Power Electronics in Industrial Machinery and Automation
Power electronics are essential to the functioning and efficiency of automation systems and industrial machinery. These technologies enable precise control over a wide range of industrial operations by effectively regulating and converting electrical power. Power electronics are at the core of modern industrial systems, from motor drives to automated production lines, propelling advancements in process automation, energy management, and manufacturing.
Motor Drives and Motion Control
From robotic arms to conveyor belts, electric motors are the workhorses of industrial machinery. In order to ensure that these motors operate with maximum efficiency and accuracy, power electronics are essential for regulating their speed, torque, and position.
Variable Frequency Drives (VFDs): Variable Frequency Drives (VFDs) are one of the most popular industrial applications for power electronics. By altering the frequency and voltage applied to the motor, VFDs regulate the speed of AC motors. Applications requiring precise speed control, such as fans, pumps, and conveyor systems, rely on this ability. VFDs lessen energy consumption and wear on mechanical components by modifying the motor speed to match demand, which results in cheaper operating costs and a longer equipment lifespan.
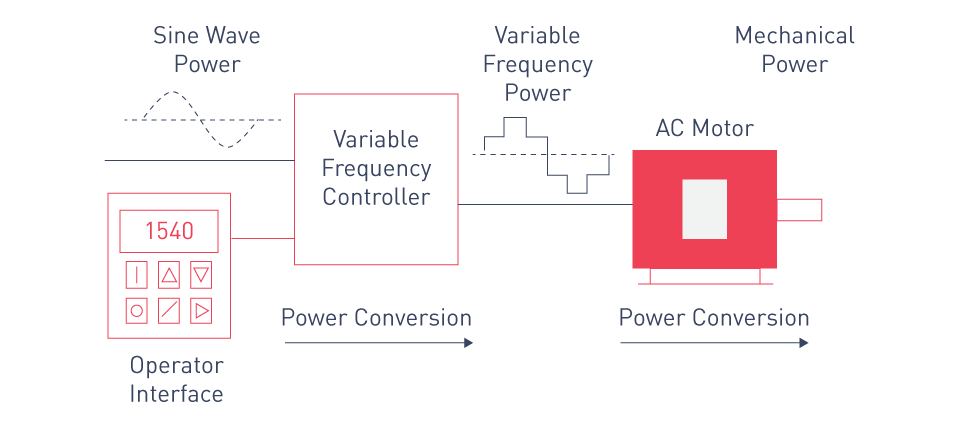
Figure 5: VFD system
Servo Drives and Robotics: Power electronics are utilized in servo drives to accurately control motor position and speed in more complex applications, including robotics and CNC machines. In order to accomplish the desired motion, servo drives apply real-time motor operating adjustments based on data from sensors, such as encoders or resolvers. This precise control is vital in applications requiring high accuracy and repeatability, such as robotic arms used for assembling, welding, and material handling.
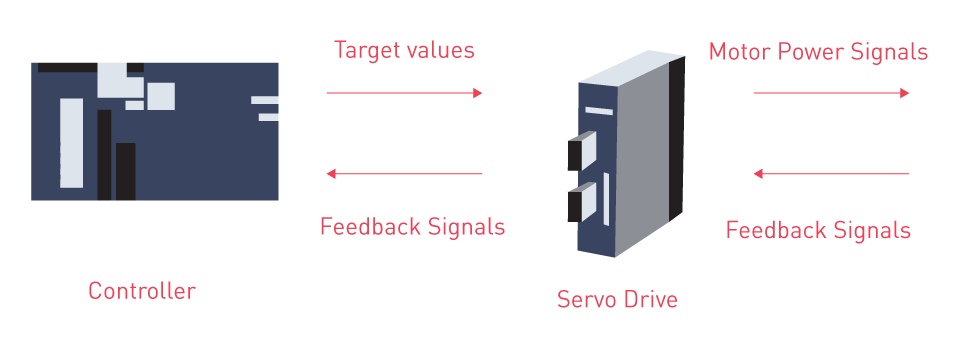
Figure 6: Servo system
Regenerative Braking: Motors in many industrial applications need to rapidly slow down or halt, which can generate extra energy. Regenerative braking, which converts this extra energy back into electrical power and feeds it back into the grid or stores it in batteries, is made possible by power electronics. This is a useful feature in applications like cranes, elevators, and electric vehicles because it not only increases energy efficiency but also reduces the wear on braking systems.
Power Conversion and Energy Management
Depending on the application, industrial machinery often requires power at various voltage levels and forms. Power electronics enable efficient conversion of electrical power to satisfy these requirements, guaranteeing the reliable and efficient operation of machinery.
