Overview of Environmental Regulations Impacting Power Electronics
The design, manufacturing, and disposal of power electronics are significantly influenced by environmental regulations. Regulatory frameworks have been established to restrict the environmental impact of electronic devices over the course of their lifecycle in response to the growing demand for eco-friendly and sustainable products. The evolution of power electronic systems is influenced by two fundamental directives, Waste Electrical and Electronic Equipment (WEEE) and Restriction of Hazardous Substances (RoHS).
RoHS Directive
The RoHS Directive, which was first introduced in the EU in 2003, limits the use of specific hazardous materials in electronic products with the goal of enhancing their sustainability and minimizing their environmental impacts. RoHS restricts the use of the following substances and is applicable to the production, distribution, and importation of electrical and electronic equipment:
- Lead (Pb)
- Mercury (Hg)
- Cadmium (Cd)
- Hexavalent chromium (Cr6+)
- Polybrominated biphenyls (PBB)
- Polybrominated diphenyl ethers (PBDE)
RoHS 2 was amended in 2011, and RoHS 3 (Directive 2015/863) was expanded in 2015 to include four more phthalates used in plastic materials. For power electronics to be sold in the EU, certain regulations must be followed, especially for components such as circuit boards, solder, and connectors.
For power electronics manufacturers, this includes selecting components and materials that comply with RoHS regulations and ensuring that no restricted substances exceed the allowable limits. Product recalls, financial penalties, and restrictions on market access can result from noncompliance with RoHS.
WEEE Directive
Another important regulation that has an impact on power electronics is the WEEE Directive. This directive, which was revised in 2012 (WEEE 2) after being adopted in the EU in 2003, focuses on the proper recycling and disposal of electrical and electronic waste. The goal of the directive is to promote the recovery, reuse, and recycling of materials used in electronics while decreasing the amount of electronic trash produced.
The WEEE Directive establishes extended producer responsibility (EPR), which means that power electronics manufacturers and distributors are responsible for the end-of-life management of their products. This involves offering systems for the collecting and recycling of waste equipment, ensuring that products are designed for easy disassembly, and reducing the environmental impact of the disposal process.
WEEE compliance requires power electronics manufacturers to:
- Designing products to be easily recycled while keeping material recovery and disassembly in mind.
- Minimizing the use of materials that are difficult to dispose of or recycle.
- Participating in take-back and recycling programs to facilitate proper e-waste disposal.
Global Adoption and Expansion of Regulations
Despite the European Union being the birthplace of RoHS and WEEE, several nations have adopted similar environmental laws. For example:
- China RoHS: Hazardous materials in electronic products are likewise restricted by China's version of the RoHS directive.
- Japan’s Home Appliance Recycling Law: This regulation focuses on recycling particular categories of electronics, such as refrigerators, televisions, and air conditioners.
- California’s Electronic Waste Recycling Act: This legislation imposes a fee on consumers who purchase certain electronic devices to fund the safe disposal and recycling of e-waste.
Implications for Power Electronics
Environmental regulations such as RoHS and WEEE have a substantial impact on power electronics manufacturers:
Material Selection: Materials that adhere to RoHS regulations must be carefully chosen by engineers, especially when soldering and manufacturing PCBs.
Product Design: Power electronics need to be designed with easily detachable components that allow efficient material recovery in order to be recyclable.
Supply Chain Management: To guarantee that components are verified as RoHS-compliant and tracked throughout the product lifecycle, manufacturers must collaborate with suppliers.
Eco-Design Principles for Sustainable Power Electronic Design
An approach to product development known as "eco-design" places a high priority on environmental sustainability at every stage of a product's lifespan, from sourcing and manufacturing of materials to usage and disposal at the end of its useful life. While preserving performance and reliability, eco-design principles in power electronics seek to reduce the environmental impact of components including power converters, inverters, and controllers. Power electronics development that incorporates eco-design enhances long-term sustainability by lowering energy use, easing recycling, and minimizing resource consumption, in addition to helping to comply with regulatory standards.
