooling systems offer higher thermal performance, they require careful design to minimize leaks, corrosion, and contamination of the coolant. Regular maintenance is important to guarantee the system performs properly over its lifespan.
Design Strategies for Thermal Efficiency
System-Level Thermal Design: A comprehensive approach that considers every aspect of the system, such as enclosure design, PCB layout, and component placement, is necessary to achieve thermal efficiency. To prevent localized hotspots, heat sources should be distributed, and components with high thermal dissipation should be placed close to heat sinks or in areas with optimal airflow.
Simulation and Thermal Modeling: Thermal simulation and modeling tools are crucial for maximizing heat sink and cooling system design efficiency. Before physical prototyping, these technologies enable designers to predict temperature distribution, detect potential thermal bottlenecks, and assess the efficiency of various cooling techniques. Engineers can enhance thermal performance and prevent expensive redesigns by iterating the design using simulations.
Scalability and Modularity: In certain applications, the thermal design needs to be scalable in order to support modular configurations or varying power levels. A modular power converter, for instance, might need to function well at various power levels, necessitating a thermal design that is simple to scale or modify. Modular heat sinks and cooling solutions can be developed to fit a variety of designs while maintaining thermal efficiency.
Impact of Temperature on Performance and Lifespan
Temperature is an important element influencing the performance, reliability, and lifespan of power conversion circuits. When power electronic components operate, they produce heat, which, if not managed effectively, can result in substantial thermal stress. Elevated temperatures can affect component electrical characteristics, diminish efficiency, and accelerate deterioration mechanisms, resulting in premature failure. This section examines the effect of temperature on the performance and lifespan of power electronics, emphasizing the critical role of proper thermal management in system integrity.
Temperature and Electrical Performance
Thermal Effects on Semiconductor Devices: MOSFETs, IGBTs, and diodes are examples of semiconductor devices that are extremely sensitive to temperature variations. These devices' junction temperature affects a number of key electrical parameters, including:
- On-Resistance: The on-resistance of MOSFETs rises with temperature. Increased conduction losses from higher on-resistance lower the power converter's overall efficiency. Additionally, this rise in on-resistance generates more heat, which, if left unchecked, could result in a thermal runaway condition.
- Threshold Voltage: As the temperature rises, MOSFETs' threshold voltage frequently decreases, which alters the switching properties of the device. A lower threshold voltage can cause the device to turn on unintentionally, increasing leakage current and perhaps causing circuit instability.
- Switching Losses: Higher temperatures cause increased carrier mobility and other thermal effects, which slow down the switching speed of semiconductor devices. Higher switching losses brought on by slower switching increase heat generation and reduce the circuit's overall efficiency.
Impact on Passive Components: Temperature also has an impact on passive components including resistors, capacitors, and inductors:
- Capacitors: Power electronics frequently use electrolytic capacitors, which have a shorter lifespan and less capacitance at higher temperatures. Over time, the capacitor's electrolyte can evaporate, resulting in a loss of capacitance and a rise in equivalent series resistance (ESR), both of which degrade circuit performance.
- Inductors: Variations in temperature can cause inductors to fluctuate in inductance and core losses. High temperatures can cause the core material's magnetic characteristics to deteriorate, increasing core losses and decreasing inductance, both of which can impair the power converter's overall performance.
- Resistors: Most resistive materials' resistance increases with temperature, which can have an impact on power conversion circuits' ability to sense current and regulate voltage. Control loop inaccuracies can result from precision resistors used in feedback networks drifting out of their specified tolerance range.
Temperature and Reliability
Thermal Stress and Component Degradation: Prolonged exposure to high temperatures accelerates different deterioration mechanisms in electronic components, greatly reducing their reliability. Among these mechanisms are:
- Electromigration: Electromigration refers to the displacement of metal atoms within interconnects caused by high current densities, which is aggravated by rising temperatures. This process can cause thinning and eventual breakdown of metal traces, resulting in open or short circuits within the device.
- Dielectric Breakdown: When exposed to high temperatures, dielectric materials used in capacitors and semiconductor devices lose their insulating properties over time. This can lead to dielectric breakdown, resulting in short circuits or leakage currents that jeopardize the circuit's operation.
- Thermal Cycling: Repeated temperature cycling (heating and cooling) can produce mechanical stress in materials due to differences in expansion rates between different materials. Solder joints, wire bonds, and package interfaces may develop fractures as a result of this stress, which could ultimately cause mechanical failure.
Acceleration of Aging Processes: According to the Arrhenius equation, aging processes accelerate with temperature; for example, a 10°C rise in operating temperature can about double the rate of degradation-causing chemical reactions. This relationship emphasizes how crucial it is to maintain the lowest temperatures possible in order to prolong the life of power electronic components.
Impact on System Mean Time Between Failures (MTBF): The mean time between failures (MTBF), which is inversely related to the failure rate, is frequently used to measure the reliability of power conversion circuits. High operating temperatures raise the failure rate, which lowers the MTBF and, as a result, the system's overall reliability. Maintaining a high MTBF requires efficient temperature management, especially in mission-critical applications such as industrial, automotive, and aerospace systems.
Strategies for Minimizing Thermal Impact
Thermal Design Considerations: Designers must integrate thermal management techniques from the very beginning of the design process to reduce the effect of temperature on lifespan and performance:
- Component Selection: Selecting components with higher temperature ratings and lower thermal coefficients can help mitigate the effects of temperature variations. Performance under thermal stress can be enhanced, for instance, by selecting capacitors with higher thermal stability and MOSFETs with lower on-resistance.
- Thermal Derating: Operating components at temperatures lower than their maximum rated temperature, known as derating, can greatly extend their lifespan. Thermal derating is designing the system to function at temperatures significantly lower than the component's maximum ratings, hence ensuring reliability and longevity.
- Effective Cooling Solutions: Lower operating temperatures are maintained by using heat sinks, fans, or liquid cooling systems, which lessens the thermal load on components. The power density of the system, environmental conditions, and the need for reliability should all be taken into consideration when selecting a cooling solution.
Real-Time Thermal Monitoring: To detect and respond to variations in temperature, advanced power conversion systems frequently use real-time thermal monitoring. Sensors can be placed close to crucial components to give the control system feedback, allowing for dynamic adjustments such as lowering load, speeding up fans, or shutting down the system to avoid overheating.
Long-Term Implications and Design for Reliability
Design for Longevity: In high-reliability applications, designing for longevity involves considering the long-term impacts of temperature on every component of the system in addition to thermal management. This entails choosing materials that are resistant to heat deterioration, developing components that are simple to maintain and replace, and making sure the thermal management system is sturdy and reliable.
Predictive Maintenance: Predictive maintenance techniques can be used to anticipate and address potential issues before they happen by tracking temperature and other operating parameters over time. In order to prevent unplanned downtime and enable proactive maintenance, this technique uses thermal modeling and historical data to anticipate when a component is likely to break as a result of thermal stress.
直接登录
创建新帐号