AC/DC and DC/DC Converters: Power electronics are employed in converters in industrial settings to alter the electrical power's level and form. For example, the grid's AC power is converted into the DC power required for a number of industrial operations, including battery charging, welding, and electroplating, using AC/DC converters. To increase or decrease DC voltage levels to meet the requirements of particular components, such as sensors, controllers, and actuators, DC/DC converters are employed.
Power Factor Correction (PFC): Industrial machinery can introduce reactive power into the electrical system, resulting in low power factor and significant energy losses. Power Factor Correction (PFC) circuits use power electronics to increase power factor, decrease reactive power, and ease the burden on the electrical grid. Improving the power factor can result in significant energy savings and lower utility costs, which is especially essential in facilities with large inductive loads including motors and transformers.
Energy Storage and Management: In industrial environments, power electronics are also essential to energy storage systems, especially when it comes to applications that integrate renewable energy sources or uninterruptible power supplies (UPS). These systems use power electronics to control battery charging and discharging, guaranteeing optimal energy storage and availability when needed. Power electronics facilitate the smooth integration of renewable energy sources, such as wind turbines and solar panels, with manufacturing plants, maximizing energy efficiency and decreasing reliance on the grid.
Automation and Process Control
High levels of productivity, consistency, and safety are made possible by automation, which is an essential pillar of modern industrial operations. Power electronics are critical components in control systems that automate industrial operations ranging from assembly lines to material handling systems.
Programmable Logic Controllers (PLCs): PLCs are frequently used to operate machines and processes in industrial automation. Power electronics and PLCs operate together to control actuators, drive motors, and regulate the power supplied to different components. Power electronics, for example, govern the torque and speed of conveyor belts in an automated packing line, providing precise control over the flow of goods.
Distributed Control Systems (DCS): Distributed Control Systems (DCS) are used in large industrial facilities to monitor and manage complex operations including power generation, oil refining, and chemical manufacturing. The DCS's electrical and mechanical systems can be controlled in real time because of power electronics, which guarantees that operations are efficient and smooth. This involves controlling the power supplied to compressors, pumps, and other vital equipment in response to feedback from process controllers and sensors.
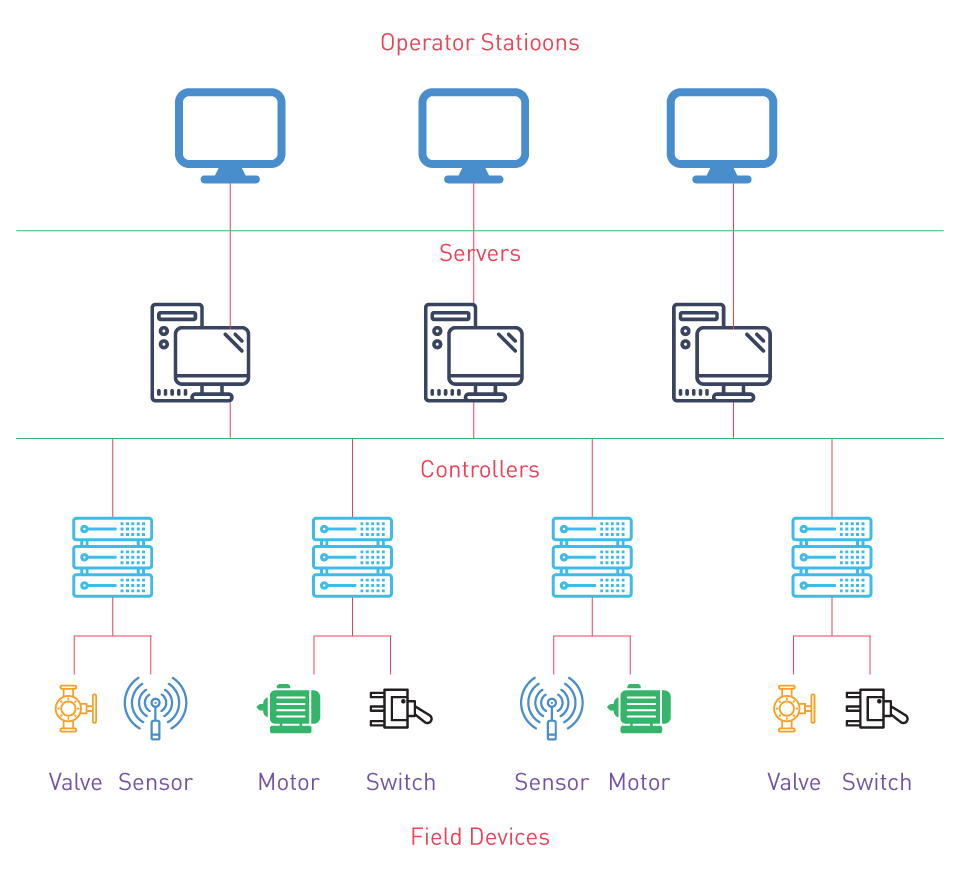
Figure 7: Distributed control system
Intelligent Sensors and Actuators: Intelligent sensors and actuators are now widely used in industrial automation as a result of Industry 4.0 and the Industrial Internet of Things (IIoT). For effective operation and communication with the central control system, these devices rely on power electronics. In predictive maintenance applications, for instance, smart sensors track the state of machinery and send data to the control system, which employs power electronics to modify operations and avert equipment failures.