Minimizing Material Use
The efficient use of materials is a cornerstone of eco-design. This entails choosing materials with lower of an impact on the environment and lowering the amount of raw materials needed to manufacture power electronic devices. Among the strategies for reducing materials used are:
Lightweighting: Utilizing lighter components in power electronics design, such as smaller capacitors and thinner PCB substrates, lowers material usage and transportation energy expenses.
Material Substitution: Replacing hazardous or environmentally harmful materials (such as lead and certain flame retardants) with safer alternatives increases compliance with RoHS requirements while lowering toxicity.
Modular Design: By designing modular systems, product lifecycles can be extended, making upgrades and repairs easier and eliminating the need to replace entire devices.
Energy Efficiency and Low-Power Design
Enhancing power electronic systems' energy efficiency over the course of their operational life is a top priority for eco-design. Designers can significantly minimize a device's overall environmental impact by optimizing energy consumption and minimizing power losses. Important strategies consist of:
High-Efficiency Topologies: Energy waste can be reduced by selecting converter topologies that minimize switching losses and increase overall efficiency, such as zero-voltage switching (ZVS) or resonant converters techniques.
Power Factor Correction (PFC): By integrating PFC circuits, power converters are guaranteed to draw electricity in a manner that optimizes efficiency and reduces grid losses, which lowers overall energy usage.
Standby Power Reduction: Power electronic devices frequently spend a lot of time in standby mode. Energy waste in consumer and industrial electronics can be significantly decreased by designing for ultra-low standby power consumption, sometimes known as "phantom load" reduction.
Design for Longevity and Reliability
Increasing the operating lifespan of power electronics is one of the best strategies to reduce their environmental impact. Eco-design promotes the development of robust, long-lasting products that need to be replaced less frequently, which lowers the amount of energy and raw materials used in production and transportation. Important strategies consist of:
Robust Component Selection: Longer device lifespans and fewer failures are guaranteed when high-quality components are used, which can withstand varying environmental conditions, including temperature changes and electrical stress.
Thermal Management: Utilizing heat sinks, thermal vias, and advanced cooling systems to efficiently dissipate heat prevents components from thermal degradation, boosting reliability and extending the product's lifespan.
Maintenance and Repairability: Product longevity is increased by designing power electronics for easy maintenance, repair, and upgrade. Users are encouraged to fix rather than throw out devices when components are easily accessible or replaceable.
End-of-Life Design Considerations
Planning for a product's end of useful life is a crucial aspect of eco-design, which aims to maximize the recovery of valuable materials and minimize waste. Design for disassembly (DfD), recycling, and the use of recyclable or biodegradable materials are ways to do this. Important tactics consist of:
Design for Disassembly: Power electronics can be easily disassembled for recycling or reuse at the end of their life by simplifying the disassembly process, utilizing fewer fasteners, eliminating permanent bonding, and clearly labeling recyclable components.
Material Recycling: Choosing easily recyclable materials, such as certain metals, ceramics, and plastics, helps lessen the impact on the environment and the demand for virgin materials. Eco-design should prioritize reducing the usage of mixed materials, which can complicate recycling efforts.
Modular Components: Designing power electronics with interchangeable modules enables particular device components to be replaced or upgraded, extending the overall system's life and decreasing the need for complete replacement.
Lifecycle Assessment (LCA) and Environmental Impact Analysis
A Lifecycle Assessment (LCA), which assesses a product's environmental impact from cradle to death, is an essential part of eco-design.
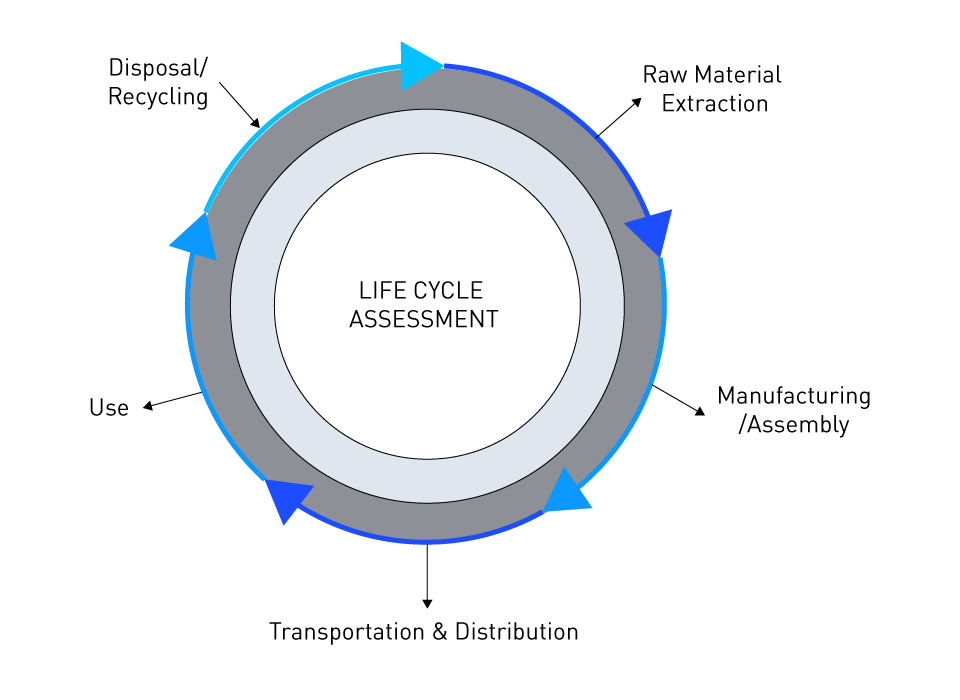
Figure 12: LCA
LCA offers a thorough view of the materials and energy utilized at every stage of a product's lifecycle, including:
Raw material extraction: The environmental cost of acquiring metals, plastics, and other materials.
Manufacturing: Emissions and energy consumption related to the manufacturing process.
Transportation: the carbon impact associated with the transportation of materials and finished products.
Use phase: Emissions and energy consumption while the power device is operating.
End-of-life: The impact of disposal, recycling, or reuse of materials.
By evaluating the entire lifecycle of power electronics, designers can optimize material use, energy efficiency, and waste management while minimizing the environmental impact at each stage.
Case Study: Eco-Design in Power Supplies
To lower the impact of their products on the environment, a major power supplies manufacturer used eco-design principles. By removing lead-based solder and lowering the amount of hazardous materials, the company modified its line of switch-mode power supplies (SMPS) to adhere to RoHS and WEEE regulations. High-efficiency power factor correction circuits were also integrated by the company to lower standby power usage and energy waste. The power supplies' usable lives were increased, and e-waste was decreased by employing modular designs, which also made repairs and upgrades simpler.
The company met strict environmental standards, improved the marketability of its products in eco-conscious regions, and reduced the carbon footprint of its power supplies by 30% as a result of these efforts.
Lifecycle Analysis and Environmental Impact Assessment
When evaluating the environmental impact of power electronics from cradle to grave, lifecycle analysis (LCA) and environmental impact assessment (EIA) are essential tools. These methods provide a thorough way for evaluating the environmental effects of a product's extraction of raw materials, production, consumption, and eventual disposal or recycling. LCA and EIA assist engineers in designing products that satisfy both functional and environmental requirements in the field of power electronics, where efficiency, sustainability, and regulatory compliance are becoming more and more crucial.
Lifecycle Analysis (LCA) Overview
LCA is a systematic technique for measuring a product's environmental effects over the course of its entire lifecycle. LCA offers a framework for comprehending how design, material selection, production procedures, and disposal techniques impact the overall environmental footprint in the context of power electronics. There are four primary stages to this analysis:
Goal and Scope Definition:Defining the goal of the LCA, including the processes and environmental implications to be examined. This could entail assessing manufacturing emissions, component recyclability, or energy usage during operation in power electronics.
Life Cycle Inventory (LCI):Data collecting on material flows, energy use, and emissions throughout a power electronic product's lifecycle is part of this phase. For instance, the LCI for power converters might monitor the extraction of raw materials (such as metals for semiconductors), energy consumption during component production, emissions from transportation, and power consumption when the device is in use.