Safety and Reliability
In industrial environments, where equipment failure can result in expensive downtime, damage, and even risks to human workers, reliability and safety are paramount. Power electronics' sophisticated protection and diagnostic capabilities help to ensure the reliability and safety of industrial machinery.
Overvoltage and Overcurrent Protection: For industrial machinery, power electronics offer crucial protection mechanisms that guard against overvoltage, overcurrent, and short-circuit conditions. Motor drives, converters, and control systems all have these safeguards built in to identify faults and take appropriate action, including turning off the machinery or disconnecting it from the power supply.
Redundancy and Fault Tolerance: Power electronics provide redundancy and fault tolerance in crucial industrial applications, guaranteeing that operations can continue on even in the case of a component failure. For instance, power electronics in a chemical plant's process control system can switch to alternate control paths or backup power sources to keep the system operating in the event of a malfunction, decreasing the possibility of a process disruption.
Thermal Management: To prevent overheating and guarantee the long-term reliability of industrial machinery, power electronics are also essential for thermal management. The equipment's lifespan is increased by advanced thermal protection circuits that monitor the temperature of power electronics components and modify operating conditions to avoid damage.
Control Technologies in Automotive Electronics
The need for sustainable transportation alternatives and the quick development of power electronics are driving a radical transition in the automotive sector toward electrification. At the front of this change are electric vehicles (EVs) and sophisticated battery management systems (BMS), which mainly rely on advanced control technologies to guarantee optimum performance, efficiency, and safety. With an emphasis on electric vehicles and battery management systems, this section examines the crucial role that control technologies play in automotive electronics.
Electric Vehicles (EVs)
Electric vehicles necessitate a new approach to power management and control since they represent a considerable shift from traditional internal combustion engine (ICE) vehicles. Efficient electrical energy conversion and control are at the center of EV operation, and power electronics are essential for controlling the drivetrain, charging systems, and general vehicle dynamics.
Inverter Control: An essential component of EVs is the inverter, which converts the battery's direct current (DC) into alternating current (AC) to power the electric motor. Inverters with advanced control technologies ensure smooth and efficient motor performance by controlling the voltage and frequency of the AC output. A popular technique called field-oriented control (FOC) meticulously controls the magnetic field inside the motor to maximize torque and speed. This improves vehicle's efficiency, acceleration, and overall driving experience.
Motor Control: To maximize efficiency and provide the required performance, electric motors in EVs need to be precisely controlled. Control systems use the driver's input and real-time conditions to regulate the motor's speed, torque, and power output. Regenerative braking systems, for example, employ control algorithms to convert the vehicle's kinetic energy during braking back into electrical energy, which is later stored in the battery. This increases the vehicle's driving range in addition to its energy efficiency.
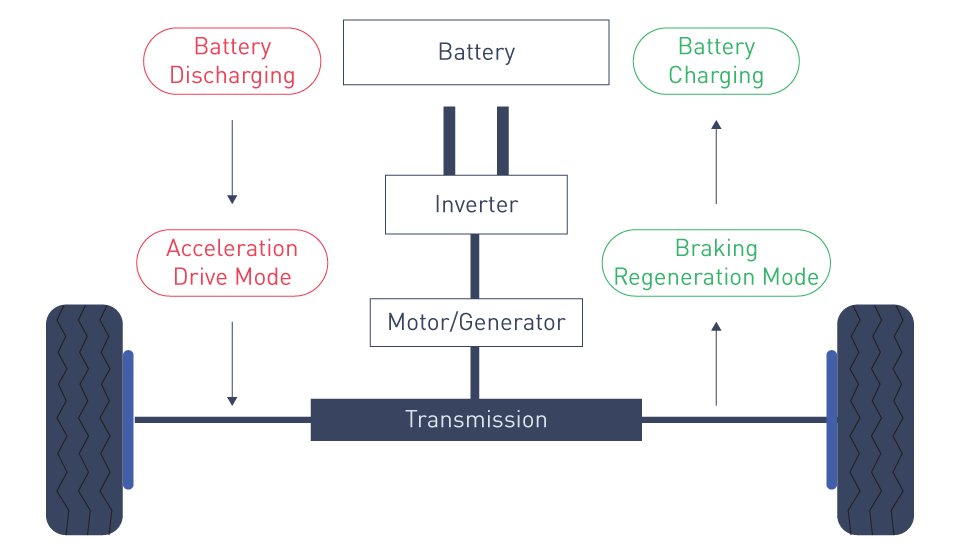
Figure 8: EV regenerative braking
Charging Control: For EVs to be practical and convenient, efficient charging is essential. In order to provide safe, fast, and efficient charging, control technologies in EV chargers regulate the flow of electricity from the grid to the vehicle's battery. Using algorithms, smart charging systems optimize the charging process according to factors such as battery state of charge, grid load, and electricity prices. This lowers expenses and reduces the strain on the electrical grid by allowing EV owners to charge their vehicles during off-peak hours.
Thermal Management: Significant heat is generated by EVs, especially when fast charging and high-performance driving are involved. To avoid overheating and guarantee the longevity of the vehicle's components, advanced thermal management systems are necessary. Control technologies monitor the battery, motor, and power electronics' temperatures and modify cooling systems as necessary. For example, high-performance EVs' liquid cooling systems use control algorithms to manage coolant flow in order to maintain optimum operating temperatures.
Battery Management Systems (BMS)
The battery is at the heart of an electric vehicle, and its performance, safety, and longevity are critical to the EV's overall success. Battery management systems (BMS) are advanced control systems that monitor and regulate the battery pack to guarantee long-term reliability, safe operation, and optimum performance.
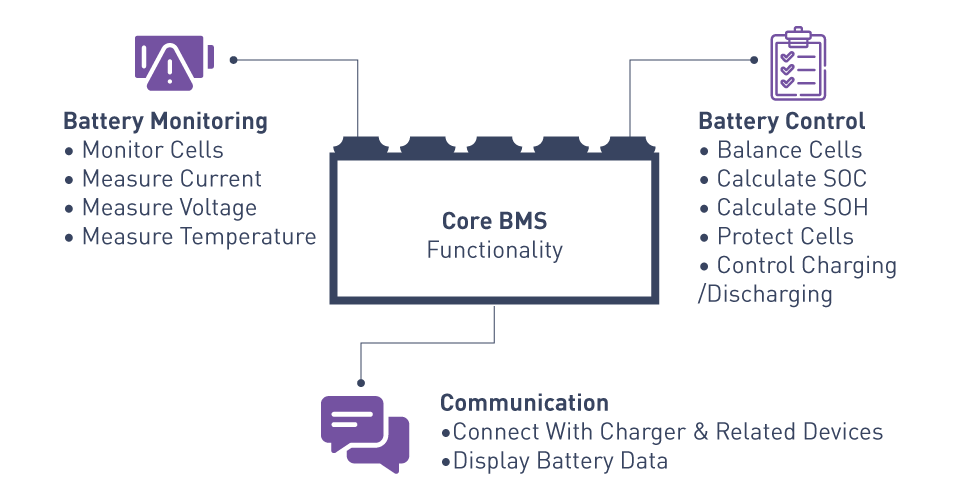
Figure 9: BMS functions
State of Charge (SoC) Estimation: Estimating the battery's state of charge (SoC) is one of a BMS's primary tasks. A battery's state of charge, represented as a percentage of its overall capacity, is known as the SoC. It shows the battery's remaining energy in relation to its maximum potential charge.
$$ \text{SoC} = \left( \frac{Q_{\text{Current}}}{Q_{\text{Max}}} \right) \times 100 $$
where SoC is State of Charge, QCurrent is Battery Current Charge (in Ampere-Hours or Ah), and QMax is Battery Maximum Capacity (in Ampere-Hours or Ah).
Managing the charging and discharging procedures and giving drivers accurate information about their remaining driving range rely on accurate SoC estimation. The BMS's control algorithms calculate the SoC in real time by analyzing data from temperature, voltage, and current sensors. Even in the face of changing load and environmental conditions, advanced techniques including machine learning and Kalman filtering are being employed more and more to increase the accuracy of SoC estimation.
State of Health (SoH) Monitoring: Apart from SoC, the BMS is in charge of monitoring the battery's state of health (SoH), which represents the pack's overall health and capacity. SoH monitoring involves assessing factors including internal resistance, capacity fade, and battery degradation. Control systems use this data to estimate how long the battery will last and to regulate the cycles of charging and discharging in order to increase battery life. This is especially crucial for preserving the vehicle's performance and over-time resale value.