Life Cycle Impact Assessment (LCIA):The LCI data is converted into environmental impact indicators at this stage. These could include the discharge of dangerous chemicals, resource depletion, energy and water use, and the potential for global warming (GWP). LCIA can identify areas in power electronics where material substitutions or increases in energy efficiency could significantly reduce the overall environmental impact.
Interpretation:To identify opportunities for reducing environmental impacts, the results of the LCI and LCIA are assessed. To build more sustainable power electronic devices, designers and engineers can utilize this data to inform decisions about material selection, design improvements, or process adjustments.
Table 10: LCA vs. EIA
Feature | Lifecycle Analysis (LCA) | Environmental Impact Assessment (EIA) |
---|---|---|
Purpose | Evaluates the environmental impacts throughout the entire lifecycle of a product or process | Assesses the potential environmental impacts of a proposed project or development |
Scope | Covers raw material extraction, production, use, and disposal | Focuses on the environmental effects of specific projects or activities |
Approach | Quantitative, often involves detailed modeling and data collection | Qualitative and quantitative, with a focus on predicting and mitigating impacts |
Application | Product design, sustainability efforts, process improvement | Infrastructure projects, industrial developments, construction projects |
Regulatory Requirement | Often voluntary, but may be required for sustainability certifications | Typically required by law for large-scale development projects |
Environmental Impact Assessment (EIA)
Before a project or product is developed or implemented, its potential environmental impacts are assessed using the Environmental Impact Assessment (EIA). EIA is usually used early in the design or project planning phase to anticipate and minimize negative environmental impacts, whereas LCA concentrates on assessing impacts throughout the product's lifecycle.
For power electronics, an EIA may examine the environmental hazards involved with establishing a new manufacturing facility, sourcing materials, or introducing new power electronics products to the market. EIA includes several important steps:
Screening and Scoping:While scoping identifies the specific environmental issues to be addressed, screening establishes if an EIA is required for a certain project. For example, scoping may concentrate on evaluating the energy needed for production or the emissions related to semiconductor fabrication in a power electronics manufacturing project.
Impact Prediction:This step involves predicting how a proposed action would affect the environment, such as the emissions from manufacturing a new type of inverter or the depletion of resources from the use of rare-earth materials in power semiconductors. Predicting the magnitude and significance of these impacts in advance of their occurrence is the aim.
Mitigation Measures:Identifying measures that reduce or mitigate the anticipated environmental effects is a requirement of the EIA. This could involve using less energy-intensive production techniques, utilizing environmentally friendly materials, or implementing renewable energy sources to supply electricity to manufacturing facilities in the power production facilities.
Monitoring and Reporting:EIAs include continuous monitoring after development to ensure environmental regulations are followed and to assess how well mitigation strategies are working. For instance, monitoring could involve assessing the recyclability of materials at the end of a product's life or measuring emissions during the manufacturing process.
Key Environmental Factors in LCA and EIA for Power Electronics
Several essential factors in power electronics are frequently addressed during both LCA and EIA.
Energy Consumption: Power electronics' operational efficiency is an essential factor in evaluating its life cycle since they are utilized to regulate and convert electrical energy. The overall environmental impact of devices such as motor drives, inverters, and converters is significantly impacted by the energy they consume during operation. The environmental effect can be significantly decreased by increasing energy efficiency through optimized design, such as by utilizing high-efficiency semiconductors or advanced control techniques.
Material Use and Resource Depletion: Significant environmental effects result from the extraction and processing of raw materials, especially metals such as aluminum, copper, and rare-earth elements. An LCA can help in finding opportunities to minimize resource consumption via lightweighting, material substitution, or enhanced recycling procedures.
Greenhouse Gas (GHG) Emissions: The manufacturing of power electronics, especially semiconductor fabrication, requires considerable amounts of energy and can generate significant greenhouse gas emissions. LCA and EIA help in measuring these emissions and identify where their impact can be mitigated by using cleaner procedures or renewable energy sources.
End-of-Life Management: LCA highlights how crucial it is to design products for appropriate disposal and recycling. To help in material recovery and reduce electronic waste (e-waste), power electronics components such as circuit boards, capacitors, and heat sinks should be made to be easily disassembled. The environmental effects of e-waste disposal or recycling facilities can also be explored through EIA.
Benefits of Lifecycle Analysis and Environmental Impact Assessment in Power Electronics
Informed Design Choices: For engineers to make environmentally informed design decisions, LCA and EIA provide crucial knowledge. For example, an LCA may reveal that a product's environmental effect can be significantly reduced by using a different material or increasing the energy efficiency of one component.
Regulatory Compliance: LCA and EIA are helpful tools for guaranteeing compliance with environmental standards (such as RoHS and WEEE) as they change. Companies can prevent fines and delays in the market by foreseeing and addressing regulatory requirements early in the design phase.
Sustainability and Market Differentiation: Sustainable products are becoming more and more sought after by industry and consumers. By showcasing a dedication to sustainability, the use of LCA and EIA can not only lessen the environmental impact but also give businesses a competitive edge.
Cost Savings: Although LCA and EIA may appear expensive at first, they often reveal opportunities to increase production efficiency, lower material costs, and cut waste, all of which result in long-term cost savings.
Case Example: Lifecycle Analysis in Power Electronics Manufacturing
An LCA was conducted by a power inverter manufacturer to evaluate the effects of its production process on the environment. According to the investigation, a large amount of the overall environmental impact was caused by the energy used in the production of semiconductors. The company lowered its overall greenhouse gas emissions by 25% by employing energy-efficient manufacturing practices and moving to a cleaner energy source. To reduce resource depletion and the expenses associated to acquiring raw materials, the LCA also found ways to recycle rare-earth metals utilized in the inverter's magnetic components.
Innovations and Case Studies in Eco-Friendly Power Electronics
The need for power electronics that are environmentally friendly and sustainable has led to important innovations in both product design and production techniques. These developments enhance the efficiency, reliability, and overall performance of power electronic devices while simultaneously reducing their environmental footprint. Manufacturers are increasingly producing products that satisfy market demands for sustainability as well as legal requirements by following eco-design principles and concentrating on reducing waste, energy use, and hazardous emissions. The main developments in environmentally friendly power electronics are explored in this section, along with case studies that show how these technologies are used in real-world situations.
Innovations in Eco-Friendly Power Electronics
Energy-Efficient Semiconductors:The reduction of energy consumption in power electronics has been significantly helped by developments in semiconductor materials. Wide-bandgap materials such as silicon carbide (SiC) and gallium nitride (GaN) are now being used in place of or in addition to traditional silicon-based devices. Power electronic devices can function at higher frequencies with reduced losses and increased reliability because to these materials' exceptional efficiency and thermal management abilities. In applications including high-frequency power supplies, renewable energy systems, and electric vehicles, wide-bandgap semiconductors have significantly reduced energy consumption.
Recycling and Reusing Materials:Power electronics component reuse and recycling are receiving more attention as part of the transition to sustainable manufacturing. By enabling the extraction of precious metals and components from electronic waste (e-waste), innovations in material recovery technologies minimize environmental damage brought on by mining and extraction and reduce the need for new raw materials. For instance, companies are developing methods to efficiently recover rare-earth elements used in semiconductors and magnets, guaranteeing the reuse of these valuable materials in future manufacturing cycles.
Biodegradable and Renewable Materials:The use of renewable and biodegradable materials in power electronics is becoming more popular in addition to recycling. In printed circuit boards (PCBs) and other components, researchers are developing new types of biodegradable polymers and plastics that can take the place of traditional materials. These materials reduce the long-term effects of discarded electronics by decomposing more easily in the environment. Renewable materials, such as bio-based polymers generated from plants, provide a more sustainable alternative to petroleum-based plastics.