Cell Balancing: EV battery packs are made up of multiple cells connected in parallel and series configurations. Some cells can become overcharged or overdischarged as a result of imbalances caused by variations in cell characteristics including capacity and internal resistance. This can reduce the battery pack's lifespan and overall efficiency. Control technologies in the BMS use cell balancing strategies to ensure that the state of charge is equal across all cells. Active balancing moves energy across cells to provide uniformity, whereas passive balancing releases excess energy from overcharged cells as heat. These methods guarantee the battery pack's safe and efficient operation.
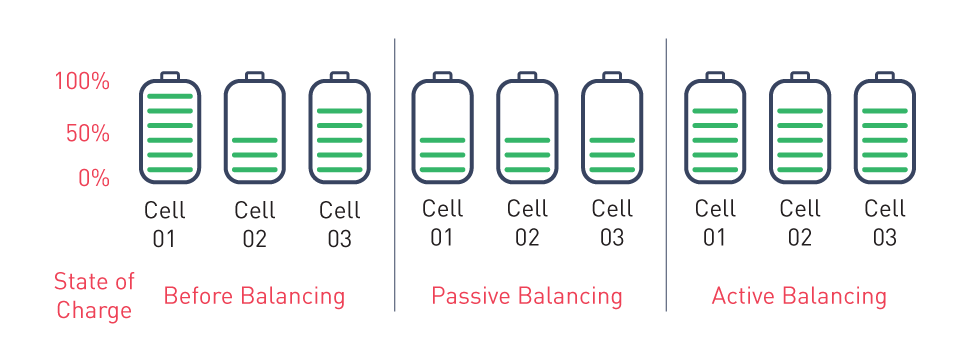
Figure 10: Cell balancing
Thermal Management in BMS: A crucial factor influencing battery safety and performance is temperature. Thermal management controls in the BMS monitors both the battery pack's overall temperature and the temperature of individual cells. The BMS modifies cooling systems, including fans or liquid cooling circuits, to disperse heat if the temperature rises above acceptable bounds. The BMS may also turn on heating elements to raise the battery's operational temperature in cold weather. By keeping the battery within its safe operating range, this thermal management prolongs battery life and prevents thermal runaway.
Safety and Fault Detection: With EV battery systems, safety is crucial since short circuits, deep discharges, and overcharging can result in hazardous situations like fires or explosions. The BMS uses advanced control technologies to identify potential faults and take appropriate action. To prevent damage from spreading, the BMS, for instance, might separate malfunctioning cells or modules from the rest of the battery pack. In order to reduce dangers, it also monitors for conditions such as overvoltage, undervoltage, overcurrent, and temperature anomalies. These safety measures are essential for both passenger protection and the vehicle's safe operation.
Future Trends in Automotive Control Technologies
Integration with Vehicle-to-Everything (V2X) Systems: Control systems in EVs and BMS are rapidly merging with Vehicle-to-Everything (V2X) systems as automotive technology advances. Real-time interactions between vehicles and the grid, other vehicles, and infrastructure are made possible by V2X communication, which enhances safety and facilitates efficient energy management. A BMS can utilize V2X data, for example, to optimize charging according to grid conditions or to take part in demand response programs, in which the battery of the vehicle returns energy to the grid during periods of high demand.
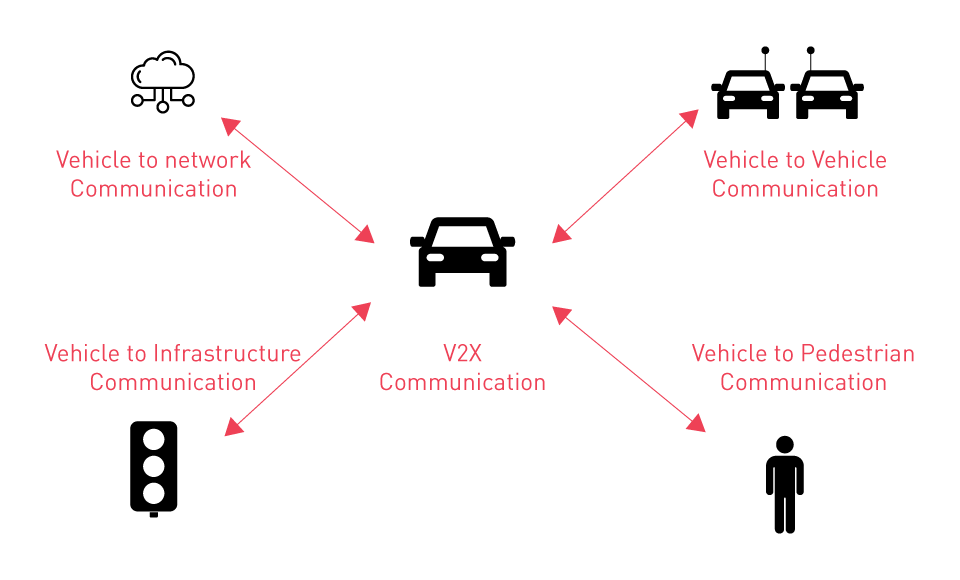
Figure 11: V2X communication
Autonomous Driving and Control Systems: The rise of autonomous driving technologies is placing new demands on automotive control systems. More advanced control systems are needed for autonomous electric vehicles in order to regulate not only energy and power but also the interactions between different sensors, actuators, and computer systems. To provide a safe and efficient driving experience, control technologies in autonomous EVs must provide smooth coordination between the drivetrain, battery management, and autonomous driving systems.