Low-Energy Manufacturing Processes:Innovations in manufacturing processes are also helping to lower power electronics' carbon footprint. Power electronic components can be produced with minimal waste and energy consumption through low-energy manufacturing techniques such as additive manufacturing (3D printing). Compared to traditional subtractive manufacturing techniques, additive manufacturing minimizes material waste and energy consumption by enabling the accurate layer-by-layer fabrication of components. Because it does not require substantial tooling or machining, this technique is especially beneficial for the manufacturing of complex or unique components.
Table 11: Additive vs. subtractive manufacturing
Feature | Additive Manufacturing | Subtractive Manufacturing |
---|---|---|
Process | Builds objects layer by layer from materials | Removes material from a solid block using cutting tools |
Material Usage | Efficient, uses only the material needed | Can result in material waste |
Complexity | Allows for complex geometries without extra cost | Complex shapes require more effort and tooling |
Speed | Slower for large or high-volume production | Faster for simple parts or mass production |
Applications | Prototyping, custom parts, low-volume production | High-volume, precision parts, traditional manufacturing |
Smart Grid Integration and Energy Harvesting:An additional significant innovation in the drive for sustainability is the incorporation of power electronics into energy-harvesting systems and smart grids. To better manage energy distribution, reduce losses, and maximize the usage of renewable energy sources such as solar and wind, smart grids rely on advanced power conversion systems. Power electronics are combined with energy-harvesting technologies, which gather ambient energy from sources such as heat, light, or vibrations, to build self-sustaining systems requiring less external power sources.
Case Studies in Eco-Friendly Power Electronics
Case Study 1 - Solar Inverter with Recyclable Components: One of the top manufacturers of solar inverters has developed a new range of products that emphasizes recycling and energy efficiency. The inverters feature silicon carbide (SiC) semiconductors, which allow for improved energy conversion efficiency and less heat generation compared to regular silicon-based inverters. Additionally, the company used recyclable materials in the design of the PCB and inverter housing, which made it simpler to disassemble and retrieve valuable components at the end of the product's life. Significant operational and environmental cost reductions were attained by the company through the integration of energy-efficient components with an emphasis on recyclability.
Case Study 2 - Eco-Friendly Power Supplies for Data Centers: The high energy consumption of data centers has raised interest in developing environmentally friendly power supplies to meet the rising need for data storage and processing. The development of high-efficiency power supply units (PSUs) for data centers, which use GaN-based transistors to lower energy losses, is one significant innovation. The data center's power usage is greatly reduced by these PSUs, which run at an efficiency of over 98%. Furthermore, modular, recyclable components that are simple to upgrade or replace are incorporated into the PSU design, increasing system longevity and lowering e-waste.
Case Study 3 - Electric Vehicle (EV) Powertrain Recycling: Manufacturers of electric vehicles are increasingly focused on making powertrain components, such as inverters and battery management systems (BMS), more recyclable. For its EV powertrains, one automaker has implemented a closed-loop recycling program in which worn-out components are collected, disassembled, and repurposed into new products. Aluminum, copper, and rare-earth magnets are among the essential materials that are extracted and recycled in the production of new motors and inverters. By reducing the demand for raw materials, this method not only lessens the environmental impact of EV production but also lowers manufacturing costs overall.
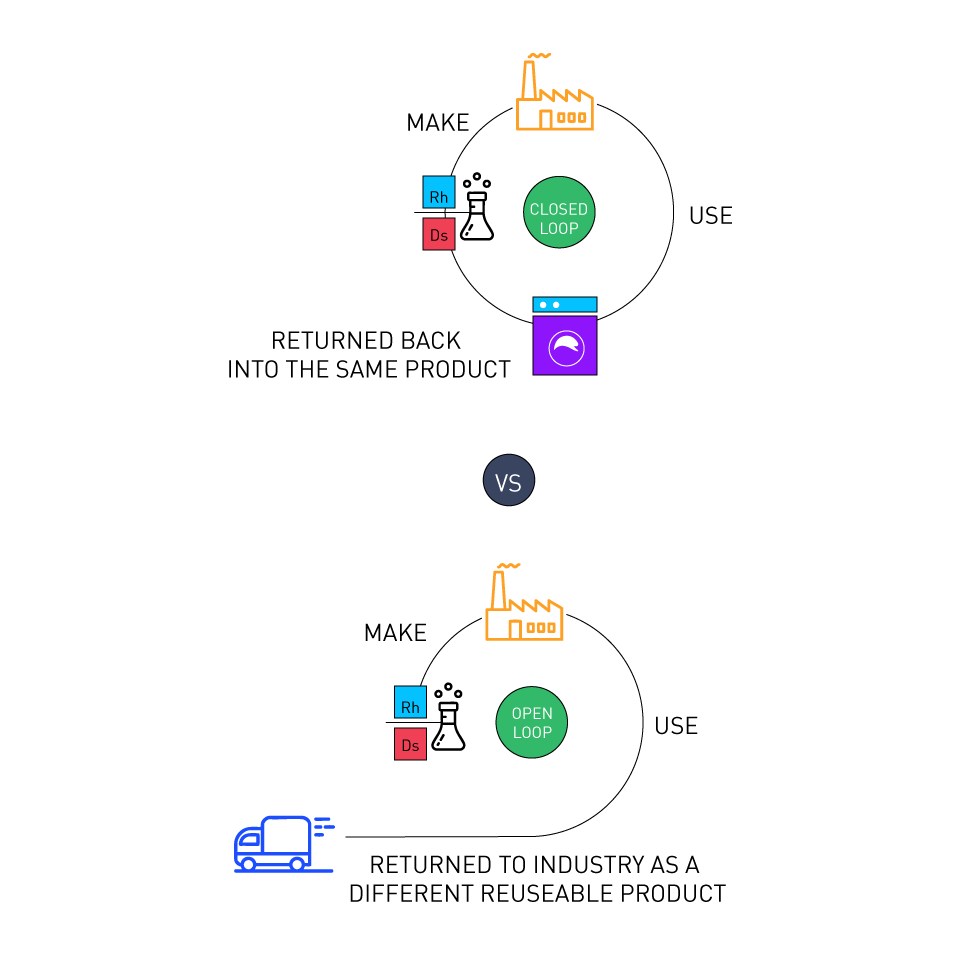
Figure 13: Closed-loop vs. open-loop recycling
Case Study 4 - Energy-Efficient Building Automation Systems: Energy-efficient power electronics are being used in the building automation industry to regulate lights, heating, ventilation, HVAC systems, and other electrical systems. Power electronics with integrated energy-harvesting technologies, which harvest energy from ambient sources such as solar power or kinetic motion, are a recent innovation. These systems can lower the building's overall energy consumption by self-powering some sensors and control units. Significant energy savings and a decrease in greenhouse gas emissions have resulted from the incorporation of energy-efficient power electronics into building automation systems.
The Role of Standards in Driving Eco-Friendly Innovation
Regulatory standards that require reductions in hazardous materials, energy consumption, and waste generation are frequently the driving force behind eco-design innovations. Regulations such as RoHS and WEEE have forced manufacturers to explore alternatives to hazardous materials and to implement procedures that promote recycling and waste reduction. Companies who adhere to these standards not only meet regulatory requirements, but also establish themselves as leaders in sustainable design.
Additionally, companies are encouraged to use systematic approaches to reduce environmental impacts across the lifecycles of their products by ISO 14001. This is because ISO 14001 is the international standard for environmental management systems. Many of the advancements in environmentally friendly power electronics mentioned above are the result of this framework's encouragement of ongoing environmental performance improvement.
Future Directions in Eco-Friendly Power Electronics
The power electronics industry will continue evolving as consumers demand greener products and environmental regulations tighten. The future of environmentally friendly power electronics will be shaped by innovations including the application of circular economy principles, the development of novel materials with less of an impact on the environment, and the integration of artificial intelligence (AI) for energy optimization. These developments will help companies comply with regulations while simultaneously meeting the increasing demand for energy-efficient and sustainable technologies in industries including data centers, electric vehicles, and renewable energy.
直接登录
创建新帐号