Wireless Charging and BMS: An emerging technology called wireless charging promises EV owners more convenience. In wireless charging configurations, control systems oversee the vehicle's alignment with the charging pad, power transfer efficiency, and BMS integration to maximize charging efficiency. This technology is a crucial area of development for the future of EVs since it needs precise control to improve charging efficiency while minimizing losses.
Emerging Trends and Challenges in Industrial and Automotive Power Electronics
Technological advances and the growing demand for reliable, sustainable, and efficient energy solutions in the industrial and automotive sectors are driving the rapid evolution of the power electronics field. Emerging innovations in power electronics are influencing how energy is converted, regulated, and used in the future as these industries experience new opportunities and challenges. With a focus on areas including wide bandgap semiconductors, electrification, digitalization, and the incorporation of renewable energy sources, this section explores the major developments and challenges in industrial and automotive power electronics.
Wide Bandgap Semiconductors: SiC and GaN
The adoption of wide bandgap (WBG) semiconductors, especially silicon carbide (SiC) and gallium nitride (GaN), is one of the most significant trends in power electronics. When compared to traditional silicon, these materials have better electrical and thermal properties, which allow for higher efficiency, faster switching speeds, and improved performance at high voltages and temperatures.
Benefits in Industrial Applications: SiC and GaN devices are utilized in industrial automation and machinery to improve the reliability and efficiency of inverters, power converters, and motor drives. Higher power densities are made possible by these semiconductors, which also improve thermal management and reduce the size and weight of power electronic systems. This is especially helpful in applications like robotics, renewable energy systems, and high-voltage power supplies where space is limited or where high efficiency is essential.
Benefits in Automotive Applications: SiC and GaN devices are revolutionizing electric vehicle (EV) powertrains in the automotive industry, including DC/DC converters, inverters, and onboard chargers. By enabling more efficient power conversion, these materials increase EVs' driving range and reduce charging times. The overall efficiency and reliability of automotive power electronics are further enhanced by their capacity to operate at higher temperatures, which eliminates the need for complex cooling systems.
Challenges: SiC and GaN semiconductor adoption is not without challenges, despite their advantages. These materials' higher price in comparison to silicon continues to be an obstacle, especially in sectors where costs are a concern. Furthermore, the production procedures for SiC and GaN devices are more complex and require specialized equipment and expertise. Reliability issues must also be addressed by engineers and manufacturers because these newer materials need extensive testing and validation in real-world applications and have different failure modes.
Electrification and Energy Efficiency
One of the main forces behind power electronics innovation is the global quest for electrification and higher energy efficiency. Reducing energy consumption, lowering carbon emissions, and incorporating renewable energy sources are becoming more and more essential in the industrial and automotive sectors.
Industrial Electrification: Traditional mechanical and hydraulic systems are being replaced by electrically powered equivalents in industrial settings as a result of electrification. For example, hydraulic actuators in machinery are gradually being replaced by electric motors, which improve control, efficiency, and precision. In order to provide efficient energy conversion and enable advanced control strategies like variable speed drives and regenerative braking, power electronics are essential to the management of modern electric systems.
Automotive Electrification: Electric vehicles (EVs) and hybrid electric vehicles (HEVs) are the most obvious examples of the automobile industry's electrification trend. Power electronics are necessary to optimize performance, increase the vehicle's range, and control the energy transfer between the battery, motor, and other components. With an emphasis on reaching higher power densities and lowering energy losses, innovation in this field is being driven by the need for more compact and efficient power converters, inverters, and battery management systems.
Challenges: The move to electrification poses multiple challenges. Electric system integration in industrial applications frequently necessitates significant modifications to the existing infrastructure, which can result in expensive upfront expenses and potential operational disruptions. High-performance batteries and efficient power electronics are essential in the automotive industry, but these components also need to adhere to strict safety and reliability standards. Research on alternative materials and recycling techniques are also being prompted by growing concerns about the sustainability and availability of the materials used in batteries and power electronics.
Digitalization and Smart Systems
Power electronics are transforming because of digitalization and the Internet of Things (IoT), making systems in industrial and automotive applications smarter and more connected. Power electrical devices are incorporating digital control systems, advanced sensors, and real-time data analytics to increase accuracy, adaptability, and efficiency.
Smart Industrial Systems: Digitalization in industrial settings is resulting in the development of "smart factories," which utilize power electronics to monitor and regulate energy consumption in real-time. Machine learning and advanced control algorithms are being used to optimize industrial machinery performance, lowering energy consumption and increasing process efficiency. Additionally, power electronics are essential to predictive maintenance, which uses sensor data to predict equipment failures and plan maintenance before expensive downtime occurs.
Connected Automotive Systems: In the automotive industry, digitalization enables the development of connected vehicles that communicate with one another and with the surrounding infrastructure. In order to control the energy flow in these interconnected systems and guarantee the safe and efficient operation of vehicles, power electronics are essential. Digital control systems, for example, optimize energy use and increase the range of electric vehicles by managing the interaction between the battery, motor, and charging infrastructure. Furthermore, power electronics are being included into autonomous driving and advanced driver assistance systems (ADAS) to help manage the energy requirements of sensors, processors, and actuators.
Challenges: The integration of complex systems, the need for real-time data processing, and cybersecurity threats are some of the challenges associated with the digitalization of power electronics. Because cyberattacks could interfere with operations or jeopardize safety, it is crucial to ensure the security of networks and connected devices in industrial applications. Digital systems and power electronics must be seamlessly integrated in the automotive sector to guarantee reliable and safe operation, especially in autonomous vehicles. Furthermore, these systems' growing complexity necessitates advanced software development and validation procedures, which can be expensive and time-consuming.
Integration of Renewable Energy Sources
New power electronics technologies are being developed as a result of the expanding trend of integrating renewable energy sources, such wind and solar, into industrial and automotive applications. Power electronics are crucial for regulating and converting the energy produced by these renewable sources as both consumers and industries want to reduce their carbon footprint.
Renewable Energy in Industrial Applications: Renewable energy sources are being incorporated into power systems in industrial settings in an effort to lower reliance on fossil fuels and save energy expenses. Power electronics convert the variable output of renewable energy sources into a stable and usable form that satisfies the demands of industrial machinery. Solar inverters, for example, convert the DC power produced by photovoltaic panels into AC power that can be fed into the grid or utilized by industrial equipment. Furthermore, energy storage devices like batteries and supercapacitors use power electronics to store excess energy generated by renewable sources and release it when needed.
Renewable Energy in Automotive Applications: Renewable energy is being incorporated into electric vehicles (EV) charging infrastructure in the automotive industry. Managing the energy flow between EV batteries and renewable energy sources such as solar panels necessitate power electronics. For example, power electronics are used in solar-powered charging stations to transform the DC power produced by solar panels into either the DC power required by EV batteries or the AC power needed by the grid. This incorporation improves the sustainability of the entire energy system in addition to lowering the carbon footprint of EVs.
Challenges: The integration of renewable energy sources into industrial and automotive applications poses a number of challenges. Power electronics systems must be extremely flexible and able to handle variations in the energy supply due to the intermittent nature of renewable energy, such as the unpredictability of solar and wind power. In industrial contexts, establishing the compatibility of renewable energy with existing power systems can be difficult and expensive. The development of reliable and efficient renewable energy-based charging infrastructure is essential for automobile applications, especially in isolated or off-grid locations. True sustainability also requires careful management of the lifecycle and environmental impact of renewable energy technologies, including the production and disposal of batteries and solar panels.
Case Study: Integration of Power Control Systems in a Manufacturing Setting
Power control system integration in manufacturing environments has completely changed how businesses control energy consumption, boost production, and ensure operational reliability. The application of advanced power control systems in a modern manufacturing environment is examined in this case study, with focus on how these systems are employed to maximize machinery performance, boost energy efficiency, and guarantee reliability of the system.
Overview of the Manufacturing Environment
Manufacturing Facility: A large-scale manufacturing facility that specializes in the production of automotive components is the subject of the case study. The facility operates a variety of machinery, such as industrial presses, conveyors, robotic assembly lines, and CNC machines, all of which require precise electrical power control to operate at peak efficiency and performance.
Challenges: The facility has multiple challenges common to high-demand industrial environments, including the need to reduce energy usage, and downtime, and maintain high levels of production quality. One potential answer to these challenges is the integration of power control systems, which would allow the facility to maximize its energy consumption while preserving reliable and consistent operation.
Integration of Variable Frequency Drives (VFDs)
One of the key components of the facility's power control technique is variable frequency drives or VFDs. VFDs are used to regulate the torque and speed of electric motors that power essential machinery including conveyors and CNC machines. VFDs allow the facility to tailor the motor speed to the specific demands of each production process by modifying the frequency and voltage applied to the motors.
Energy Efficiency: The manufacturing processes' energy efficiency has increased dramatically after VFDs were integrated. VFDs, for example, allow the motors in conveyor systems to operate at reduced speeds when maximum production capacity is not needed, which lowers energy usage. In addition to reducing energy expenses, this ability of dynamically modify motor speed in response to real-time demand also prolongs the motors' lifespan by minimizing wear and tear.
Process Optimization: VFDs give precise control over spindle speeds in CNC machining, enabling the best possible cutting conditions for different materials and machining tasks. This enhances the quality of the finished components, lowers tool wear, and improves machining accuracy. Furthermore, the smooth acceleration and deceleration of robotic arms is guaranteed by the use of VFDs in robotic assembly lines. This is essential for preserving precise assembly processes and avoiding mechanical stress on the equipment.
Implementation of Programmable Logic Controllers (PLCs)
A key component of the facility's power control approach are programmable logic controllers, or PLCs. The coordination of VFDs, sensors, and actuators is one of the many machines and processes that PLCs are used to automate and control. PLC integration makes it possible to centrally manage power control systems, facilitating real-time manufacturing process monitoring and adjustment.
Centralized Control and Monitoring: The facility's PLCs are connected to a centralized control system that monitors the status and operation of all machines. This system gives operators a thorough understanding of the manufacturing process by gathering data on power usage, motor speeds, production output, and machine health. Rapid response to any issues, such as equipment failures or changes in production quality, is made possible by this real-time monitoring ability.
Improved Reliability and Reduced Downtime: Using predictive maintenance strategies is one of the main advantages of incorporating PLCs into power control systems. The PLCs can detect early signs of wear or potential failure by continuously monitoring the operation of the machinery, enabling maintenance to be performed before a breakdown happens. The facility's downtime has been significantly decreased because of this predictive maintenance strategy, which also helps to avoid expensive unplanned repairs and maintain production schedules.
Energy Management and Power Factor Correction
For the manufacturing facility to accomplish sustainability goals and save money, efficient energy management is essential. Power factor correction (PFC) and load balancing are two advanced energy management strategies that the facility has been able to apply because of the integration of power control systems.
Power Factor Correction (PFC): Power factor is a measure of how efficiently electrical power is used. For the facility's electrical system to operate more efficiently, power factor correction is necessary. The facility has installed PFC systems, which minimize energy losses and reduce reactive power by correcting the electrical load's power factor using capacitors. This contributes to a more stable and reliable power supply by lowering electricity costs and lessening the load on the electrical grid.
Load Balancing and Demand Response: The facility's power control systems are also employed to distribute the electrical load evenly across various machines and operations. This load-balancing feature lowers the chance of power outages and helps keep the electrical system from overloading. The facility additionally participates in demand response programs, which help stabilize the grid during times of peak demand by adjusting power usage through control systems that receive signals from the utility company.
Integration of Renewable Energy Sources
The industrial facility has included solar panels and other renewable energy sources into its power infrastructure as part of it's commitment to sustainability. In order to manage the energy flow between the grid, the facility's machinery, and renewable sources, power control systems are essential.
Solar Power Integration: The facility has installed solar panels on its rooftops, which provide a considerable amount of its electrical requirements. Converting the DC power produced by the solar panels into AC power that the facility's machinery can use is the responsibility of the power control systems. These systems also control how solar energy is distributed, giving priority to its usage during periods of highest production and storing extra energy in battery systems for later use.
Hybrid Energy Management: The facility's implementation of renewable energy sources has also allowed it to install a hybrid energy management system. The power control systems optimize energy consumption according to cost and availability by dynamically balancing the use of solar power, grid power, and battery storage. In addition to lowering the facility's reliance on fossil fuels, this hybrid approach ensures that essential machinery functions continuously by offering a backup power source in the event of grid failures.
直接登录
创建新帐号